Formy wtryskowe – Definicja, Budowa, Produkcja, Rodzaje
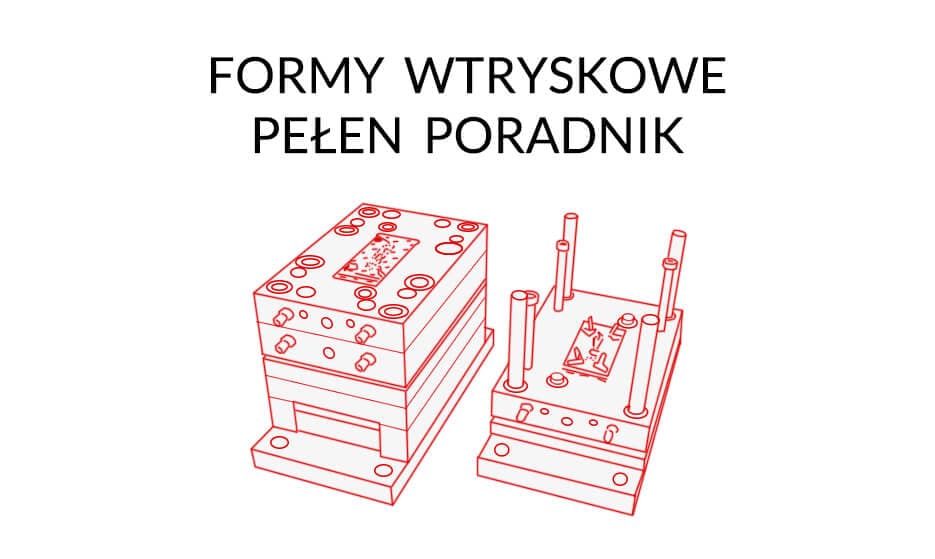
Czym są formy wtryskowe?
Formy wtryskowe to specjalistyczne narzędzia wykorzystywane w procesie wtryskiwania tworzyw sztucznych, które odgrywają kluczową rolę w masowej produkcji złożonych i precyzyjnych elementów z plastiku. Są one nieodzowne w wielu gałęziach przemysłu - od motoryzacji, przez medycynę, aż po elektronikę.
Forma wtryskowa to zasadniczo stalowy lub aluminiowy blok, wewnątrz którego znajdują się jedna lub więcej szczegółowo wyfrezowanych półprzestrzeni, nazywanych gniazdami. Właśnie do nich tworzywo sztuczne jest wtryskiwane pod wpływem wysokiej temperatury i ciśnienia, przyjmując pożądaną formę.
Wtryskiwanie pozwala na osiągnięcie wysokiej dokładności wymiarowej oraz powtarzalności, co jest niezbędne w produkcji na szeroką skalę.
Z jakich elementów zbudowana jest forma wtryskowa?
Forma wtryskowa zbudowana jest z kilku kluczowych elementów, które razem tworzą system umożliwiający efektywną i powtarzalną produkcję:
- Gniazdo formujące - Kluczowy komponent każdej formy, który determinuje kształt i detale wypraski. Gniazdo może być pojedyncze lub wielokrotne. W drugim przypadku pozwala na wytwarzanie wielu części podczas jednego cyklu wtrysku.
- Układ wlewowy - System kanałów, który prowadzi roztopione tworzywo sztuczne z wtryskarki do gniazd formujących. W zależności od konstrukcji układ wlewowy może być zimnokanałowy lub gorącokanałowy.
- Układ chłodzenia formy i wypraski - Składa się z sieci kanałów chłodzących, które regulują temperaturę formy, czym zapewniają odpowiednie warunki dla procesu krzepnięcia tworzywa i skracają cykl produkcyjny.
- Układ wypychania wypraski - Mechanizm umożliwiający automatyczne wyjmowanie gotowego produktu z formy, co zwiększa efektywność produkcji.
- Układ usuwania wlewka - Pozwala na oddzielenie wlewków (nadmiaru tworzywa) od finalnych wyrobów, co jest kluczowe dla estetyki i funkcjonalności gotowych części.
- Elementy prowadzące i ustalające połówki formy - Dbają precyzyjne dopasowanie i ruch obu części formy, dzięki czemu możliwe jest zachowanie wymaganych tolerancji i jakości produktu.
- Napędy płyt i segmentów - Mechanizmy kontrolujące ruch różnych części formy, w tym segmentów ruchomych czy rdzeni, które mogą tworzyć złożone geometrie w wypraskach.
- Obudowa - Zewnętrzna struktura formy, która zapewnia ochronę i wsparcie dla wewnętrznych komponentów, a także umożliwia montaż formy we wtryskarce.
Formy mogą różnić się konstrukcją w zależności od potrzeb produkcyjnych. Na przykład proste formy jednogniazdowe idealnie sprawdzą się w produkcji małoseryjnej. Z kolei skomplikowane wielogniazdowe układy z kilkoma płaszczyznami podziału ułatwiają wytwarzanie szeregu części na raz w procesie wieloseryjnym.
Różnorodność typów form pozwala na dostosowanie procesu produkcji do specyficznych wymagań dotyczących jakości, ilości i złożoności wyrobów końcowych.
Jak projektowane są formy wtryskowe?
Formy wtryskowe projektowane są wieloetapowo. Kolejne kroki tego procesu obejmują:
- wykonanie projektu wyrobu końcowego,
- stworzenie projektu formy,
- przygotowanie formy,
- próby i dopracowania,
- próby końcowe.
Poniżej opisujemy każdy z etapów.
Wykonanie projektu wyrobu końcowego
Pierwszym krokiem w projekcie formy wtryskowej jest stworzenie projektu detalu, który ma być wytwarzany. Zazwyczaj służy do tego oprogramowanie CAD 3D. To właśnie za jego pomocą inżynierowie przygotowują zarówno dwu-, jak i trójwymiarowe modele przedmiotu.
Jeśli kształt detalu jest skomplikowany, projekt może wymagać pogłębionej analizy pod kątem realnej funkcjonalności finalnego produktu i możliwości jego masowego wytwarzania.
Na tym etapie uwzględnia się także wszelkie wymagania techniczne i estetyczne, które wypraski mają spełniać.
Stworzenie projektu formy
Po przygotowaniu projektu detalu i konsultacjach z klientem odnośnie specyficznych wymagań dla danego wyrobu inżynierowie przechodzą do projektowania formy.
Najpierw wybierają jej typ (np. gorąco- lub zimnokanałowa, jedno- lub wielogniazdowa) w zależności od przewidywanej wielkości produkcji oraz aspektów ekonomicznych. Potem przechodzą do samego projektu formy, który obejmuje szczegółowe rozmieszczenie kanałów wlewowych, układu chłodzenia formy wtryskowej oraz systemów wypychających. Każdy z tych elementów jest niezbędny dla optymalnego procesu wtrysku.
Przygotowanie formy
Kolejnym etapem jest wykonanie fizycznej formy. Wiele komponentów, takich jak standardowe elementy mocujące czy prowadzące, można nabyć od specjalizujących się w tym producentów, co obniża koszty i skraca czas produkcji. Jednak kluczowe części, takie jak gniazda formujące, wymagają indywidualnego wykonania.
Próby i dopracowania
Po złożeniu wszystkich elementów przechodzi się do etapu pierwszych prób wtryskiwania. Pozwalają one ocenić, czy forma spełnia wszystkie oczekiwania i czy wypraski mają odpowiednią jakość.
Na tym etapie często pojawiają się potrzeby drobnych poprawek, takich jak modyfikacja kanałów chłodzenia czy dostosowanie systemów wypychających, co jest niezbędne do optymalizacji procesu produkcji.
Próby końcowe
Po wprowadzeniu wszystkich poprawek forma jest wysyłana do klienta, gdzie przeprowadzane są próby końcowe na docelowych stanowiskach produkcyjnych. To ostateczny test, który decyduje, czy forma jest gotowa do rozpoczęcia masowej produkcji.
Jak produkowane są formy wtryskowe?
Formy wtryskowe są produkowane etapami, z których każdy wymaga precyzyjnej inżynierii i starannej realizacji projektu. Oto kroki, które składają się na ten złożony proces:
- podział na elementy formujące,
- konstrukcja elementów formujących,
- zabudowa korpusu formy,
- projektowanie układu doprowadzenia tworzywa,
- projektowanie układu chłodzenia,
- projektowanie układu wypychania,
- stworzenie symulacji wtrysku,
- konstrukcja elementów funkcjonalnych formy,
- konstrukcja dodatkowych elementów,
- stworzenie listy materiałowej BOM,
- wykonanie rysunku zestawieniowego oraz rysunków wykonawczych,
- montaż formy we wtryskarce.
Poniżej opisujemy każdy z nich.
Podział na elementy formujące
Produkcja formy wtryskowej zaczyna się od podziału na elementy formujące, które są odpowiedzialne za nadanie kształtu gotowemu produktowi. Każdy z tych elementów, zwanych też gniazdami, jest projektowany tak, aby dokładnie odwzorowywał geometrię wyrobu.
Konstrukcja elementów formujących
Projektowanie elementów formujących jest kluczowe, ponieważ muszą one wytrzymać wysokie temperatury i ciśnienie procesu wtrysku. Zwykle wykonuje się je ze stali narzędziowej lub innego tworzywa o wysokiej odporności na ścieranie i uszkodzenia.
Zabudowa korpusu formy
Korpus formy stanowi "szkielet", do którego wszystkie inne elementy są mocowane. Musi być wystarczająco mocny, aby wytrzymać ciśnienia i temperatury podczas wtrysku oraz zapewnić stabilność całej konstrukcji.
Projektowanie układu doprowadzenia tworzywa
Układ doprowadzenia tworzywa jest projektowany w taki sposób, aby roztopione tworzywo sztuczne mogło być równomiernie rozprowadzone do wszystkich części formy. Zależnie od projektu może być on gorącokanałowy lub zimnokanałowy.
Projektowanie układu chłodzenia
Układ chłodzenia formy wtryskowej jest niezbędny do szybkiego schładzania wyprasek, co pozwala na skrócenie cyklu produkcyjnego i zwiększenie jakości gotowych produktów. Kanały chłodzące rozmieszcza się w strategicznych miejscach formy.
Projektowanie układu wypychania
Układ wypychania jest konieczny do usunięcia wystudzonej wypraski z formy. Projektuje się go tak, aby zapewnić łatwe i bezpieczne wyjęcie produktu bez uszkodzenia go.
Stworzenie symulacji wtrysku
Symulacja wtrysku pozwala przewidzieć, jak tworzywo będzie się zachowywać podczas procesu wtrysku, co umożliwia optymalizację konstrukcji formy przed jej wykonaniem.
Konstrukcja elementów funkcjonalnych formy
Elementy takie jak układ doprowadzenia tworzywa, układ chłodzenia i układ wypychania są integralną częścią konstrukcji formy. Ich precyzyjne zaprojektowanie jest kluczowe dla funkcjonalności i efektywności formy.
Konstrukcja dodatkowych elementów
Do formy często dodaje się również inne elementy, takie jak prowadnice czy zamki, które pomagają w utrzymaniu jej w stanie zamkniętym podczas wtrysku.
Stworzenie listy materiałowej BOM
Lista materiałowa BOM (Bill of Materials) jest kompleksowym zestawieniem wszystkich materiałów i komponentów potrzebnych do budowy formy, co umożliwia efektywne planowanie i zakupy.
Wykonanie rysunku zestawieniowego oraz rysunków wykonawczych
Rysunki te są niezbędne dla dokładnego zmontowania formy, ponieważ zawierają wszystkie wymiary, tolerancje oraz specyfikacje techniczne.
Montaż formy we wtryskarce
Ostatnim etapem jest montaż gotowej formy we wtryskarce. Musi być on wykonany z najwyższą precyzją, aby zapewnić prawidłowe funkcjonowanie całego systemu.
Czym są normalia w formach wtryskowych?
Normalia w formach wtryskowych to standardowe, gotowe komponenty form, takie jak wypychacze, prowadnice, tuleje czy sprężyny, które są dostępne w handlu i mogą być używane w wielu różnych formach. Użycie normaliów pozwala na obniżenie kosztów i skrócenie czasu produkcji form, ponieważ eliminuje potrzebę projektowania i wykonywania tych elementów od podstaw. Normalia ułatwiają również konserwację i naprawy, bo uszkodzone części można łatwo wymienić na nowe, standardowe komponenty.
Jakie materiały są wykorzystywane do tworzenia form wtryskowych?
Do tworzenia form wtryskowych najczęściej wykorzystuje się stal, aluminium czy stopy miedzi. Poniżej przedstawiamy najważniejsze ich cechy:
- Stal - Materiał najczęściej stosowany ze względu na jego wytrzymałość i zdolność do utrzymywania wysokiej precyzji nawet po wielokrotnym użyciu. Stal jest używana zarówno do konstrukcji głównych elementów formy, jak i gniazd formujących.
- Aluminium - Wybierane przede wszystkim ze względu na lekkość i szybkość obróbki, co czyni je idealnym do produkcji prototypów i krótkich serii produkcyjnych. Aluminium jest jednak mniej odporne na zużycie w porównaniu do stali, co oznacza, że formy szybciej ulegają degradacji.
- Stopy miedzi - Wykorzystywane ze względu na doskonałe właściwości przewodzenia ciepła, co umożliwia efektywniejsze chłodzenie formy. Jest to szczególnie ważne w szybkich cyklach produkcyjnych.
- Inne materiały - W zależności od specyfiki produkcji i wymagań technicznych producenci wykorzystują także różne tworzywa sztuczne, ceramikę lub specjalne stopy odporne na korozję.
Jaka stal na formy wtryskowe?
Na formy wtryskowe najlepsza jest stal narzędziowa ze względu na jej wysoką odporność na ścieranie, zdolność do utrzymania ostrości krawędzi oraz wytrzymałość na pęknięcia. Popularne typy stali używane do form wtryskowych aplikacji to:
- Stal 1.2083 - Stal narzędziowa stopowa, nierdzewna, przystosowana do pracy na zimno. Charakteryzuje się doskonałą stabilnością wymiarową podczas ulepszania cieplnego i jest idealna do formowania tworzyw agresywnych chemicznie, jak PCV. Doskonale nadaje się również do produkcji elementów optycznych.
- Stal 1.2085 - Wysokochromowa stal narzędziowa o dużej odporności na korozję, co czyni ją szczególnie przydatną do formowania tworzyw sztucznych. Ma poprawione właściwości mechaniczne w porównaniu do stali 1.2083, jednak jest trudniejsza w polerowaniu.
- Stal 1.2311 (P20) - Uniwersalnie stosowana stal narzędziowa, która często służy do produkcji korpusów i wkładek form wtryskowych. Charakteryzuje się średnią hartownością, dużą twardością, dobrą skrawalnością i odpornością na ścieranie.
- Stal 1.2312 (PS+S) - Podobna do stali 1.2311, ale z dodatkiem siarki, co zwiększa jej skrawalność kosztem pogorszonych możliwości polerowania. Jest dostarczana w stanie ulepszonym cieplnie, co eliminuje potrzebę późniejszej obróbki cieplnej.
- Stal 1.2738 - Jest to modyfikacja stali P20 z dodatkiem niklu, co skutkuje większą twardością przez całą grubość materiału. Materiał cechuje się dobrą skrawalnością, a ponadto jest odpowiedni do teksturowania i polerowania. Często stosuje się go do dużych form wtryskowych.
- Stal 1.2767 - Stal narzędziowa do pracy na zimno, odporna na uderzenia i z dużą hartownością oraz ciągliwością. Doskonała do matryc, stempli i narzędzi do bicia monet, a także do elementów form, które wymagają wysokiej wytrzymałości.
Wybór odpowiedniego rodzaju stali zależy od specyfiki procesu produkcyjnego, rodzaju wytwarzanego produktu oraz oczekiwanego cyklu życia formy.
Jakie maszyny są potrzebne do wykonania formy wtryskowej?
Do wykonania formy wtryskowej potrzebne są różne maszyny i urządzenia, które cechują się wysoką precyzją i efektywnością procesu produkcji jak frezarki CNC. elektrodrążarki czy wytaczarki. Poniżej przedstawiamy najważniejsze z nich:
- Frezarki CNC (Computer Numerical Control) - Podstawowe narzędzia do produkcji form wtryskowych, które pozwalają na precyzyjną obróbkę metali z dużą dokładnością. Frezarki CNC służą do tworzenia skomplikowanych kształtów i detali, w tym gniazd formujących i systemów wypychających. Ich zdolność do wykonania złożonych operacji frezowania, wiercenia i gwintowania jest kluczowa.
- Elektrodrążarki - Maszyny niezastąpione w przypadku obróbki trudno dostępnych, bardzo twardych lub skomplikowanych części form. Ich technologia pozwala na usuwanie materiału za pomocą elektroerozji, co jest szczególnie przydatne przy tworzeniu precyzyjnych detali, które trudno wykonać tradycyjnymi metodami.
- Szlifierki - Umożliwiają uzyskanie wyjątkowo gładkich powierzchni, co jest niezbędne dla zapewnienia wysokiej jakości wyprasek i łatwości wypuszczania ich z formy. Szlifowanie jest również stosowane do finalnego wykończenia gniazd formujących oraz elementów prowadzących i ustalających.
- Wytaczarki - Wykorzystuje się je do obróbki otworów o dużych średnicach, gdzie wymagana jest wysoka precyzja. Są niezbędne do wykonania elementów takich jak otwory pod wypychacze czy systemy chłodzące formy.
- Maszyny do obróbki elektrochemicznej - W niektórych specyficznych zastosowaniach, gdzie tradycyjne metody obróbki są niewystarczające, stosuje się maszyny do obróbki elektrochemicznej. Pozwalają one na usuwanie materiału w sposób kontrolowany bez kontaktu fizycznego, co minimalizuje ryzyko deformacji.
- Obrabiarki laserowe - W przypadkach wymagających szczególnie precyzyjnej i delikatnej obróbki, takiej jak cienkie detale, tekstury czy mikro-gniazda, stosuje się obrabiarki laserowe. Technologia laserowa pozwala bowiem na precyzyjne cięcie, wiercenie i grawerowanie bez ryzyka uszkodzenia obrabianego materiału.
- Narzędzia pomiarowe - Dokładne narzędzia pomiarowe, takie jak współrzędnościowe maszyny pomiarowe (CMM), spektrometry czy twardościomierze, są niezbędne w całym procesie produkcji form. Zapewniają bowiem zgodność wymiarów z projektami i wysoką jakość wykonania.
Jakie są metody produkcji form wtryskowych?
Najpopularniejsze metody produkcji form wtryskowych to obróbka CNC, obróbka elektroerozyjna (EDM), obróbka laserowa, odlewanie próżniowe, gięcie i spawanie, obróbka chemiczna.
Poniżej opisujemy każdą z nich.
Obróbka CNC
Jedną z najpopularniejszych metod produkcji form wtryskowych jest obróbka CNC (Computer Numerical Control), która pozwala na automatyczne sterowanie narzędziami skrawającymi za pomocą programu komputerowego. Metoda ta jest szczególnie przydatna w przypadku złożonych kształtów, które wymagają dużej precyzji.
Maszyny CNC są w stanie wykonać każdy detal z niesamowitą dokładnością, niezależnie od skomplikowania projektu. Ponadto świetnie nadają się do obróbki stali nierdzewnej oraz innych metali.
Obróbka skrawaniem pozwala na wytworzenie nawet bardzo skomplikowanych gniazd formujących, co czyni ją nieocenioną w produkcji form o wysokich wymaganiach dotyczących precyzyjności.
Obróbka elektroerozyjna (EDM)
Obróbka elektroerozyjna EDM to technika, w której materiał jest usuwany z przedmiotu obrabianego za pomocą serii wyładowań elektrycznych, które występują pomiędzy elektrodą narzędziową a obrabianym materiałem. Jedno i drugie oddziela tylko płyn dielektryczny. Skrót EDM oznacza Electrical Discharge Machining.
EDM umożliwia tworzenie bardzo złożonych i precyzyjnych form, które są trudne do wykonania za pomocą innych technik. Dlatego znajduje zastosowanie tam, gdzie wymagana jest skomplikowana geometria, a końcowa jakość powierzchni jest kluczowa.
Obróbka laserowa
Obróbka laserowa to zaawansowana technika, która pozwala na cięcie lub grawerowanie materiałów z wysoką precyzją. Laser jest przydatny w tworzeniu bardzo dokładnych i skomplikowanych detali na formach, zwłaszcza gdy wymagane są cienkie linie lub szczegółowe tekstury. Może być również używany do dokonywania poprawek lub modyfikacji już istniejących form.
Odlewanie próżniowe
Odlewanie próżniowe to technika, która może być stosowana do tworzenia prototypów lub form o ograniczonej trwałości, które służą do krótkotrwałych serii produkcyjnych. W tej technice oryginalny model jest umieszczany w komorze próżniowej, a silikon lub inne polimery są wylewane dookoła niego, tworząc tymczasową formę. Odlewanie próżniowe to nie jest typowa metoda, gdy w grę wchodzi produkcja trwałych form.
Gięcie i spawanie
Gięcie i spawanie mogą być używane do budowy korpusu formy gdy forma wymaga dużych, jednolitych płaszczyzn lub specyficznych konstrukcji metalowych. Często wykorzystuje się gięcie i spawanie przy tworzeniu dużych form lub tam, gdzie konieczna jest solidna konstrukcja wspierająca całą formę.
Obróbka chemiczna
Obróbkę chemiczną stosuje się przy tworzeniu mikrostruktur na powierzchni formy. Pozwala ona na precyzyjne usuwanie materiału za pomocą reakcji chemicznych, co jest szczególnie przydatne przy tworzeniu drobnych detali, które są trudne do wykonania za pomocą tradycyjnych metod mechanicznych.
Jaki jest średni czas produkcji formy wtryskowej?
Średni czas produkcji formy wtryskowej wynosi od kilku tygodni do około miesiąca w przypadku prostych projektów. Jednak dla form bardziej skomplikowanych może się wydłużyć nawet do dwóch lub trzech miesięcy. Z kolei szczególnie złożone projekty, które wymagają wysokiej precyzji lub innowacyjnych rozwiązań technologicznych, mogą potrzebować jeszcze więcej czasu na realizację.
Jak testowane są formy wtryskowe?
Najpopularniejsze sposoby testowania form wtryskowych to testowanie na sucho czy wykonanie pierwszego wtrysku. Poniżej opisujemy konkretne sposoby testowania form wtryskowych:
- Testowanie na sucho - Przeprowadza się je bez użycia materiału (tworzywa sztucznego) w celu sprawdzenia poprawności działania mechanizmów formy, takich jak systemy otwierania, zamykania, wtryskiwania, chłodzenia i ogrzewania. Ponadto sprawdza się, czy wszystkie ruchome części chodzą płynnie.
- Pierwszy test wtrysku - Polega na wykonaniu pierwszych wtrysków z użyciem właściwego materiału. Następnie analizuje się wyprodukowane części pod kątem jakości, dokładności wymiarowej i obecności defektów, takich jak puste przestrzenie, linie zgrzewu, nadmiar materiału czy naprężenia wewnętrzne.
- Testy wydajnościowe - Sprawdza się, jak formy radzą sobie podczas pracy pod obciążeniem i czy mogą produkować elementy w wymaganych cyklach czasowych bez utraty jakości. Na tym etapie testowania bada się również różne parametry procesu wtrysku, takie jak temperatura, ciśnienie i prędkość.
- Analiza wymiarowa - Każda część wyprodukowana podczas testów jest dokładnie mierzona i porównywana ze specyfikacjami projektowymi. Umożliwia to wychwycenie wszelkich odstępstw od planowanych wymiarów, które mogą wymagać dostosowania formy lub parametrów procesu.
- Testy materiałowe - Ocenia się, jak tworzywo sztuczne reaguje w formie, w tym jego zachowanie pod wpływem temperatury i ciśnienia. Analizuje się także właściwości wytrzymałościowe i elastyczne gotowego produktu.
- Testy długoterminowe - Przeprowadza się dłuższą serię produkcyjną, aby sprawdzić, czy forma utrzymuje swoją wydajność i jakość produkcji przez określony czas. Na tej podstawie analizuje się trwałość formy oraz jej elementów, jak również stabilność procesu produkcyjnego.
Jeśli testy i analizy wykażą konieczność naniesienia korekt, formy są modyfikowane. Dopiero po potwierdzeniu osiągnięcia wszystkich pożądanych parametrów produkcyjnych formy są uznawane za gotowe do rozpoczęcia masowej produkcji.
Czym jest tuszowanie form wtryskowych?
Tuszowanie form wtryskowych to technika używana do weryfikacji dokładności i jakości dopasowania poszczególnych części formy. Metoda ta polega na nakładaniu warstwy barwnego tuszu na jedną z powierzchni formy, a następnie zamykaniu jej, aby tusz mógł przenieść się na przeciwległe powierzchnie.
Po otwarciu formy analizuje się rozmieszczenie tuszu, co pozwala zidentyfikować miejsca, gdzie powierzchnie stykają się zbyt mocno lub zbyt słabo. Umożliwia to precyzyjne dostosowanie formy, co jest kluczowe dla zapewnienia jakości i trwałości produkowanych wyprasek.
Czym są prasy do tuszowania form wtryskowych?
Prasy do tuszowania form wtryskowych to specjalistyczne urządzenia służące do aplikacji tuszu na formy w procesie tuszowania. Maszyny te umożliwiają równomierne i kontrolowane nakładanie tuszu oraz precyzyjne zamykanie formy, co jest niezbędne dla dokładnego przeniesienia tuszu na stykające się powierzchnie.
Dzięki zastosowaniu pras do tuszowania można z dużą dokładnością ocenić jakość dopasowania formy, co jest istotne zarówno podczas jej początkowych testów, jak i regularnych kontroli w trakcie eksploatacji. Prasy zapewniają również powtarzalność procesu, tak istotną w produkcji przemysłowej.
Czym jest odpowietrzanie form wtryskowych?
Odpowietrzanie form wtryskowych to kluczowy proces technologiczny mający na celu usunięcie powietrza z wnętrza formy podczas wtryskiwania tworzywa sztucznego.
W trakcie wtrysku roztopione tworzywo sztuczne wprowadzane jest pod wysokim ciśnieniem do wnętrza formy, co może prowadzić do uwięzienia powietrza w jej przestrzeniach. Skutkuje to szeregiem problemów, takich jak tworzenie się pęcherzy lub nierówności czy nawet spalanie się materiału. Wpływają one negatywnie na jakość końcowego produktu.
Aby zapobiec powyższym komplikacjom, formy wyposaża się w specjalnie zaprojektowane kanały odpowietrzające, które umożliwiają ucieczkę powietrza na zewnątrz podczas wtrysku. Kanały zazwyczaj są umieszczane w strategicznych miejscach formy, takich jak najwyższe punkty przestrzeni formującej lub strefy wypełniane przez tworzywo sztuczne jako ostatnie.
Proces odpowietrzania jest niezbędny do utrzymania wysokiej jakości produkcji. Nie tylko eliminuje on wady związane z obecnością powietrza, ale także pomaga w utrzymaniu odpowiedniej prędkości wtrysku i ciśnienia w formie, co jest kluczowe dla osiągnięcia optymalnych właściwości fizycznych wyprasek.
Jakie są rodzaje form wtryskowych?
Główne rodzaje form wtryskowych to:
- Formy wtryskowe jednogniazdowe,
- Formy wtryskowe wielogniazdowe,
- Formy wtryskowe zimnokanałowe,
- Formy wtryskowe gorącokanałowe,
- Formy wtryskowe rozdmuchowe,
- Formy wtryskowe gabarytowe,
- Formy wtryskowe z jedną płaszczyzną podziału,
- Formy wtryskowe z wieloma płaszczyznami podziału,
- Formy wtryskowe próbne,
- Formy wtryskowe jednokomponentowe,
- Formy wtryskowe wielokomponentowe,
- Formy wtryskowe piętrowe,
- Formy wtryskowe suwakowe.
Poniżej opisujemy każdą z nich.
Formy wtryskowe jednogniazdowe
Formy wtryskowe jednogniazdowe są najprostszym typem form wtryskowych, gdzie w jednym cyklu produkcyjnym powstaje tylko jeden wyrób. Zazwyczaj są one stosowane do produkcji dużych elementów lub w przypadku, gdy wymagana jest bardzo wysoka dokładność każdego wyprodukowanego detalu.
Formy wtryskowe wielogniazdowe
W odróżnieniu od form wtryskowych jednogniazdowych, formy wtryskowe wielogniazdowe pozwalają na wytwarzanie kilku wyrobów jednocześnie w jednym cyklu pracy maszyny. Jest to rozwiązanie bardziej ekonomiczne przy masowej produkcji, gdyż zmniejsza czas i koszty związane z procesem wtrysku.
Formy wtryskowe zimnokanałowe
Formy wtryskowe zimnokanałowe wykorzystują układ kanałów, który po wtrysku zostaje wychłodzony razem z wypraską, co skutkuje powstawaniem tzw. “wlewek”. Dlatego kanały muszą być każdorazowo opróżniane z zastygłego materiału. Generuje to dodatkowe odpady, które wymagają recyklingu.
Formy wtryskowe gorącokanałowe
W formach wtryskowe gorącokanałowych układ kanałów jest utrzymywany w wysokiej temperaturze, co pozwala na ciągły przepływ tworzywa. W tym przypadku wlewki nie są częścią finalnego produktu, dzięki czemu maleje liczba odpadów i rośnie wydajność produkcji.
Czym różni się układ zimnokanałowy formy wtryskowej od gorącokanałowego?
Układ zimnokanałowy formy wtryskowej różni się od gorącokanałowego ceną, zarządzaniem odpadami i cyklem produkcji.
Układ zimnokanałowy jest bowiem tańszy, ale generuje więcej odpadów, ponieważ wlewki po kanałach wlewowych są usuwane i recyklingowane po każdym cyklu. Ponadto wymaga większej ilości energii do uplastycznienia tworzywa.
Z kolei w układzie gorącokanałowym tworzywo pozostaje w kanale w stanie płynnym, co redukuje odpady i skraca czas cyklu. Jednak system ten jest bardziej wrażliwy na zanieczyszczenia.
Formy wtryskowe rozdmuchowe
Formy wtryskowe rozdmuchowe są używane do produkcji wyrobów o zamkniętej, pustej wewnątrz budowie, takich jak butelki czy pojemniki. Aby to osiągnąć, wdmuchuje się powietrze do roztopionego tworzywa umieszczonego w formie, co pozwala na uzyskanie jednolitych ścianek produktu.
Formy wtryskowe gabarytowe
Gabarytowe formy wtryskowe są stosowane do produkcji dużych elementów, takich jak części karoserii samochodowej czy obudowy sprzętu AGD. Jednak ze względu na rozmiar formy te wymagają specjalnych maszyn wtryskowych o dużej sile zamykania.
Formy wtryskowe z jedną płaszczyzną podziału
Formy wtryskowe z jedną płaszczyzną podziału to najprostsza konstrukcja formy, która składa się z dwóch połówek rozdzielających się wzdłuż jednej płaszczyzny. Umożliwia to łatwe otwieranie formy i wyjmowanie wypraski.
Formy wtryskowe z wieloma płaszczyznami podziału
Złożone formy mogą mieć więcej niż jedną płaszczyznę podziału, co przydaje się przy produkcji skomplikowanych elementów z wieloma wypustkami lub wgłębieniami. Więcej płaszczyzn podziału umożliwia bowiem lepszą kontrolę nad procesem wtrysku i ułatwia produkcję złożonych detali.
Formy wtryskowe próbne
Formy wtryskowe próbne są wykorzystywane w fazie testowej produkcji, zanim zostaną uruchomione pełnowymiarowe linie produkcyjne. Służą one do sprawdzenia projektu wypraski, funkcjonalności formy, a także do doprecyzowania procesu produkcyjnego. Zazwyczaj są tańsze w wykonaniu i szybsze do wyprodukowania, niż pełnowymiarowe formy, co pozwala na ekspresową weryfikację i ewentualne modyfikacje projektu.
Formy wtryskowe jednokomponentowe
Formy wtryskowe jednokomponentowe są przeznaczone do produkcji części składających się z jednego rodzaju materiału. Są to najprostsze formy wtryskowe, stosowane w przypadkach, gdy produkt końcowy nie wymaga integracji różnych materiałów.
Formy wtryskowe wielokomponentowe
W odróżnieniu od form wtryskowych jednokomponentowych, formy wtryskowe wielokomponentowe (znane również jako formy wielomateriałowe) pozwalają na wtrysk dwóch lub więcej tworzyw w jednym cyklu produkcyjnym. Technika ta służy do produkcji złożonych wyrobów, które wymagają innych właściwości materiałowych w różnych częściach przedmiotu, takich jak np. miękkie uchwyty na twardych narzędziach.
Formy wtryskowe piętrowe
Formy wtryskowe piętrowe są specjalnym typem form, gdzie gniazda formujące są rozmieszczone w kilku poziomach, co maksymalizuje liczbę wyprodukowanych części przy minimalnym zużyciu przestrzeni maszyny. Są to formy wysoce wydajne, szczególnie przydatne w masowej produkcji małych elementów.
Formy wtryskowe suwakowe
Formy wtryskowe suwakowe zawierają ruchome elementy, znane jako suwaki. Umożliwiają one formowanie skomplikowanych kształtów z podcięciami, co byłyby niemożliwe do wykonania w tradycyjnych formach z jedną płaszczyzną podziału.
Suwaki przesuwają się w trakcie procesu wtrysku i otwierania formy, co pozwala na precyzyjne formowanie i łatwe wyjmowanie gotowego produktu.
Jakie jest zastosowanie form wtryskowych?
Zastosowanie form wtryskowych obejmuje wiele sektorów przemysłu jak motoryzacja, elektronika, opieka zdrowotna czy budownictwo. Poniżej opisaliśmy konkretne sposoby wykorzystania form wtryskowych w danych branżach:
- Motoryzacja - Produkcja wielu komponentów samochodów, np. paneli desek rozdzielczych, obudów świateł, elementów wnętrza oraz różnych innych detali wykończeniowych i funkcjonalnych. Dzięki formom wtryskowym możliwe jest osiągnięcie wymaganej precyzji i trwałości, które są kluczowe dla branży automotive.
- Elektronika - Tworzenie obudów dla telefonów komórkowych, komputerów, telewizorów oraz innych urządzeń elektronicznych. Formy wtryskowe pozwalają na masową produkcję skomplikowanych elementów, które muszą spełniać wysokie standardy jakościowe i estetyczne.
- Opieka zdrowotna - Produkcja wielu narzędzi medycznych jednorazowego i wielokrotnego użytku, takich jak strzykawki, elementy aparatury medycznej czy obudowy urządzeń diagnostycznych. Przedmioty te wymagają bardzo wysokiej precyzji wykonania oraz bezpieczeństwa użytkowania.
- Opakowania - Produkcja różnego rodzaju pojemników, butelek, wieczek i innych elementów opakowań, które są zarówno funkcjonalne, jak i estetycznie atrakcyjne. Formy wtryskowe umożliwiają projektowanie opakowań o złożonych kształtach i wielobarwnych wzorach.
- Budownictwo - Produkcja elementów takich jak rury, złączki, panele ścienne oraz inne komponenty konstrukcyjne. Wyroby te często wymagają odporności na warunki atmosferyczne i mechaniczne, co jest możliwe dzięki precyzji i trwałości procesu wtrysku.
- Artykuły gospodarstwa domowego - Produkcja szerokiej gamy produktów użytku domowego, w tym elementów meblowych, zabawek, narzędzi kuchennych i wielu innych. Dzięki elastyczności procesu wtrysku producenci mogą łatwo dostosowywać produkty do zmieniających się trendów i preferencji konsumentów.
Czy możliwa jest zmiana materiału detalu bez ingerencji w formę?
Tak, zmiana materiału detalu jest możliwa bez ingerencji w formę, pod warunkiem, że nowe tworzywo ma podobne właściwości przetwórcze do pierwotnie użytego. Należy jednak upewnić się, że temperatura topnienia i inne parametry nowego materiału są kompatybilne z parametrami pracy formy. Warto też sprawdzić, czy zmiana nie wpłynie negatywnie na jakość finalnego produktu, szczególnie w kontekście skurczu materiału, jego wytrzymałości czy wykończenia powierzchni.
Czy można wytworzyć różne detale na jednej formie?
Tak, można wytworzyć różne detale na jednej formie. Pozwalają na to formy wielogniazdowe, gdzie każde gniazdo może być zaprojektowane do produkcji innego detalu. Umożliwia to równoczesne wytwarzanie różnych części w jednym cyklu pracy wtryskarki. Ważne jest jednak, aby wszystkie detale były podobne pod względem rozmiaru i wymagań materiałowych, aby zapewnić równomierny przepływ tworzywa i uniknąć problemów z jakością wtrysku.
Jakie są zalety form wtryskowych?
Główne zalety form wtryskowych to:
- Wysoka wydajność - Formy wtryskowe pozwalają na szybką i masową produkcję części, co jest kluczowe w przemyśle, gdzie czas i koszty produkcji mają istotne znaczenie. Cykle produkcyjne są krótkie, co pozwala na szybką realizację dużych zamówień.
- Powtarzalność - Dzięki precyzji wykonania form każdy wyprodukowany element jest identyczny. Powtarzalność jest kluczowa dla utrzymania spójnej jakości przedmiotów w masowej produkcji.
- Zmniejszenie odpadów - Proces wtrysku umożliwia wykorzystanie większości materiału, minimalizując ilość odpadów produkcyjnych. Ponadto materiał, który nie został wykorzystany, często można ponownie przetworzyć.
- Możliwość tworzenia złożonych kształtów - Formy wtryskowe pozwalają na produkcję skomplikowanych i precyzyjnych geometrii, które byłyby trudne lub niemożliwe do wykonania innymi metodami obróbki.
- Wysoka jakość powierzchni - Wypraski uzyskane z form wtryskowych charakteryzują się doskonałą jakością wykończenia powierzchni, eliminując potrzebę dodatkowego obrabiania czy wykańczania.
- Elastyczność materiałowa - Formy wtryskowe pozwalają na używanie szerokiej gamy materiałów, od różnych rodzajów plastiku, przez metale, aż po nowoczesne kompozyty, co zwiększa ich uniwersalność.
- Automatyzacja procesu - Proces wtrysku można łatwo zautomatyzować, co redukuje koszty pracy i zwiększa efektywność produkcji. Automatyzacja przyczynia się również do zwiększenia bezpieczeństwa operacji.
- Trwałość form - Formy wtryskowe są projektowane z myślą o wielokrotnym użyciu, co sprawia, że mogą wytrzymać masową produkcję bez degradacji jakości.
Jakie są wady form wtryskowych?
Główne wady form wtryskowych są następujące:
- Wysokie koszty początkowe - Projektowanie i wykonanie form wtryskowych wiąże się z dużymi inwestycjami początkowymi, zwłaszcza w przypadku skomplikowanych kształtów. Wysokie koszty mogą okazać się nieprzekraczalną barierą dla mniejszych firm lub przy produkcji małoseryjnej.
- Złożoność projektowania - Zaprojektowanie skutecznej formy wtryskowej wymaga specjalistycznej wiedzy i doświadczenia, co stanowi wyzwanie dla inżynierów i projektantów. Ponadto ewentualne błędy w projekcie wymagają drogich poprawek i modyfikacji.
- Długi czas przygotowania - Opracowanie i wykonanie nowej formy może trwać wiele tygodni lub nawet miesięcy, co opóźnia ogólny termin rozpoczęcia produkcji. Długi czas przygotowania może być problematyczny na szybko zmieniających się rynkach.
- Ograniczenia materiałowe - Nie wszystkie materiały nadają się do procesu wtrysku, co ogranicza możliwości projektowe. Ponadto niektóre tworzywa sztuczne wymagają specjalnych dodatków lub modyfikacji samego procesu, aby zapewnić odpowiednią jakość wyprasek.
- Trudności z produkcją bardzo dużych elementów - Chociaż formy wtryskowe są idealne do produkcji małych i średnich części, wytwarzanie bardzo dużych wyrobów może być trudne i nieefektywne z powodu ograniczeń rozmiarów form i maszyn wtryskowych.
- Zużycie formy - Formy wtryskowe, zwłaszcza te wykonane z mniej trwałych materiałów, mogą ulegać stopniowemu zużyciu, co wpływa na jakość wyprasek. Zaś regularne konserwacje i wymiana form mogą generować dodatkowe koszty.
- Problemy z jakością wyprasek - Istnieje ryzyko wystąpienia wad produkcyjnych, takich jak naprężenia wewnętrzne, deformacje czy pęcherze powietrza, jeśli formy nie są odpowiednio zaprojektowane lub jeśli proces wtrysku nie jest optymalnie kontrolowany.
Jak działa chłodzenie form wtryskowych?
Chłodzenie form wtryskowych odbywa się za pomocą przepływu chłodziwa (zazwyczaj wody lub oleju) przez specjalnie zaprojektowane kanały chłodzące rozmieszczone wewnątrz formy. Kanały są umieszczane jak najbliżej przestrzeni formującej, aby maksymalnie skrócić czas potrzebny na odebranie ciepła z wypraski.
Etapy chłodzenia form wtryskowych są następujące:
- Rozprowadzanie chłodziwa - Chłodziwo trafia do formy wlotami, a następnie przepływa przez system kanałów obejmujących zarówno płytę stałą, jak i ruchomą formy. Przepływ musi być optymalnie zaprojektowany, aby zapewnić równomierne chłodzenie wszystkich części formy.
- Absorpcja ciepła - Gdy chłodziwo przepływa przez kanały, absorbuje ciepło z rozgrzanych ścian formy, które nagrzewają się od wtryskiwanego tworzywa. Skuteczność chłodzenia zależy od kilku czynników, w tym od rozstawu kanałów, ich średnicy oraz prędkości przepływu chłodziwa.
- Wydalanie ciepła - Ogrzane chłodziwo opuszcza formę, przekazując odebrane ciepło do zewnętrznego systemu chłodzenia. Następnie cykl rozpoczyna się na nowo.
Ile kosztują formy wtryskowe?
Formy wtryskowe kosztują od kilku tysięcy do nawet kilkuset tysięcy złotych. Finalna cena zależy wielu czynników, co sprawia, że precyzyjne oszacowanie wydatków wymaga analizy specyficznych potrzeb projektu.
Co wpływa na cenę form wtryskowych?
Na cenę form wtryskowych wpływa szereg czynników, takich jak:
- Złożoność konstrukcji - Bardziej skomplikowane formy, które wymagają precyzyjnego odwzorowania detali lub mają wiele ruchomych części (np. suwaki), są droższe w produkcji.
- Wymagania materiałowe - Wybór materiału na formę, np. wysokiej jakości stali narzędziowej, znacząco wpływa na koszt. Materiały odporne na zużycie i korozję są zwykle droższe, ale zapewniają dłuższą żywotność formy.
- Wielkość formy - Większe formy, które wymagają więcej materiału i czasu na wykonanie, są droższe.
- Liczba gniazd - Formy wielogniazdowe, pozwalające na jednoczesne wytwarzanie kilku części, są droższe w produkcji, ale mogą obniżać koszt jednostkowy każdej części.
- Typ formy - Niektóre typy form kosztują więcej, niż inne. Na przykład formy gorącokanałowe są droższe od zimnokanałowych ze względu na dodatkowe komponenty i zastosowaną technologię.
Dlaczego formy wtryskowe są drogie?
Formy wtryskowe są drogie ze względu na ich złożoność i wymagania technologiczne. Wysokie koszty form wtryskowych początkowe wynikają z potrzeby użycia precyzyjnych maszyn CNC lub elektroerozyjnych, a także specjalistycznej wiedzy inżynieryjnej do projektowania i wykonania form.
Koszt materiałów, szczególnie wysokiej jakości stali, również znacząco wpływa na finalną cenę. Tak samo jak czas i praca włożone w projektowanie, testowanie i dopracowanie formy.
Czy formy wtryskowe mogą być tańsze?
Formy wtryskowe mogą być tańsze, choć zazwyczaj wiąże się to z pewnymi kompromisami, takimi jak:
- Uproszczenie konstrukcji - Minimalizacja liczby ruchomych części i uproszczenie ich geometrii może obniżyć koszty produkcji formy.
- Standaryzacja - Używanie standardowych komponentów i modułów przełoży się na niższe wydatki projektowe i produkcyjne.
- Optymalizacja liczby gniazd - Dobór optymalnej liczby gniazd w zależności od przewidywanej wielkości produkcji może zrównoważyć cenę inwestycji.
- Recykling i modyfikacja istniejących form - W niektórych przypadkach możliwe jest modyfikowanie lub adaptowanie używanych form do nowych projektów, co pozwala zaoszczędzić na kosztach materiałów i obróbki.
Jakie narzędzia są wykorzystywane do form wtryskowych?
Do form wtryskowych wykorzystywane są różne specjalistyczne narzędzia niezbędne zarówno podczas produkcji, jak i podczas konserwacji oraz obsługi w trakcie procesu wtryskiwania.
Oto niektóre z głównych narzędzi używanych w tej dziedzinie:
- Wtryskarki - Maszyny do wtrysku są kluczowe w procesie produkcji, bowiem to one wtryskują roztopione tworzywo sztuczne pod ciśnieniem do formy.
- Narzędzia pomiarowe - Precyzyjne narzędzia, takie jak mikrometry, suwmiarki czy współrzędnościowe maszyny pomiarowe (CMM) są niezbędne do dokładnego mierzenia wymiarów formy i wyprasek, co jest kluczowe dla zapewnienia jakości i dokładności produkcji.
- Narzędzia ręczne - Różnego rodzaju klucze, śrubokręty, szczypce i inne narzędzia ręczne są używane do montażu, demontażu i regulacji form.
- Systemy chłodzenia - Pompy, węże i inne elementy systemów chłodzenia są konieczne do regulowania temperatury formy podczas procesu wtrysku, co jest kluczowe dla zachowania jakości wyprasek.
- Narzędzia do polerowania i szlifowania - Służą do wykańczania i poprawiania powierzchni form, co ma bezpośredni wpływ na jakość końcowego produktu.
Jakie akcesoria są wykorzystywane do form wtryskowych?
Do form wtryskowych wykorzystywane są różne akcesoria. Poniżej przedstawiamy kilka najpopularniejszych:
- Wkładki i nasadki formujące - Elementy, które można dostosować lub wymienić w celu modyfikacji kształtu, rozmiaru lub wzoru gotowego produktu. Pozwalają na szybkie przestawianie produkcji na różne warianty wyrobu.
- Kołki wyrzutników i tuleje - Używane do automatycznego wyrzucania gotowego produktu z formy po zakończeniu cyklu wtryskowego. Ich właściwe działanie jest niezbędne do zapewnienia płynności procesu produkcyjnego.
- Czujniki temperatury i ciśnienia - Umieszczane w strategicznych punktach formy do monitorowania i regulacji warunków procesowych. Dostarczają cennych danych, które mogą być używane do automatycznej korekty parametrów wtrysku.
- Systemy zabezpieczeń i blokad - Zapobiegają przypadkowemu otwarciu formy podczas wtrysku, co jest kluczowe dla bezpieczeństwa operacji.
- Systemy chłodzenia/wentylacji - Rury, szybkozłącza lub węże, które prowadzą ciecz chłodzącą lub powietrze do różnych części formy w celu zapewnienia równomiernego chłodzenia produktu i uniknięcia deformacji. Poniżej przyglądamy się im bardziej szczegółowo.
Węże do form wtryskowych
Węże do form wtryskowych są kluczowym elementem systemów chłodzenia i grzewczych używanych w procesie wtryskowym. Ich głównym zadaniem jest transport chłodziwa (najczęściej wody lub oleju) do i z formy.
Węże do gorącej wody muszą być odporne na temperatury oraz ciśnienie, aby skutecznie przekazywać medium chłodzące do wszystkich części formy, nawet tych trudno dostępnych. Dlatego dobór odpowiedniej jakości węży do układu chłodzenia jest ważny dla efektywności chłodzenia i jakości finalnych wyrobów. Minimalizuje bowiem ryzyko deformacji czy wewnętrznych naprężeń materiału.
Szybkozłącza do form wtryskowych
Szybkozłącza są stosowane do szybkiego i efektywnego łączenia linii chłodniczych lub grzewczych z formą wtryskową. Dzięki nim można łatwo i bezpiecznie podłączyć lub odłączyć formę od systemu chłodzenia bez konieczności użycia narzędzi, co znacząco skraca czas przestojów i zmian konfiguracji.
Szybkozłącza do form wtryskowych zapewniają także lepsze uszczelnienie połączenia, co jest kluczowe dla utrzymania odpowiedniego ciśnienia i przepływu chłodziwa.
Dostępne są różne typy szybkozłączy, w tym te przeznaczone do wysokich temperatur i ciśnień, co czyni je uniwersalnym rozwiązaniem dla różnorodnych aplikacji w procesie wtrysku.
Jak wybrać formę wtryskową?
Aby wybrać odpowiednią formę wtryskową, należy zwrócić uwagę na kilka istotnych kryteriów, takich jak:
- Złożoność konstrukcji - Im bardziej złożona konstrukcja, tym większe wymagania co do precyzji wykonania formy. Skomplikowane formy mogą wymagać zaawansowanych technologii obróbki, takich jak elektroerozja czy obróbka laserowa, co wpływa na koszty i czas produkcji.
- Rozmiar formy - Większe formy wymagają maszyn o większej mocy, a ponadto mogą generować wyższe koszty materiałowe i energetyczne.
- Ilość kawitacji - Liczba kawitacji, czyli liczba gniazd w formie, wpływa na szybkość produkcji oraz jednorodność jakości wytwarzanych elementów. Większa liczba kawitacji umożliwia szybszą produkcję, ale wymaga również bardziej skomplikowanej i droższej formy.
- Typ zastosowanego tworzywa - Tworzywa sztuczne mają różne właściwości fizykochemiczne, które wpływają na wymagania stawiane formom. Na przykład tworzywa o wyższej temperaturze topnienia wymagają form o większej odporności na wysokie temperatury. Z kolei tworzywa o większym skurczu wymagają większej precyzji wykonania form, aby kompensować zmiany wymiarów podczas stygnięcia.
- Koszt - Ostateczny wybór tworzywa i typu formy często balansuje między oczekiwaną jakością a kosztami związanymi z przetwarzaniem. Wyższe koszty początkowe mogą przełożyć się na niższe koszty jednostkowe w produkcji masowej, dlatego ważne jest przemyślane planowanie i analiza zwrotu z inwestycji.
Jakie wyróżnia się wykończenia powierzchni formy wtryskowej?
Najpopularniejsze wykończenia powierzchni formy wtryskowej to:
- poler techniczny,
- poler lustro,
- elektrodrążenie,
- piaskowanie,
- szkiełkowanie,
- trawienie chemiczne.
Poniżej opisujemy każde z nich.
Poler techniczny
Poler techniczny jest jednym z podstawowych sposobów wykończenia powierzchni formy, który polega na jej manualnym szlifowaniu za pomocą papierów ściernych o coraz mniejszej gradacji. Pozwala to na osiągnięcie gładkiej powierzchni bez wysokiego poziomu odblasku, co jest odpowiednie dla większości zastosowań przemysłowych, gdzie wymagana jest dobra jakość powierzchni bez konieczności osiągania efektu lustrzanego.
Poler lustro
Poler lustro to technika wykończeniowa, która polega na osiągnięciu bardzo wysokiego poziomu gładkości i połysku, imitującego powierzchnię lustra. Jest to proces czasochłonny i kosztowny, wymagający zastosowania specjalnych past polerskich oraz wieloetapowego szlifowania. Wykończenie to jest często stosowane w formach dla części, które wymagają estetycznie doskonałej powierzchni, takich jak elementy optyczne czy dekoracyjne.
Elektrodrążenie
Elektrodrążenie to technika używana do tworzenia tekstur lub mikrostruktur na powierzchni formy poprzez kontrolowaną erozję materiału z użyciem impulsów elektrycznych. Pozwalają one na precyzyjne modelowanie skomplikowanych wzorów, które są trudne do osiągnięcia innymi metodami. Jest to technika często wykorzystywana do tworzenia tekstur skóry, drewna czy geometrycznych wzorów na produktach.
Piaskowanie
Piaskowanie to proces, w którym drobne cząstki ścierniwa (najczęściej piasek) są wyrzucane pod wysokim ciśnieniem na powierzchnię formy, co skutkuje matowym i równomiernym wykończeniem. Technika ta jest stosowana, aby zredukować odblaski na powierzchni wypraski oraz zwiększyć jej adhezję wobec farb i powłok.
Szkiełkowanie
Szkiełkowanie to metoda podobna do piaskowania, w której zamiast piasku stosuje się drobne szklane kuleczki. Metoda ta pozwala na osiągnięcie bardziej jednolitej i subtelnej tekstury, niż w przypadku tradycyjnego piaskowania. Jest stosowana w celu uzyskania delikatniejszego, matowego wykończenia.
Trawienie chemiczne
Trawienie chemiczne polega na aplikacji substancji chemicznych na powierzchnię formy, które selektywnie usuwają materiał, tworząc żądane tekstury lub wzory. Technika ta jest szczególnie przydatna do wykonywania precyzyjnych i powtarzalnych wzorów na dużych powierzchniach form.
Jak zadbać o prawidłowe działanie form wtryskowych?
Aby zadbać o prawidłowe działanie form wtryskowych, konieczna jest regularna konserwacja i przestrzeganie odpowiednich procedur operacyjnych. Oto kilka ważnych zasad, które pomogą w utrzymaniu form wtryskowych w dobrym stanie:
- Regularne czyszczenie - Formy powinny być regularnie czyszczone z resztek tworzywa, pyłów i innych zanieczyszczeń. Czysta forma zapewnia lepszą jakość wyprasek i rzadziej ulega uszkodzeniom mechanicznym.
- Konserwacja powierzchni formy - Wszystkie powierzchnie robocze formy powinny być regularnie sprawdzane pod kątem uszkodzeń, takich jak zadrapania czy wżery. Należy je odpowiednio polerować i naprawiać, aby uniknąć wpływu na jakość produktów końcowych.
- Smarowanie mechanizmów ruchomych - Mechanizmy ruchome, takie jak suwaki czy wypychacze, wymagają regularnego smarowania, aby zapewnić ich płynne działanie. Zapobiegnie to ich przedwczesnemu zużyciu.
- Kontrola systemów chłodzenia - Należy regularnie sprawdzać, czy kanały chłodzące są wolne od zatorów i czy system chłodzenia działa efektywnie. Nieprawidłowa temperatura formy może bowiem prowadzić do problemów z jakością wtrysku i dłuższego cyklu produkcyjnego.
- Inspekcja i kalibracja sprzętu - Regularne kontrole i kalibracje sprzętu, w tym pomiarów ciśnienia, temperatury oraz parametrów cyklu wtrysku, są niezbędne dla zapewnienia stabilnych i powtarzalnych wyników produkcyjnych.
- Dokumentacja i analiza awarii - Prowadzenie dokładnej dokumentacji dotyczącej historii konserwacji i napraw form jest kluczowe dla efektywnego zarządzania stanem technicznym. Analiza przyczyn awarii i wprowadzanie korekt na podstawie zebranych danych pozwala na unikanie powtarzających się problemów.
- Szkolenie personelu - Regularne szkolenia dla operatorów i techników utrzymania ruchu, mające na celu podnoszenie ich kwalifikacji w zakresie obsługi i konserwacji form wtryskowych, są istotne dla zachowania wysokiej jakości produkcji.
Zastosowanie tych zasad zapewnia nie tylko długotrwałe i bezawaryjne funkcjonowanie form wtryskowych, ale również przyczynia się do obniżenia kosztów produkcji poprzez minimalizację przestojów i zwiększenie wydajności procesów produkcyjnych.
Jaka jest gwarancja na formy wtryskowe?
Gwarancja na formy wtryskowe różni się w zależności od producenta, rodzaju formy oraz warunków umowy.
Zazwyczaj producenci form wtryskowych oferują gwarancję obejmującą wady materiałowe i błędy wykonania z okresem gwarancyjnym wynoszącym od roku do trzech lat. Jest on dostosowany do przewidywanej liczby cykli pracy formy lub ilości wyprodukowanych za jej pomocą części.
Poza tym u niektórych producentów gwarancja obejmuje określoną liczbę cykli wtrysku, co jest szczególnie istotne w przypadku intensywnego użytkowania. Na przykład forma może mieć gwarancję na milion cykli wtrysku, dzięki czemu masz pewność, że będzie ona funkcjonować bez awarii do osiągnięcia tego limitu.
Ważne jest, aby przed zakupem formy dokładnie sprawdzić warunki gwarancji i upewnić się, że obejmuje ona wszystkie istotne aspekty mające wpływ na działanie i trwałość formy. Należy także zwrócić uwagę na procedury reklamacyjne i warunki serwisowania, które mogą być wymagane w przypadku wystąpienia wad gwarancyjnych.
W niektórych przypadkach, dla dodatkowego zabezpieczenia, klienci mogą negocjować o rozszerzenie gwarancji lub dodatkowe usługi konserwacyjne, które pomogą w utrzymaniu formy w optymalnym stanie przez dłuższy czas. Rozszerzenia tego typu są szczególnie wartościowe w przypadku skomplikowanych projektów.
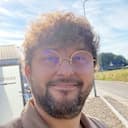
Autor artykułu
Bartosz Kułakowski
CEO Hosetech Sp.z o.o.
Bartosz Kułakowski jest specjalistą od węży i złączy przemysłowych z ponad 10 letnim doświadczeniem. Bartosz jest obecny w branży technicznej od 2013 roku. Zdobywał doświadczenie jako doradca techniczno-handlowy w sektorze tworzywowych taśm przenośnikowych, konstrukcji stalowych, węży i złączy przemysłowych. Od 2016 roku specjalizuje się wyłącznie w wężach i złączach. Twórca firmy HOSETECH Bartosz Kułakowski, obecnie HOSETECH Sp. z o.o.
Spis treści
Czym są formy wtryskowe?
Z jakich elementów zbudowana jest forma wtryskowa?
Jak projektowane są formy wtryskowe?
Wykonanie projektu wyrobu końcowego
Stworzenie projektu formy
Przygotowanie formy
Próby i dopracowania
Próby końcowe
Jak produkowane są formy wtryskowe?
Podział na elementy formujące
Konstrukcja elementów formujących
Zabudowa korpusu formy
Projektowanie układu doprowadzenia tworzywa
Projektowanie układu chłodzenia
Projektowanie układu wypychania
Stworzenie symulacji wtrysku
Konstrukcja elementów funkcjonalnych formy
Konstrukcja dodatkowych elementów
Stworzenie listy materiałowej BOM
Wykonanie rysunku zestawieniowego oraz rysunków wykonawczych
Montaż formy we wtryskarce
Czym są normalia w formach wtryskowych?
Jakie materiały są wykorzystywane do tworzenia form wtryskowych?
Jaka stal na formy wtryskowe?
Jakie maszyny są potrzebne do wykonania formy wtryskowej?
Jakie są metody produkcji form wtryskowych?
Obróbka CNC
Obróbka elektroerozyjna (EDM)
Obróbka laserowa
Odlewanie próżniowe
Gięcie i spawanie
Obróbka chemiczna
Jaki jest średni czas produkcji formy wtryskowej?
Jak testowane są formy wtryskowe?
Czym jest tuszowanie form wtryskowych?
Czym są prasy do tuszowania form wtryskowych?
Czym jest odpowietrzanie form wtryskowych?
Jakie są rodzaje form wtryskowych?
Formy wtryskowe jednogniazdowe
Formy wtryskowe wielogniazdowe
Formy wtryskowe zimnokanałowe
Formy wtryskowe gorącokanałowe
Formy wtryskowe rozdmuchowe
Formy wtryskowe gabarytowe
Formy wtryskowe z jedną płaszczyzną podziału
Formy wtryskowe z wieloma płaszczyznami podziału
Formy wtryskowe próbne
Formy wtryskowe jednokomponentowe
Formy wtryskowe wielokomponentowe
Formy wtryskowe piętrowe
Formy wtryskowe suwakowe
Jakie jest zastosowanie form wtryskowych?
Czy możliwa jest zmiana materiału detalu bez ingerencji w formę?
Czy można wytworzyć różne detale na jednej formie?
Jakie są zalety form wtryskowych?
Jakie są wady form wtryskowych?
Jak działa chłodzenie form wtryskowych?
Ile kosztują formy wtryskowe?
Co wpływa na cenę form wtryskowych?
Dlaczego formy wtryskowe są drogie?
Czy formy wtryskowe mogą być tańsze?
Jakie narzędzia są wykorzystywane do form wtryskowych?
Jakie akcesoria są wykorzystywane do form wtryskowych?
Węże do form wtryskowych
Szybkozłącza do form wtryskowych
Jak wybrać formę wtryskową?
Jakie wyróżnia się wykończenia powierzchni formy wtryskowej?
Poler techniczny
Poler lustro
Elektrodrążenie
Piaskowanie
Szkiełkowanie
Trawienie chemiczne
Jak zadbać o prawidłowe działanie form wtryskowych?
Jaka jest gwarancja na formy wtryskowe?
Te produkty mogą Cię zainteresować