Bend radius - Definition, How To Calculate, Types
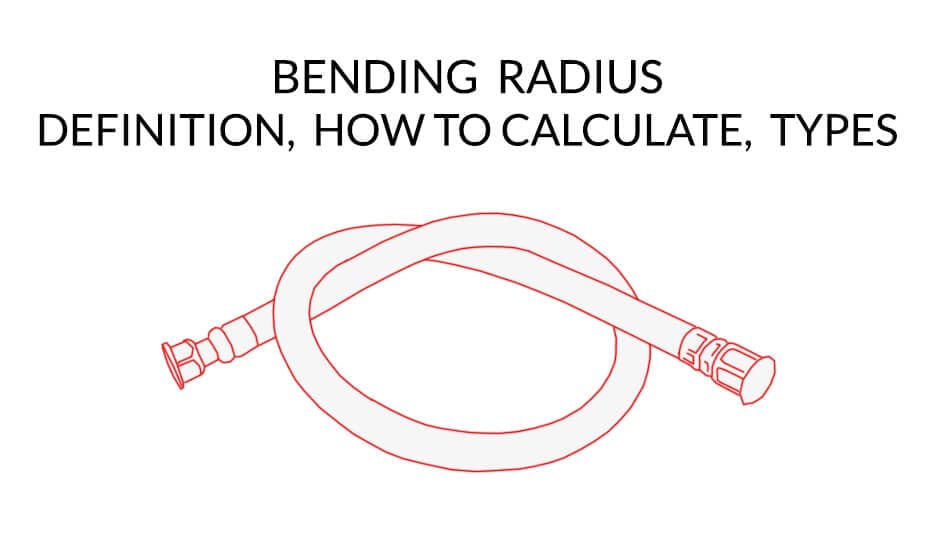
What is the bend radius?
The bend radius is the distance to the inside edge of the hose (not the centreline) when making a 90° turn. Measurements of bend radius are made under controlled laboratory conditions. The bend radius is a key parameter when selecting a hose, especially if it will be subjected to sharp turns in daily use.
A bending angle that is too sharp can cause excessive stress or distortion of the hose reinforcement, shortening its life.
The concept of "force to bend" is worth noting, which defines the amount of tension needed to bend a hose around a certain bend radius. Short hoses, thick walls, large diameters or heavy construction will not bend easily without significant physical effort.
In practice, the bend radius and the force to bend determine the flexibility and durability of the hose in specific applications.
What is the minimum bend radius?
The minimum bend radius is the shortest distance a hose can be bent without causing permanent damage.
How to measure the minimum bend radius?
There are two ways to measure the minimum bend radius: inner radius and centreline radius. The inner radius measures the distance to the nearest inner surface of the bent hose. This is a more precise measurement that helps assess the risk of damage to the internal structure of the hose. The centreline radius measures the distance to the centreline of a hose or flexible hose. Although less accurate, this measurement is often used because of its ease of use in practice.
Knowing the minimum bend radius is crucial to ensure the durability and reliability of the hose in various applications, as it helps minimize the risk of damage and extend the life of the hose.
Why is hose bend radius important?
The hose bend radius is important because it helps prevent hose deformation, inefficiency, and rupture.
Therefore, ignoring this aspect due to time pressure, limited budget, or lack of proper knowledge can lead to serious safety problems and high repair costs.
Below we explain in more detail why the bend radius is important.
Preventing deformation
Attempting to bend an industrial hose beyond its minimum bend radius can lead to permanent deformation of the hose's reinforcement layers.
In turn, when the reinforcement is damaged, the structure of the hose will be weakened. It will become more susceptible to intense bending and vibration during operation, leading to cracks and leaks over time.
Preventing inefficiencies
Industrial installations operate in a system where the pressure is constantly fluctuating due to the transfer of energy needed to do the work. This means that additional stress on the system will require more effort from the system.
And it just so happens that excessive hose flexing can lead to line constriction, which requires the system to work harder. This results in a reduction in its efficiency.
Prevention of breakage
Excessive bending of the hose weakens it. Worse, the resulting narrowing of the flow line can lead to a buildup of pressure that the hose will not be able to withstand. As a result, the risk of rupture increases, which is a serious danger.
Consideration of the bend radius of the hose is therefore essential to ensure the safe, efficient, and durable operation of industrial installations.
What are the types of bend radii?
There are two main types of bend radius - static and dynamic.
Their importance depends on whether the hose will be subjected to continuous movement or mounted in a fixed position.
What is the static bend radius?
Static bend radius is the smallest radius at which a hose can be used without kinking in situations that require it to be constantly bent. This is a key parameter in applications where flexible system components are not exposed to constant movement.
This is because the use of a static bend radius allows for minimizing the risk of damage while ensuring ease of installation.
What is a dynamic bend radius?
The dynamic bend radius is the smallest radius at which a hose can be used without kinking in situations that require it to move continuously.
So if the hose has to withstand constant bending, vibration, or pressure changes, this parameter will help ensure the long-term performance and safety of the installation.
What is the difference between static bend radius and dynamic bend radius?
The main difference between static and dynamic bend radius is that static bend radius refers to hoses in a fixed position, while dynamic refers to hoses subjected to constant movement and vibration.
The static bend radius is usually smaller than the dynamic one because the lack of movement reduces the risk of damage.
Meanwhile, the dynamic bend radius must take into account the additional forces and stresses resulting from continuous bending. Therefore, a larger radius is necessary to ensure the structural integrity of the hose under such conditions.
What factors affect the bend radius of a hose?
Several factors affect the bend radius of a hose. One of the main ones is the design of the hose, that is, how its layers are arranged and how many of them there are. What's more, mesh braided hoses tend to be more flexible than spiral braided hoses with the same number of layers, because the thinner wires in the mesh braid allow for a greater range of movement.
The type of hose material, wall thickness, and diameter also have a significant effect on the bend radius.
Does the bend radius of a hose affect its flexibility?
Yes, the bend radius of a hose affects its flexibility. This is because a lower radius means that the hose can be bent more.
However, flexibility is not just a result of the bend radius. The design of the hose, including the number and type of layers and the type of materials used, also plays a key role here.
Therefore, two hoses of the same thickness may have different minimum bending radii and therefore different levels of flexibility.
How to calculate the bend radius?
To calculate the bend radius, you need to find out what bend angle is required and what is the diameter of the hose.
Once you have this information, you can calculate the minimum bend radius in the two ways mentioned earlier: inner radius and centreline radius. The centreline radius is the most commonly used method, as it allows you to determine the minimum required hose length in any situation.
How to calculate the minimum hose length for a given bend radius?
To calculate the minimum hose length for a given bend radius, it is useful to use the centreline radius method. The formula is as follows:
L = A / 360° × 2πr
- L is the minimum length of hose that must bend,
- A is the angle of bend,
- r is the bend radius of the hose,
- π is the mathematical constant (3.14).
Example of calculation
If a customer needs a hose that can bend 90° and has a bend radius of 3 inches, the minimum hose length would be:
90° / 360° × 2 × 3.14 × 3 = 4.71 inches
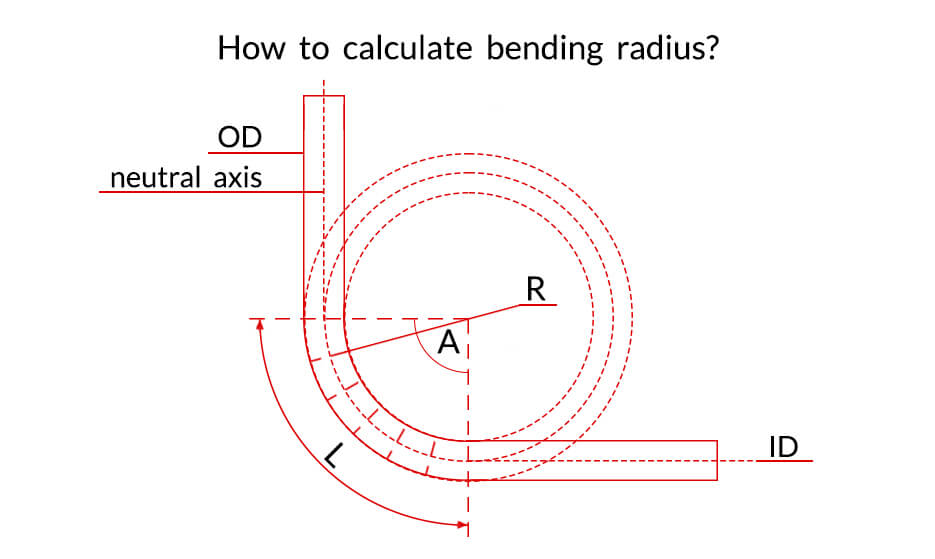
How to choose the right hose bend radius?
To choose the right bend radius, you need to consider several important factors, such as the application, hose type, and design, technical requirements, or hose diameter.
- Hose application - Determine whether the hose will be used in static or dynamic conditions. For dynamic applications where the hose will be subjected to constant movement, choose a larger bend radius.
- Hose type and construction - Mesh braided hoses are usually more flexible than those with spiral braiding. Thus, the design and material of the hose's layers have a direct impact on its bending ability.
- Technical requirements - Make sure the bend radius meets the technical specifications required by the manufacturer and industry standards. This is because the correct bend radius prevents damage and extends the life of the hose.
- Hose diameter - Larger hose diameters usually require larger bending radii. So make sure the radius you choose is appropriate for the diameter of the hose you plan to use.
What is the best hose bend radius?
The best hose bend radius is the one that maximizes hose performance and durability while meeting the specific requirements of the application. Depending on the operating conditions, the best bend radius may vary.
- Static applications - Hoses used in fixed positions can have a smaller bend radius. However, it is recommended that it be slightly larger than the minimum to further increase durability.
- Dynamic applications - Hoses subjected to constant movement, vibration, or pressure changes should have a larger bend radius, as it reduces the risk of damage and ensures long-lasting functionality.
It is always a good idea to consult the hose manufacturer to make sure the bend radius you choose is appropriate for your application.
How to bend industrial hose?
Industrial hose should be bent taking into account several important factors, such as the appropriate bend radius, the type of hose, and the operating conditions. We describe this issue in more detail below.
How to prevent the hose from collapsing when bending?
To prevent the hose from collapsing when bending, use the right bend radius, brackets, and guides, and choose hoses with the right design.
- Applying the right bend radius - Make sure the bend radius is in accordance with the manufacturer's recommendations. Too small a radius can lead to hose collapse.
- Use brackets and guides - Where the hose is most likely to bend, use brackets or guides to help maintain the proper shape of the hose.
- Choosing hoses with the right design - Hoses with spiral braid or helical reinforcement are more resistant to collapse compared to hoses with mesh braid.
How to prevent the hose from bursting when bending?
To prevent the hose from bursting when bending, avoid excessive bending, regularly check the condition of the hose, and select hoses with the right specifications. Here's how you can do this:
- Avoid excessive bending - A bending angle that is too sharp can lead to excessive stress and cracking. So make sure the hose is bent within the recommended bend radius.
- Regular hose inspection - Regular hose inspections can detect early signs of wear or damage that could lead to rupture.
- Select hoses with the right specifications - Make sure the hose is designed for the conditions in which it will be used. When doing so, take into account factors such as pressure, temperature, and the type of medium to be transported.
Following the above tips will help keep industrial hoses in good condition, minimizing the risk of collapse or cracking during bending.
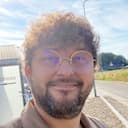
Articles author
Bartosz Kułakowski
CEO of Hosetech Sp. z o.o.
Bartosz Kulakowski is an industrial hoses and couplings specialist with over 10 years of experience. Bartosz has been present in the technical industry since 2013. He gained experience as a technical and commercial advisor in the sector of plastic conveyor belts, steel structures, industrial hoses, and connectors. Since 2016, he has specialized exclusively in hoses and connectors. In 2019 he opened his own business under the HOSETECH Bartosz Kulakowski brand and since July 2022 he has been the CEO of the capital company HOSETECH Sp z o. o. (LLC).
Table of Contents
What is the bend radius?
What is the minimum bend radius?
How to measure the minimum bend radius?
Why is hose bend radius important?
Preventing deformation
Preventing inefficiencies
Prevention of breakage
What are the types of bend radii?
What is the static bend radius?
What is a dynamic bend radius?
What is the difference between static bend radius and dynamic bend radius?
What factors affect the bend radius of a hose?
Does the bend radius of a hose affect its flexibility?
How to calculate the bend radius?
How to calculate the minimum hose length for a given bend radius?
How to choose the right hose bend radius?
What is the best hose bend radius?
How to bend industrial hose?
How to prevent the hose from collapsing when bending?
How to prevent the hose from bursting when bending?
See also other categories