Budowa wtryskarek – jak zbudowane są wtryskarki?
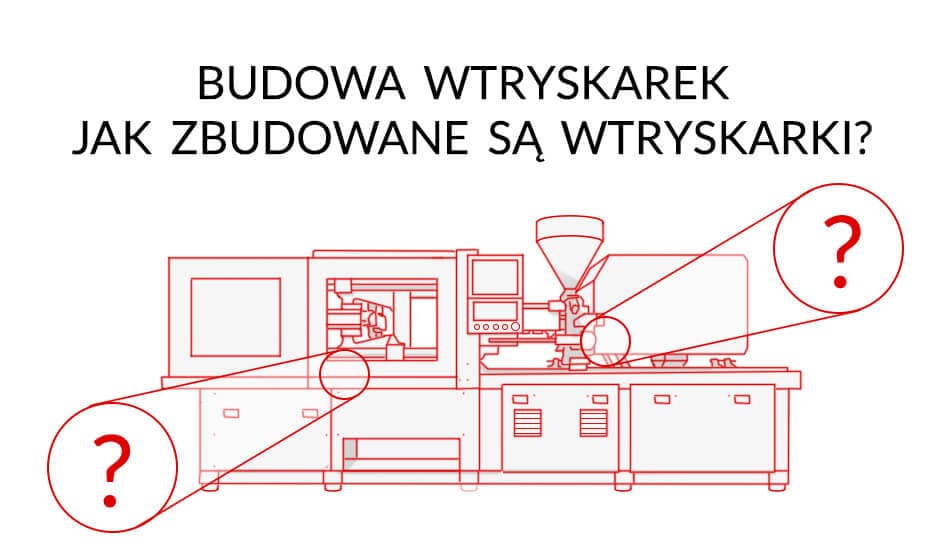
Z jakich elementów zbudowana jest wtryskarka?
Wtryskarka zbudowana jest z następujących elementów:
- zbiornik tworzywa,
- cylinder,
- ślimak,
- układ napędowy ślimaka,
- elementy grzejne,
- układ rozłączający,
- układ wyrzutnikowy,
- siłowniki hydrauliczne,
- układ zamknięcia formy,
- układ chłodzenia,
- układ grzejny formy,
- gniazdo formujące,
- układ wypychanie wypraski,
- układ usuwania wlewka,
- elementy prowadzące i ustalające połówki formy,
- napędy płyt i segmentów,
- obudowa,
- węże do form wtryskowych,
- szybkozłącza do form wtryskowych.
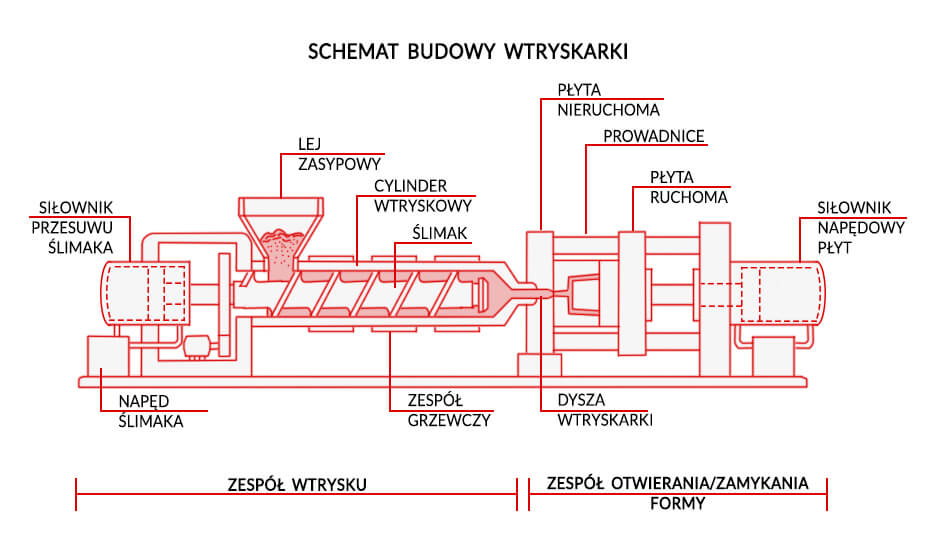
Zbiornik tworzywa
Zbiornik tworzywa to kluczowy element wtryskarki, gdzie wsypywane są granulaty plastiku przed rozpoczęciem procesu wtrysku. Zbiornik ten często jest wyposażony w jednostkę suszącą, która usuwa wilgoć z tworzywa, co przekłada się na lepszą jakość końcowego produktu. Dodatkowo, w celu ochrony maszyny przed szkodliwymi metalicznymi cząstkami, wewnątrz zbiornika czasem znajdują się małe magnesy.
Po osuszeniu materiał trafia do kolejnego ważnego komponentu maszyny - cylindra.
Cylinder
Cylinder to miejsce, w którym plastik jest ogrzewany do stanu ciekłego, umożliwiającego dalszy przepływ. Wewnątrz cylindra znajduje się także ślimak, który wstrzykuje stopione tworzywo do form znajdujących się w jednostce zamykającej.
Temperatura w cylindrze musi być starannie regulowana, aby odpowiadała różnym rodzajom tworzyw sztucznych.
Do funkcji cylindra zaliczamy: transport, zagęszczanie, topienie, mieszanie i przetłaczanie plastiku, zanim dotrze do formy wtryskowej.
Ślimak
Ślimak wtryskarki działa na zasadzie śruby zwrotnej. Został opracowany w połowie lat 50. XX wieku i szybko zastąpił starsze systemy. Jego konstrukcja pozwala bowiem na skuteczne zarządzanie temperaturą stopionego plastiku.
Głównym zadaniem ślimaka wtryskarki jest przemieszczanie materiału przez cylinder.
Początkowo, gdy granulki tworzywa są podawane ze zbiornika do cylindra, ślimak obraca się, przesuwając materiał do przodu, podczas gdy dodawane są kolejne porcje surowca. Lotki ślimaka zapewniają ciągłe mieszanie, które równomiernie rozprowadza ciepło po całej masie.
Mieszanie pomaga również w czyszczeniu mechanizmu z różnych materiałów i pozostałości kolorów z wcześniejszych cykli produkcyjnych odbywających się na tej samej wtryskarce.
Ślimak dostarcza większość ciepła do termoformowalnego plastiku, głównie przez zmniejszanie średnicy w miarę zbliżania się do końcówki, co zmusza granulki do przesuwania się wzdłuż lotek, kompresji w ciaśniejszej przestrzeni i mieszania poprzez tarcie. Dzięki temu tworzywo równomiernie nagrzewa się do odpowiedniej temperatury.
Układ napędowy ślimaka
Układ napędowy ślimaka odpowiada za precyzyjne dozowanie i transport tworzywa w maszynie. Współczesne wtryskarki korzystają głównie z napędu hydraulicznego, napędzanego silnikiem elektrycznym i pompą hydrauliczną. Pozwala on na skuteczne i ciągłe przemieszczanie ślimaka.
Poza tym, w celu osiągnięcia bardzo wysokiej dokładności i powtarzalności (szczególnie przy produkcji małych i precyzyjnych elementów), stosowane są także napędy elektryczne. Charakteryzują się one znakomitą kontrolą nad procesem wtrysku, co jest niezbędne w precyzyjnej fabrykacji.
Elementy grzejne
Elementy grzejne są niezbędne do utrzymania odpowiedniej temperatury w cylindrze, co umożliwia jego upłynnienie i formowanie wtryskowe tworzywa. We wtryskarkach stosuje się głównie elektryczne elementy grzejne, takie jak opaski lub grzałki patronowe i spiralne. Są one montowane wokół cylindra oraz w innych strategicznych miejscach maszyny, jak dysze czy płyty formujące, aby zapewnić równomierny rozkład ciepła.
Istotna jest zdolność grzałek do szybkiego reagowania na zmiany w procesie wtrysku, co gwarantuje stabilność termiczną i wysoką jakość wyprasek.
Układ rozłączający
Układ rozłączający oddziela ślimak od jego napędu w kluczowych momentach procesu, takich jak faza wtrysku, kiedy to ślimak działa jak tłok. Mechanizm ten jest fundamentalny dla prawidłowego działania maszyny, ponieważ umożliwia przekształcenie ruchu obrotowego ślimaka w ruch liniowy, niezbędny do precyzyjnego wtrysku tworzywa do formy.
Układ rozłączający zapewnia, że każdy cykl wtryskowy jest dokładny i powtarzalny, co gwarantuje zachowanie stałej jakości produkcji.
Układ wyrzutnikowy
Układ wyrzutnikowy odpowiada za oddzielanie gotowych wyprasek od formy po zakończeniu procesu wtrysku i schłodzeniu. We wtryskarkach stosowane są różne typy układów wyrzutnikowych:
- hydrauliczne,
- mechaniczne,
- pneumatyczne.
Hydrauliczne układy wyrzutnikowe działają na zasadzie automatycznych inicjatorów sterowanych sekwencyjnie, co zapewnia szybkie i czyste oddzielenie produktu od formy. Mechaniczne wykorzystują siłę mechaniczną formy, która otwierając się, naciska na stemple wybijające wypraskę. Z kolei pneumatyczne używają ciśnienia powietrza do wytworzenia siły potrzebnej do oddzielenia wypraski od formy.
Każde z tych rozwiązań jest dostosowane do specyficznych wymagań produkcyjnych, co pozwala na optymalizację procesu wtrysku.
Siłowniki hydrauliczne
Siłowniki hydrauliczne są odpowiedzialne za wywieranie dużych sił niezbędnych do utrzymania formy zamkniętej podczas wtrysku oraz do jej otwierania po zakończeniu cyklu. Ponadto wprawiają tłok w ruch postępowy.
Działanie siłowników jest efektywne i precyzyjne, co zapewnia stabilność oraz powtarzalność procesów produkcyjnych.
Układ zamknięcia formy
W nowoczesnych wtryskarkach często stosuje się kolanowy układ zamknięcia formy. Jego główną rolą jest utrzymanie formy szczelnie zamkniętej w obliczu rosnącego ciśnienia podczas wtrysku tworzywa.
Zamykanie i otwieranie formy odbywa się za pomocą wspomnianych siłowników hydraulicznych, co pozwala na kompaktową konstrukcję samej wtryskarki. Typowo układ zamknięcia formy składa się z dwóch centralnie zamontowanych siłowników:
- większego (zewnętrznego), odpowiedzialnego za podstawowe otwieranie i zamykanie formy,
- mniejszego (wewnętrznego), który zapewnia odpowiednie dociśnięcie formy i chroni przed jej rozwarciem podczas wtrysku.
Układ chłodzenia
We wtryskarkach znajdują się dwa główne układy chłodzenia:
- układ chłodzenia oleju hydraulicznego,
- układ chłodzenia formy.
Układ chłodzenia oleju hydraulicznego obniża temperaturę oleju hydraulicznego, utrzymując ją w zakresie 35-60°C, co jest kluczowe dla optymalnego działania hydrauliki. Natomiast układ chłodzenia formy ma za zadanie obniżyć temperaturę wypraski przed otwarciem formy, czym zapewnia jej odpowiednią sztywność i ułatwia wyrzut z formy.
Układ grzejny formy
Układ grzejny formy jest niezbędny w procesie wtrysku, szczególnie w przypadku większych form o skomplikowanej geometrii i długich kanałach wtryskowych. Zapobiega on bowiem zastygnięciu materiału w kanałach, co jest kluczowe dla ciągłości produkcji.
Układy grzejne formy dzielimy je na wbudowane (wewnętrzne) oraz zewnętrzne, które są sterowane niezależnie od panelu kontrolnego maszyny. Zarówno wewnętrzne, jak i zewnętrzne systemy muszą być precyzyjnie regulowane, aby zapewnić równomierne ogrzewanie, co jest niezbędne dla jakości finalnego produktu.
Gniazdo formujące
Gniazdo to część formy, w której kształtowana jest wypraska. Musi być precyzyjnie wykonane, aby odwzorować żądane detale produktu końcowego.
Układ wypychania wypraski
Układ wypychania wypraski umożliwia usunięcie gotowego produktu z formy. W jego skład wchodzą przede wszystkim sworznie wypychaczy, które są zainstalowane w tylnej części formy. Po schłodzeniu i zastygnięciu tworzywa, sworznie popychają gotową część na zewnątrz.
Z powodu ich pracy na wyprodukowanej części często pozostaje charakterystyczne wgłębienie, znane jako ślad po sworzniach.
Istnieje kilka rodzajów sworzni wypychaczy, w tym te hartowane na wskroś dla jednolitej twardości oraz hartowane powierzchniowo, które są odporniejsze i stosowane w bardziej wymagających systemach odlewniczych.
Układ usuwania wlewka
Wlewek to nadmiar tworzywa, który powstaje w procesie wtryskowym. Układ usuwania wlewka służy do oddzielania go od właściwej wypraski, co zazwyczaj odbywa się automatycznie.
Wlewki mogą być usuwane mechanicznie lub za pomocą specjalnych narzędzi cięcia. Zależy to od konstrukcji formy i rodzaju tworzywa.
Elementy prowadzące i ustalające połówki formy
Elementy prowadzące i ustalające dbają o dokładne dopasowanie połówek formy w procesie wtrysku. Linia podziału formy, czyli miejsce, gdzie obie jej połówki łączą się, jest kluczowa dla jakości końcowego produktu. Nieprawidłowe dopasowanie może prowadzić do wad produkcyjnych, takich jak nierówności czy nieszczelności.
Formy dzielone, w których szczęki formujące tworzą wnękę formy, są przykładem zastosowania mechanizmów prowadzących, zapewniających precyzyjne zamykanie i otwieranie formy.
Napędy płyt i segmentów
Napędy płyt i segmentów w jednostce zamykającej odgrywają kluczową rolę w otwieraniu i zamykaniu formy oraz w wypychaniu gotowych wyprasek. Wyróżniamy dwa główne typy systemów zamykających:
- hydrauliczne,
- dźwigniowe.
System hydrauliczny wykorzystuje jeden lub więcej cylindrów hydraulicznych do kontroli ruchu płyt, natomiast system dźwigniowy opiera się na szeregu połączeń, które efektywnie przekształcają ruch obrotowy w liniowy.
W jednostce zamykającej znajdują się także inne komponenty, np. wypychacze maszynowe, ruchoma i stała płyta, a także pręty prowadzące, które wspólnie zapewniają sprawne działanie mechanizmu otwierania i zamykania formy oraz wypychania produktów.
Obudowa wtryskarki
Obudowa wtryskarki chroni mechanizm wtryskarki oraz przed urazami. Zazwyczaj jest wykonana z wytrzymałych materiałów, takich jak stal czy tworzywa sztuczne, co zapewnia stabilność i bezpieczeństwo operacji. Poza tym pełni również funkcje izolacyjne, ponieważ ogranicza hałas oraz minimalizuje utratę ciepła, zapewniając efektywność energetyczną.
Współczesne obudowy są projektowane tak, aby umożliwić łatwy dostęp do wewnętrznych komponentów maszyny, co ułatwia konserwację i przeglądy techniczne.
Węże do form wtryskowych
Węże do form wtryskowych są kluczowym elementem systemu przesyłowego, który dostarcza i odbiera różne media, takie jak chłodziwa, oleje hydrauliczne czy gazy. Dlatego jakość i konstrukcja węży ma bezpośredni wpływ na skuteczność procesów chłodzenia, smarowania i innych funkcji pomocniczych.
Węże do gorącej wody są dostępne w różnych wymiarach i typach, co umożliwia dopasowanie ich do specyficznych wymagań maszyny oraz procesu produkcyjnego. Jednak przede wszystkim powinny być odporne na wysokie ciśnienia i temperatury, bo tylko wtedy mogą zapewnić długotrwałą i bezawaryjną pracę.
Szybkozłącza do form wtryskowych
Szybkozłącza do form wtryskowych to specjalistyczne komponenty umożliwiające szybkie i efektywne łączenie lub rozłączanie linii przesyłowych, takich jak te przewodzące olej, wodę czy powietrze. Ich zastosowanie znacząco skraca czas potrzebny na zmianę formy, co jest istotne w szybko zmieniających się warunkach produkcyjnych.
Szybkozłącza są zaprojektowane tak, aby zapewniać szczelność połączenia oraz wytrzymałość na ciśnienie i temperaturę, co minimalizuje ryzyko przecieków i innych awarii. Z kolei szeroki wybór ich rozmiarów i typów umożliwia dostosowanie armatury do różnorodnych zastosowań w przemyśle wtryskowym.
Jakie są rodzaje ślimaków we wtryskarkach?
Rodzaje ślimaków we wtryskarkach są następujące:
- ślimak standardowy,
- ślimak mieszający,
- ślimak specjalny,
- ślimak z odgazowaniem,
- ślimak wysokowydajny.
Poniżej opisujemy każdy z nich.
Ślimak standardowy
Ślimak standardowy to najbardziej uniwersalne rozwiązanie stosowane we wtryskarkach. Jest przystosowany do przetwarzania różnorodnych materiałów, co sprawia, że znajduje zastosowanie w wielu aplikacjach.
Chociaż nie zawsze oferuje optymalną wydajność przy pracy ze specjalistycznymi materiałami, w większości przypadków skutecznie spełnia stawiane mu wymagania. Dlatego jest to podstawowy wybór dla wielu procesów wtryskowych, szczególnie gdy przetwarzane tworzywo nie wymaga specjalistycznych właściwości mechanicznych lub termicznych.
Ślimak mieszający
Ślimak mieszający został zaprojektowany do szczególnie precyzyjnego ujednolicenia masy tworzyw sztucznych. Jego zastosowanie jest kluczowe przy dodawaniu pigmentów barwiących oraz granulatów proszkowych, które wymagają dokładnego homogenizowania.
Ślimak ten doskonale sprawdza się również w przypadku przetwarzania kompozycji wieloskładnikowych, gdzie istotne jest uzyskanie jednolitej konsystencji i właściwości materiału końcowego. Dlatego stanowi preferowane rozwiązanie w aplikacjach wymagających wysokiej jednorodności mechanicznej i termicznej wyrobu.
Ślimaki specjalne
Ślimaki specjalne są dostosowane do specyficznych wymagań materiałów z unikalnymi właściwościami termicznymi, reologicznymi lub trybologicznymi. Typy tworzyw, dla których są przeznaczone, to np. PVC, duroplasty czy elastomery.
Jako że ślimaki tego typu są projektowane i produkowane z myślą o optymalizacji procesu przetwarzania trudnych w obróbce surowców, pozwalają na osiągnięcie najlepszych możliwych rezultatów w produkcji detali z wymienionych tworzyw.
Ślimak z odgazowaniem
Ślimak z odgazowaniem to specjalistyczne rozwiązanie stosowane przy przetwarzaniu materiałów higroskopijnych, które muszą być dokładnie osuszone przed obróbką. Jest to szczególnie ważne w produkcjach, gdzie wymagana jest wysoka jakość optyczna i technologiczna wyprasek.
Ślimak tego typu umożliwia efektywne odgazowanie i eliminację wilgoci z materiału, co jest kluczowe dla zachowania właściwości fizycznych oraz estetycznych finalnego produktu.
Ślimak wysokowydajny
Ślimak wysokowydajny powstał z myślą o maksymalizacji wydajności procesu plastyfikacji. Jego zastosowanie redukuje czas cyklu, jednocześnie podnosząc jakość roztopionej masy. Ślimak wysokowydajny jest też oznaczany skrótem HP od High Performance.
Dzięki obecności elementów mieszających oraz szczelin ścinających, ślimak umożliwia np. lepsze i bardziej równomierne barwienie materiałów przy mniejszym udziale środków barwiących. Jest to rozwiązanie ekonomiczne, pozwalające na zmniejszenie kosztów wtryskiwania oraz zużycia energii, a jego zastosowanie jest szczególnie korzystne w przypadkach dużych przerobów materiałowych oraz wysokich wymagań jakościowych.
Jak często wymieniać części wtryskarki?
Części wtryskarki należy wymieniać w różnych odstępach czasu, w zależności od intensywności użytkowania maszyny, rodzaju przetwarzanego tworzywa, a także specyfikacji technicznych i rekomendacji producenta. Dlatego nie ma jednolitej odpowiedzi na pytanie, jak często powinno się to robić.
Jednak istnieją ogólne wytyczne, które pomagają w utrzymaniu wtryskarki w dobrym stanie technicznym.
Części ruchome, takie jak śruby, cylindry czy tłoki, powinny być sprawdzane regularnie pod kątem zużycia i wymieniane, gdy ich stan techniczny przestaje spełniać wymogi bezpieczeństwa i efektywności. Przy intensywnym użytkowaniu maszyny wymiana może być konieczna nawet co 6 miesięcy.
Elementy hydrauliczne i pneumatyczne, w tym pompy i zawory, również są narażone na uszkodzenia z powodu ciągłego ciśnienia i przepływu. Dlatego ich wymiana powinna następować co najmniej raz w roku lub częściej, jeśli obserwuje się przecieki czy spadek wydajności.
Z kolei elementy elektryczne, takie jak czujniki i przekaźniki, mogą wymagać wymiany co 1-2 lata, w zależności od warunków eksploatacji i częstości występowania awarii.
Płyty formujące i komponenty formy warto monitorować pod kątem pęknięć i innych uszkodzeń strukturalnych. Ich wymiana zależy od jakości materiałów i precyzji wykonania, a także od skomplikowania detali, które są formowane.
Oprócz tego filtry, uszczelnienia i smary powinny być wymieniane zgodnie z planem serwisowym, zwykle raz na rok, aby zapewnić optymalne smarowanie i ochronę przed zanieczyszczeniami.
Pamiętaj, że dokładny harmonogram wymiany części powinien być dostosowany do indywidualnych warunków pracy wtryskarki i zaleceń producenta. Regularne przeglądy techniczne i serwisowanie są kluczowe dla wydłużenia żywotności maszyny i utrzymania jej w pełnej gotowości produkcyjnej.
Jak dbać o części wtryskarki?
Aby dbać o części wtryskarki, warto zwracać uwagę na regularne czyszczenie, smarowanie i kontrolę stanu technicznego maszyny. Podczas konserwacji wtryskarki należy kierować się kilkoma podstawowymi zasadami, które pomogą utrzymać maszynę w optymalnej kondycji:
- Regularne czyszczenie - Systematyczne usuwanie resztek tworzywa, pyłu i brudu z maszyny zapobiega akumulacji zanieczyszczeń, które mogą prowadzić do uszkodzeń mechanicznych i przegrzewania. Szczególną uwagę należy zwrócić na czyszczenie elementów ruchomych, takich jak śruby i cylindry.
- Smarowanie - Wszystkie ruchome części maszyny, w tym łożyska i prowadnice, wymagają regularnego smarowania, aby zapewnić płynną pracę i zmniejszyć tarcie, co przyczynia się do mniejszego zużycia komponentów. Zaleca się stosowanie smarów wskazanych przez producenta maszyny.
- Sprawdzanie stanu technicznego - Regularne inspekcje techniczne pozwalają na wczesne wykrycie potencjalnych problemów, takich jak pęknięcia, zarysowania lub inne usterki mechaniczne. Części z widocznymi uszkodzeniami należy natychmiast wymienić.
- Utrzymanie temperatury roboczej - Przestrzeganie zaleceń producenta odnośnie temperatur roboczych jest istotne. Nadmierna temperatura może uszkodzić części plastikowe i gumowe, dlatego ważne jest jej kontrolowanie i regulowanie w maszynie.
- Odpowiednie ustawienia wtryskarki - Niewłaściwe ustawienie parametrów wtrysku, takich jak ciśnienie, prędkość czy temperatura, może przyczynić się do przedwczesnego zużycia części. Dlatego istotne jest dokładne dostosowanie ustawień do przetwarzanego materiału i specyfikacji produktu.
- Regularne przeglądy serwisowe - Przestrzeganie harmonogramu przeglądów serwisowych zalecanego przez producenta maszyny zapewnia, że wszelkie problemy zostaną szybko zidentyfikowane i naprawione, minimalizując ryzyko długotrwałych przestojów.
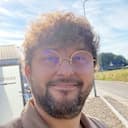
Autor artykułu
Bartosz Kułakowski
CEO Hosetech Sp.z o.o.
Bartosz Kułakowski jest specjalistą od węży i złączy przemysłowych z ponad 10 letnim doświadczeniem. Bartosz jest obecny w branży technicznej od 2013 roku. Zdobywał doświadczenie jako doradca techniczno-handlowy w sektorze tworzywowych taśm przenośnikowych, konstrukcji stalowych, węży i złączy przemysłowych. Od 2016 roku specjalizuje się wyłącznie w wężach i złączach. Twórca firmy HOSETECH Bartosz Kułakowski, obecnie HOSETECH Sp. z o.o.
Spis treści
Z jakich elementów zbudowana jest wtryskarka?
Zbiornik tworzywa
Cylinder
Ślimak
Układ napędowy ślimaka
Elementy grzejne
Układ rozłączający
Układ wyrzutnikowy
Siłowniki hydrauliczne
Układ zamknięcia formy
Układ chłodzenia
Układ grzejny formy
Gniazdo formujące
Układ wypychania wypraski
Układ usuwania wlewka
Elementy prowadzące i ustalające połówki formy
Napędy płyt i segmentów
Obudowa wtryskarki
Węże do form wtryskowych
Szybkozłącza do form wtryskowych
Jakie są rodzaje ślimaków we wtryskarkach?
Ślimak standardowy
Ślimak mieszający
Ślimaki specjalne
Ślimak z odgazowaniem
Ślimak wysokowydajny
Jak często wymieniać części wtryskarki?
Jak dbać o części wtryskarki?
Te produkty mogą Cię zainteresować