Chłodzenie form wtryskowych – Jak ochłodzić formy wtryskowe?
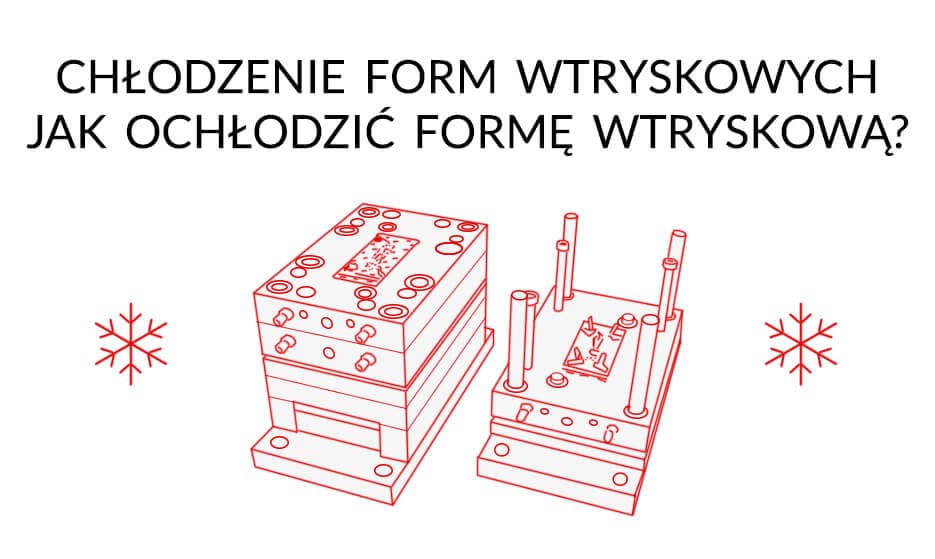
Czym jest chłodzenie form wtryskowych?
Chłodzenie form wtryskowych to kluczowy element procesu wtrysku tworzyw sztucznych, mający na celu regulację temperatury formy podczas i po wtryskiwaniu stopionego materiału. Optymalna temperatura jest niezbędna do uzyskania wysokiej jakości wyrobów, ponieważ wpływa na szybkość krzepnięcia i ostateczne właściwości fizyczne produktu.
Proces chłodzenia rozpoczyna się natychmiast po wtrysku rozgrzanego polimeru do wnęki formy. Aby przyspieszyć jego utwardzanie i umożliwić szybkie wyjęcie, formy są wyposażone w systemy chłodzące, najczęściej składające się z serii kanałów, przez które przepływa chłodziwo (np. woda lub olej).
Kanały mogą być rozmieszczone na wiele sposobów. Zależy to od kształtu i rozmiaru formy, a także od wymagań termicznych.
Dlaczego chłodzenie form wtryskowych jest ważne?
Chłodzenie form wtryskowych jest ważne, ponieważ bezpośrednio wpływa na jakość, wydajność i ekonomiczność procesu wtryskiwania. Wynika to z kilku powodów.
Po pierwsze, odpowiednia temperatura formy zapewnia szybsze twardnienie materiału, co skraca cykl produkcyjny. Krótszy cykl pozwala natomiast na zwiększenie wydajności i obniżenie kosztów operacyjnych wtryskiwania. Jest to kluczowe w warunkach przemysłowych, gdzie każda sekunda przestoju generuje dodatkowe koszty.
Po drugie, równomierne chłodzenie materiału wpływa na jakość końcowego produktu. Nierówne odprowadzanie ciepła może prowadzić do wewnętrznych naprężeń, deformacji, a nawet pęknięć, co z kolei zwiększa ilość odrzutów i obniża standardy jakościowe. Natomiast dobre chłodzenie skutkuje jednolitymi właściwościami fizycznymi produktu, takimi jak wytrzymałość, elastyczność oraz estetyka.
Po trzecie, skuteczne chłodzenie ma wpływ na trwałość samej formy. Redukuje bowiem ryzyko jej uszkodzenia z powodu nadmiernego nagrzewania się, które może skutkować koniecznością wymiany lub przeprowadzenia drogich napraw. Optymalna temperatura pracy zwiększa żywotność formy i zapewnia lepsze wyniki produkcyjne.
Po czwarte, zaawansowane systemy chłodzenia zapewniają większą elastyczność w projektowaniu produktów. Inżynierowie mogą eksperymentować z bardziej złożonymi kształtami i cieńszymi ściankami, co otwiera drogę do innowacji i rozwoju nowych, lepszych wyrobów.
Ponadto procesy wspierane przez precyzyjne sterowanie temperaturą są bardziej zrównoważone i ekologiczne, co ma coraz większe znaczenie w odpowiedzialnym przemyśle produkcyjnym.
Czym jest bilans cieplny formy wtryskowej?
Bilans cieplny formy wtryskowej odnosi się do zarządzania ilością ciepła wprowadzanego i usuwanego z formy podczas cyklu produkcyjnego. Aby osiągnąć wysoką jakość i wydajność, niezbędne jest precyzyjne zrównoważenie obu procesów.
Ciepło jest wprowadzane do formy poprzez stopiony polimer, który podczas wtrysku wypełnia jej gniazdo. Jednak ciepło to musi być jednocześnie efektywnie (i w odpowiednim tempie) usuwane, aby umożliwić szybkie i równomierne stygnięcie oraz krzepnięcie tworzywa.
W tym celu projektuje się system chłodzenia formy.
Równoważenie bilansu cieplnego wymaga uwzględnienia wielu czynników, w tym właściwości termicznych użytego tworzywa, geometrii formy, prędkości wtrysku i temperatury chłodziwa.
Od skuteczności na tym polu zależy wydajność całego cyklu produkcyjnego. Zbyt wolne odprowadzanie ciepła wydłuża cykl i zwiększa koszty produkcji, podczas gdy zbyt szybkie może prowadzić do wad materiałowych, takich jak naprężenia wewnętrzne czy skurcz.
Jaka powinna być temperatura formy wtryskowej?
Temperatura formy wtryskowej powinna być dostosowana do rodzaju i właściwości termicznych używanego tworzywa sztucznego, a także do specyfikacji produktu końcowego.
Dla tworzyw termoplastycznych, takich jak polipropylen (PP) czy polietylen (PE), temperatura formy zazwyczaj waha się w zakresie od 30°C do 90°C. Z kolei tworzywa inżynieryjne, takie jak nylon czy poliwęglany, wymagają wyższych temperatur formy, często sięgających od 80°C do 140°C, co jest niezbędne do uniknięcia wad materiałowych, takich jak nierównomierne kurczenie czy naprężenia wewnętrzne.
Ustalenie odpowiedniej temperatury formy to proces, który wymaga uwzględnienia wielu czynników, takich jak:
- Charakterystyka tworzywa - Różne materiały mają inne temperatury przetwarzania i krzepnięcia.
- Geometria produktu - Złożoność kształtu i grubość ścianek produktu także wpływają na wymagania cieplne.
- Cykl produkcyjny - Krótszy cykl wymaga szybszego chłodzenia, ale należy wziąć pod uwagę, że zbyt niska temperatura może prowadzić do wad produkcyjnych.
- Jakość wykończenia powierzchni - W celu uzyskania gładkiej powierzchni bez śladów łączeń czy zarysowań mogą być potrzebne wyższe temperatury.
Inżynierowie stosują symulacje komputerowe i empiryczne testy do optymalizacji temperatury form, aby maksymalizować jakość i wydajność, jednocześnie minimalizując ryzyko defektów i maksymalizując trwałość formy.
Jednak zarządzanie temperaturą to nie tylko kwestia ustawień technicznych, ale też kosztów i efektywności produkcji, co ma bezpośredni wpływ na konkurencyjność wyrobów na rynku.
Jak działa układ chłodzenia formy wtryskowej?
Układ chłodzenia formy wtryskowej działa na bazie precyzyjnie zaprojektowanego systemu kanałów chłodzących, przez które przepływa chłodziwo (najczęściej woda lub specjalny płyn chłodzący).
Zasada działania układu chłodzenia jest stosunkowo prosta, lecz kluczowa dla całego procesu produkcyjnego:
- Wprowadzenie ciepła - Podczas wtrysku gorące tworzywo wprowadza do formy dużą ilość ciepła, które musi być skutecznie usunięte, aby materiał mógł stwardnieć.
- Przepływ medium chłodzącego - Medium chłodzące przepływa przez kanały wykonane w formie, które są strategicznie rozmieszczone, aby zapewnić równomierne chłodzenie całej powierzchni formy. Jest to kluczowe dla zapobiegania deformacjom i innym wadom wyrobu. Zaleca się, aby średnice kanałów nie były mniejsze niż 6 mm, ponieważ przy mniejszych wartościach następuje tłumienie przepływu medium chłodzącego, co utrudnia chłodzenie formy. Z kolei górna granica średnicy kanału wynosi ok. 20 mm. Powyżej tej wartości intensywność chłodzenia nie wzrasta, a zwiększa się tylko wydatek chłodziwa, co jest zjawiskiem niepożądanym.
- Odbiór ciepła - Medium chłodzące absorbuje ciepło z formy, a następnie odprowadza je na zewnątrz układu. Efektywność tego procesu zależy od wielu czynników, w tym od rodzaju i temperatury medium chłodzącego oraz od konstrukcji i materiału formy.
- Regulacja temperatury - Nowoczesne układy chłodzenia są wyposażone w zaawansowane regulatory temperatury, które pozwalają na dynamiczne dostosowywanie parametrów chłodzenia w odpowiedzi na zmieniające się warunki.
Przy projektowaniu układu chłodzenia należy mieć również na uwadze długość drogi przepływu medium chłodzącego przez formę wtryskową. Całkowita długość kanałów powinna być możliwie jak najkrótsza, aby zapewnić minimalną różnicę temperatury chłodziwa na wejściu i wyjściu, nie większą niż 2-3°C. Wynika to z faktu, że niewielka różnica równomierne odbiera ciepło z wypraski we wszystkich strefach gniazda formującego.
Jakie elementy wtryskarki wymagają chłodzenia?
Elementami wtryskarki, które wymagają chłodzenia są forma wtryskowa oraz system hydrauliczny.:
- Forma wtryskowa - Jest to najbardziej oczywisty i kluczowy element wymagający chłodzenia. Systemy chłodzące w formie wtryskowej są zaprojektowane do szybkiego odprowadzania ciepła, które jest do niej wprowadzane przez stopione tworzywo. Zapewnia to odpowiedni czas stygnięcia i krzepnięcia materiału, co jest niezbędne do uzyskania pożądanej jakości i wymiarów produktu.
- System hydrauliczny - Wiele wtryskarek wykorzystuje hydraulikę do napędzania ruchów maszyny, w tym zamknięcia formy czy wtrysku. Olej hydrauliczny używany w tych systemach generuje ciepło podczas pracy, które musi być kontrolowane przez dedykowane chłodnice oleju, aby zapobiec przegrzewaniu się i awariom.
Jakie są techniki chłodzenia form wtryskowych?
Główne techniki chłodzenia form wtryskowych to:
- konwencjonalny układ chłodzący,
- chłodzenie konformalne,
- chłodzenie konturowe,
- technologia BFMOLD.
Poniżej opisujemy każdą z nich.
Konwencjonalny układ chłodzący form wtryskowych
Konwencjonalny układ chłodzenia form wtryskowych to standardowe rozwiązanie, które jest wykorzystywane ze względu na prostotę wykonania oraz stosunkowo niskie koszty. Głównym elementem tego typu systemów są otwory wiercone w elementach formy, przez które przepływa medium chłodzące.
Otwory te są rozmieszczone w jednym kierunku, a ich połączenie odbywa się za pomocą otworów poprzecznych lub przez zastosowanie elastycznych węży na zewnątrz formy, co umożliwia skuteczne przesyłanie cieczy chłodzącej.
Ze względu na konieczność kontroli przepływu medium w każdej strefie chłodzenia, część kanałów chłodzących jest zamykana specjalnymi korkami, zazwyczaj wykonanymi z miedzi lub jej stopów. Pozwalają one na izolowanie poszczególnych sekcji układu chłodzenia.
Jedną z głównych wad tego rozwiązania jest ryzyko przecieków, które mogą zakłócać efektywność chłodzenia.
Poza tym utrzymanie odpowiedniej temperatury staje się wyzwaniem w przypadku form z ruchomymi rdzeniami czy długimi częściami stemplowymi, gdzie trudno jest zapewnić skuteczny przepływ medium chłodzącego. Dlatego w takich sytuacjach stosuje się specjalne konstrukcje chłodzenia stempli (np. przegrody proste lub spiralne), które kierują przepływ chłodziwa, minimalizując różnicę temperatury między stroną wlotu i wylotu.
W elementach długich, takich jak stemple, używane są także dysze chłodzące, które mogą być rozmieszczone szeregowo lub równolegle. Oferują one szereg korzyści, w tym łatwość instalacji, możliwość pracy w dowolnej orientacji oraz niski spadek ciśnienia, co jest szczególnie ważne przy projektowaniu efektywnych systemów chłodzenia.
Chłodzenie konformalne form wtryskowych
Chłodzenie konformalne to nowoczesna technologia, która wykorzystuje zaawansowane metody przyrostowe, takie jak laserowe przetapianie proszków metali (Direct Metal Laser Sintering - DMLS, lub Selective Laser Melting - SLM). Dzięki temu możliwe jest tworzenie kanałów chłodzących, które idealnie dopasowują się do kształtu i złożoności wyprasek.
W chłodzeniu konformalnym kanały chłodzące prowadzone są blisko powierzchni formujących, dzięki czemu bardzo efektywnie odbierają ciepło z wypraski.
Kanały mogą mieć dowolne, często skomplikowane przekroje poprzeczne, czego nie da się osiągnąć przy zastosowaniu tradycyjnych metod wiercenia. Takie rozwiązanie pozwala na utrzymanie równej odległości między kanałem a powierzchnią formującą, co przekłada się na równomierne rozłożenie temperatury na całej powierzchni formy.
Oznacza to eliminację problemu nierównego chłodzenia, który jest typowy dla tradycyjnych układów, gdzie odległość kanałów chłodzących od powierzchni formującej bywa zmienna.
Dzięki zastosowaniu chłodzenia konformalnego, możliwe jest osiągnięcie wyższej precyzji kontroli temperatury, co jest szczególnie ważne w produkcji skomplikowanych komponentów wymagających szczególnej dbałości o detale i redukcji ryzyka deformacji.
Technologia chłodzenia konformalnego umożliwia nie tylko skrócenie cyklu wtrysku, ale także intensyfikację chłodzenia dzięki selektywnemu odbiorowi ciepła z poszczególnych obszarów wypraski. Pozwala to na tworzenie gradientu struktury w materiałach, otwierając nowe możliwości w projektowaniu właściwości fizycznych produktów.
Chłodzenie konformalne jest także wykorzystywane do chłodzenia specyficznych elementów, takich jak stemple, trzpienie czy rdzenie za pomocą jednego lub kilku specjalnie zaprojektowanych kanałów, co zwiększa efektywność i precyzję procesu produkcyjnego.
Chłodzenie konturowe form wtryskowych
Chłodzenie konturowe form wtryskowych polega na wykonaniu frezowanych kanałów chłodzących bezpośrednio w rdzeniu stempla. Później na taki rdzeń nakładana jest oprawka, która zapewnia odpowiednie uszczelnienie i utrzymuje medium chłodzące w określonej trajektorii.
Kanały chłodzące są prowadzone blisko powierzchni formującej, więc lepiej odwzorowują kształt wypraski i wydajniej odbierają ciepło z przetwarzanego tworzywa. Skutkuje to bardziej intensywnym i równomiernym rozkładem temperatury, co jest kluczowe dla osiągnięcia wysokiej jakości finalnego produktu.
Główną zaletą tego rodzaju chłodzenia jest intensywny odbiór ciepła, co przekłada się na szybsze stygnięcie materiału i krótsze cykle produkcyjne. Duża objętość przepływu medium chłodzącego i związane z nią efektywne odprowadzanie wysokiej temperatury jest szczególnie ważne przy produkcji gabarytowych lub złożonych elementów.
Wadą chłodzenia konturowego jest natomiast konieczność zapewnienia szczelności połączenia między rdzeniem stempla a oprawką. Brak hermetyczności może prowadzić do przecieków medium chłodzącego, co obniża efektywność chłodzenia i jakość wypraski.
Metoda ta ma również ograniczone zastosowanie przy chłodzeniu płyt stemplowych o małej grubości, ponieważ frezowanie kanałów może osłabić ich strukturę i wytrzymałość.
Technologia BFMOLD
Technologia BFMOLD® to innowacyjna technologia, która charakteryzuje się zastosowaniem dwóch niezależnych obiegów cieczy, które służą do dynamicznego zarządzania temperaturą
Główny obieg odpowiada za podstawową regulację temperatury formy. Z kolei obieg drugi, zlokalizowany w okolicach gniazda formującego, służy do szybkiego podnoszenia temperatury w momencie potrzeby.
Kluczowym elementem tej technologii jest kieszeń wewnątrz wkładu formującego, którą wypełniają kulki. Zapewniają one nie tylko odpowiednią sztywność konstrukcji, ale również sprzyjają równomiernemu rozkładowi temperatury na powierzchni formującej.
W momencie aktywacji, obieg wody przepływa przez wnękę z kulkami, co umożliwia efektywną i szybką zmianę temperatury powierzchni formującej. Pozwala to na dynamiczną adaptację do dynamicznych warunków procesu wtrysku, co jest kluczowe dla zachowania optymalnych parametrów produkcji. Technologia BFMOLD® została opatentowana przez brytyjski koncern Wittmann Group, która znacząco usprawnia proces regulacji temperatury w formach wtryskowych.
Korzyści z zastosowania technologii BFMOLD® są następujące:
- Zwiększenie wydajności produkcji - Skrócenie czasu cyklu jest możliwe dzięki szybszej regulacji temperatury, co bezpośrednio przekłada się na większą ilość wyprodukowanych przedmiotów w jednostce czasu.
- Dynamiczna regulacja temperatury - Zwiększenie powierzchni czynnej wymiany cieplnej umożliwia bardziej efektywne i precyzyjne sterowanie temperaturą, co jest istotne w produkcji elementów o złożonych geometriach.
- Minimalizacja zniekształceń wyprasek - Równomierny rozkład temperatury minimalizuje ryzyko zniekształceń i innych wad, poprawiając ogólną jakość produktów.
- Unikanie wad wyprasek - Technologia ta eliminuje typowe problemy, takie jak widoczne punkty wtrysku czy linie łączenia, co jest szczególnie ważne dla estetyki wyrobów.
Co ma wpływ na efektywność chłodzenia form wtryskowych?
Na efektywność chłodzenia form wtryskowych wpływa przede wszystkim ułożenie kanałów chłodzących i projekt obwodu. Poniżej tłumaczymy, dlaczego.
Ułożenie kanałów chłodzących
Rozmieszczenie kanałów chłodzących w formie ma decydujący wpływ na jednorodność temperatury jej powierzchni. Istotnymi parametrami są tutaj głębokość i rozstaw kanałów. Na przykład w stalowych formach P20 ze średnicą linii wodnej 11,1 mm (D) i temperaturą chłodziwa 30°C, różne konfiguracje mogą znacznie wpływać na efektywność chłodzenia.
Wytłumaczymy to sobie na kilku scenariuszach:
- Głębokość 1.0D i rozstaw 2.5D - Powierzchnia formy pozostaje stosunkowo jednorodna z różnicą temperatur w okolicach 1°C. Natomiast średnia temperatura jest o około 10°C wyższa, niż temperatura chłodziwa.
- Głębokość 1.0D i rozstaw 10D - Różnica temperatur na powierzchni formy wzrasta do 25°C, a średnia temperatura osiąga 56°C. Pokazuje to, że kanały rozmieszczone dalej od siebie chłodzą mniej efektywnie.
- Głębokość 5D i rozstaw 10D - Temperatura powierzchni formy pozostaje jednorodna w granicach 2°C, ale średnia temperatura jest o 46°C wyższa, niż temperatura chłodziwa.
Skuteczne ułożenie kanałów chłodzących powinno zapewnić jednorodną temperaturę powierzchni formy, która nie jest znacznie wyższa, niż temperatura chłodziwa.
Projekt obwodu
Projektanci form mają do wyboru dwa główne typy obwodów chłodzenia: równoległe i szeregowe.
- Obwody równoległe - Kanały chłodzące są wiercone prosto przez formę od kolektora doprowadzającego do zbierającego. Zróżnicowanie oporów przepływu w poszczególnych kanałach prowadzi do różnic w efektywności transferu ciepła, co może generować "gorące punkty" i powodować nierównomierne chłodzenie.
- Obwody szeregowe - Kanały chłodzące połączone są w jedną pętlę, od wlotu do wylotu chłodziwa. Jest to rozwiązanie częściej stosowane, ponieważ umożliwia utrzymanie jednolitego przepływu przez całą długość kanału, co jest preferowane dla osiągnięcia optymalnej efektywności chłodzenia.
Odpowiedni projekt układu chłodzenia form wtryskowych jest kluczowy dla minimalizacji zniekształceń i maksymalizacji wydajności cyklu produkcyjnego.
Jakie narzędzia są potrzebne do chłodzenia form wtryskowych?
Do chłodzenia form wtryskowych potrzebne są liczne narzędzia, takie jak:
- Węże do układów chłodzenia - Niezbędne do przesyłania medium chłodzącego do i z formy. Muszą być wykonane z materiałów odpornych na wysokie ciśnienia i temperatury, jak również na ewentualne agresywne składniki chłodziwa. Węże do form wtryskowych zwykle są elastyczne, co pozwala na łatwe układanie ich w przestrzeniach maszynowych i dopasowanie do różnorodnych konfiguracji form.
- Szybkozłącza do form wtryskowych - Umożliwiają szybkie podłączanie i odłączanie linii chłodzących bez konieczności używania narzędzi. Szybkozłącza do form zapewniają również szczelność połączeń, co jest istotne dla likwidacji przecieków i utrzymania ciśnienia w systemie. Dzięki różnym rozmiarom i typom komponenty te można łatwo dopasować do specyficznych wymagań form i instalacji.
- Manometry i regulatory przepływu - Urządzenia służące do monitorowania i regulacji ciśnienia oraz przepływu medium chłodzącego. Manometry pozwalają na bieżące śledzenie ciśnienia w systemie, co jest ważne dla zapobiegania przeciążeniom i uszkodzeniom. Z kolei regulatory przepływu umożliwiają precyzyjne dostosowanie ilości chłodziwa przepływającego przez formę, co ma bezpośredni wpływ na skuteczność chłodzenia.
- Pompy i kolektory - Odpowiadają za ciągłe i równomierne dostarczanie medium chłodzącego do systemu. Pompy muszą być dostosowane do wymagań systemu pod kątem wydajności i odporności na temperaturę oraz ciśnienie. Z kolei kolektory rozdzielają przepływ chłodziwa na poszczególne kanały chłodzące w formie.
- Systemy filtracji - Filtrują chłodziwo, usuwając z niego zanieczyszczenia, co jest kluczowe dla utrzymania sprawności hydraulicznej systemu i ochrony komponentów przed zatarciami i uszkodzeniami.
- Oprogramowanie do zarządzania temperaturą - Nowoczesne systemy chłodzenia mogą być wyposażone w oprogramowanie do monitorowania i automatycznego regulowania temperatury w formach, co zwiększa precyzję i redukuje ryzyko błędów produkcyjnych.
Czy chillery mogą chłodzić formy wtryskowe?
Tak, chillery mogą chłodzić formy wtryskowe. Chillery to urządzenia, które obniżają temperaturę cieczy chłodzącej i utrzymują ją na stałym, niskim poziomie, co jest kluczowe dla efektywnego odprowadzania ciepła.
Dzięki wykorzystaniu chillerów możliwe jest precyzyjne kontrolowanie temperatury formy, co ma bezpośredni wpływ na jakość wyprasek. Równomierne i efektywne chłodzenie zapobiega deformacjom, zmniejsza naprężenia wewnętrzne w produkcie końcowym i skraca czas cyklu produkcyjnego przez szybsze twardnienie materiału.
Chillery są szczególnie przydatne w produkcji wielkoseryjnej, gdzie stabilność procesu chłodzenia wpływa na powtarzalność i jakość wyrobów.
Stosowanie chillerów pozwala także na znaczną oszczędność wody, ponieważ pracują one w obiegu zamkniętym, co redukuje całkowite zużycie cieczy chłodzącej. Jest to zarówno ekonomicznie korzystne, jak i bardziej zrównoważone ekologicznie w porównaniu z tradycyjnymi systemami chłodzenia, które wymagają ciągłego dopływu świeżej wody.
Jakie czynniki chłodnicze są używane do chłodzenia form wtryskowych?
Do chłodzenia form wtryskowych używane są różne czynniki chłodnicze takie jak woda, oleje czy glikole. Można podzielić na kilka głównych kategorii:
- Woda - Najczęściej stosowane chłodziwo ze względu na jego dostępność, niski koszt i dobre właściwości termiczne. Woda jest efektywna w przenoszeniu ciepła, ale jej użycie może wymagać odpowiedniego systemu filtracji i oczyszczania, aby zapobiegać osadzaniu się kamienia i korozji w kanałach chłodzących. Specjalne węże do gorącej wody są wymagane do transportu wody w formach wtryskowych.
- Oleje - Używane głównie w bardzo wysokich temperaturach pracy, które mogłyby być szkodliwe dla systemów opartych na wodzie. Oleje mają wyższą pojemność cieplną, co sprawia, że są skuteczne w utrzymaniu stabilnych temperatur. Ich użycie jest jednak droższe i wymaga specjalnych systemów utrzymania czystości oraz recyklingu.
- Glikole (np. etylenoglikol, propylenoglikol) - Dodaje się je do wody w celu obniżenia jej punktu zamarzania i zapobiegania korozji w systemie chłodzącym.
- Ciecze chłodzące specjalistyczne - Mogą zapewniać lepsze parametry chłodzenia w specyficznych warunkach, np. w bardzo wysokich temperaturach lub przy specjalnych wymaganiach dotyczących przewodności cieplnej.
Wybór odpowiedniego czynnika chłodniczego zależy od wielu czynników, w tym od wymagań procesu produkcyjnego, rodzaju materiału przetwarzanego w formie, oraz od aspektów ekonomicznych i środowiskowych związanych z eksploatacją systemu chłodzenia.
Jak obliczany jest czas potrzebny na chłodzenie form wtryskowych?
Czas potrzebny na chłodzenie form wtryskowych jest obliczany na podstawie wielu czynników związanych z właściwościami materiału, geometrią wyrobu, oraz specyfikacją formy i systemu chłodzenia. Oto główne kwestie uwzględniane przy obliczaniu czasu chłodzenia:
- Analiza termiczna formy - Za pomocą modelowania komputerowego ocenia się, jak ciepło jest przekazywane i usuwane z formy. Symulacje CFD (Computational Fluid Dynamics) pozwalają zobaczyć, jak temperatura rozchodzi się w formie i jak szybko jest usuwana przez system chłodzenia.
- Właściwości materiału - Każde tworzywo sztuczne ma specyficzne właściwości termiczne, takie jak przewodność cieplna, ciepło właściwe, i temperatura przetwarzania, które muszą być uwzględnione. Materiały o wyższej przewodności cieplnej mogą szybciej oddawać ciepło, co skraca czas chłodzenia.
- Geometria wypraski - Grubość i złożoność kształtu wypraski mają znaczący wpływ na czas chłodzenia. Grubsze sekcje będą chłodziły się dłużej ze względu na większą masę materiału i mniejszą powierzchnię kontaktu z kanałami chłodzącymi.
- Temperatura formy i wtrysku - Optymalna temperatura formy oraz temperatura, z jaką materiał jest wtryskiwany do formy, określają ilość ciepła, które musi być usunięte w procesie chłodzenia. Im wyższa temperatura początkowa, tym dłuższy czas chłodzenia.
- Temperatura wyformowania wypraski - Jest to docelowa temperatura, przy której wypraska może być bezpiecznie wyjęta z formy bez ryzyka deformacji. Jest ona ściśle powiązana z właściwościami termicznymi użytego tworzywa.
- Parametry chłodzenia - Obejmują temperaturę i przepływ medium chłodzącego, a także rozmieszczenie i efektywność kanałów chłodzących. Lepsza cyrkulacja i niższa temperatura medium chłodzącego mogą znacznie skrócić czas chłodzenia.
Jak skrócić czas chłodzenia form wtryskowych?
Czas chłodzenia form wtryskowych można skrócić za pomocą kilku sprawdzonych metod, takich jak:
- Optymalizacja układu kanałów chłodzących - Projekt kanałów chłodzących powinien być jak najbardziej efektywny, z kanałami rozmieszczonymi równomiernie i jak najbliżej najgrubszych części wypraski. Użycie symulacji przepływu ciepła (CFD) pomoże zoptymalizować rozmieszczenie kanałów i ich efektywność.
- Zwiększenie przepływu medium chłodzącego - Użycie pomp o większej mocy i lepszej efektywności może zwiększyć przepływ chłodziwa przez kanały, co skutkuje szybszym odprowadzaniem ciepła z formy.
- Zastosowanie zaawansowanych materiałów do form - Materiały o lepszej przewodności cieplnej, takie jak miedź lub aluminium, mogą skutecznie przyspieszyć odprowadzanie ciepła z formy, skracając czas chłodzenia.
- Regulacja temperatury medium chłodzącego - Obniżenie temperatury chłodziwa może znacząco wpłynąć na czas chłodzenia. Jednak należy to robić rozważnie, aby uniknąć kondensacji lub zbyt gwałtownego chłodzenia, które mogłoby prowadzić do wad materiałowych.
- Optymalizacja cyklu wtrysku - Dostosowanie parametrów wtrysku, takich jak ciśnienie, prędkość i czas wtrysku, również wpływa na szybkość chłodzenia, gdyż odpowiednie ustawienia mogą zredukować ilość ciepła generowanego w procesie.
- Zastosowanie izolacji termicznej - Izolowanie formy od zewnętrznych źródeł ciepła oraz izolowanie samej formy może zmniejszyć straty ciepła i skupić proces chłodzenia tam, gdzie jest najbardziej potrzebny.
Implementacja powyższych metod często wymaga początkowych inwestycji w nowe technologie, materiały czy oprogramowanie, ale zwykle przynosi znaczące korzyści w postaci krótszych cykli produkcyjnych i niższych kosztów operacyjnych.
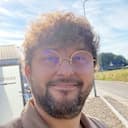
Autor artykułu
Bartosz Kułakowski
CEO Hosetech Sp.z o.o.
Bartosz Kułakowski jest specjalistą od węży i złączy przemysłowych z ponad 10 letnim doświadczeniem. Bartosz jest obecny w branży technicznej od 2013 roku. Zdobywał doświadczenie jako doradca techniczno-handlowy w sektorze tworzywowych taśm przenośnikowych, konstrukcji stalowych, węży i złączy przemysłowych. Od 2016 roku specjalizuje się wyłącznie w wężach i złączach. Twórca firmy HOSETECH Bartosz Kułakowski, obecnie HOSETECH Sp. z o.o.
Spis treści
Czym jest chłodzenie form wtryskowych?
Dlaczego chłodzenie form wtryskowych jest ważne?
Czym jest bilans cieplny formy wtryskowej?
Jaka powinna być temperatura formy wtryskowej?
Jak działa układ chłodzenia formy wtryskowej?
Jakie elementy wtryskarki wymagają chłodzenia?
Jakie są techniki chłodzenia form wtryskowych?
Konwencjonalny układ chłodzący form wtryskowych
Chłodzenie konformalne form wtryskowych
Chłodzenie konturowe form wtryskowych
Technologia BFMOLD
Co ma wpływ na efektywność chłodzenia form wtryskowych?
Ułożenie kanałów chłodzących
Projekt obwodu
Jakie narzędzia są potrzebne do chłodzenia form wtryskowych?
Czy chillery mogą chłodzić formy wtryskowe?
Jakie czynniki chłodnicze są używane do chłodzenia form wtryskowych?
Jak obliczany jest czas potrzebny na chłodzenie form wtryskowych?
Jak skrócić czas chłodzenia form wtryskowych?
Te produkty mogą Cię zainteresować