Industrial refrigeration - definition, types, benefits, elements - A complete guide
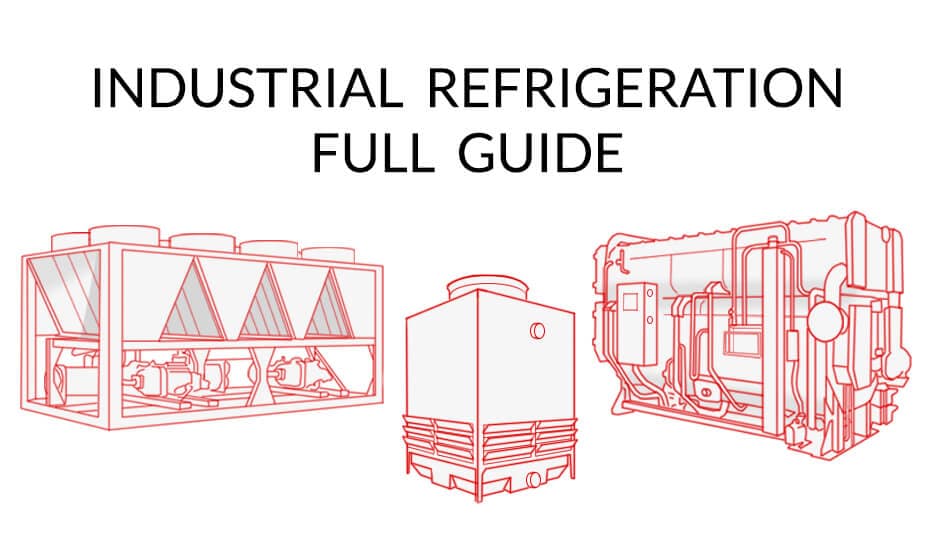
What is industrial refrigeration?
Industrial refrigeration is a specialized field focused on cooling and removing excess unwanted heat from industrial facilities and processes. Excessive heat generated during industrial cycles has a negative impact on equipment, facilities and final products.
When you remove the heat, you ensure continuity safety and process reliability. In doing so, you protect your company's bottom line and prevent costly downtime.
There are three main areas of cooling that industrial refrigeration helps with:
- cooling a specific process, e.g. printing;
- cooling a specific product, e.g. plastic during thermoforming;
- cooling a specific equipment, e.g. a laser cutting machine.
Why is industrial refrigeration important?
Industrial refrigeration is important for the following reasons:
- maintains equipment performance,
- improves product quality,
- creates a safe working environment,
- ensures regulatory compliance,
- reduces energy costs.
Read on and you will learn more about each of the above points.
Maintains equipment performance
Many industrial machines and processes generate heat, which can damage or reduce the performance of equipment. Industrial cooling systems remove excessive heat. Thus, they ensure that equipment runs smoothly and efficiently.
Improves product quality
In some industries, such as the food industry, the product's temperature is crucial to its quality. Cooling systems maintain the desired thermal conditions in the plant, thus ensuring that products meet quality standards.
Creates a safe working environment
High temperatures can sometimes be dangerous for workers, as they increase the risk of heat stress, injury and even death. As industrial cooling systems help to keep the workplace cool and comfortable, they reduce the risk of similar hazards.
Reduces energy costs
Industrial cooling systems reduce energy costs by using more efficient methods to reduce temperatures. However, this largely depends on choosing the right solution for your business and ensuring that the cooling system is in good condition.
Ensures regulatory compliance
Many industries are subject to regulations that limit the amount of heat released into the environment. Industrial cooling systems help to meet these requirements.
In doing so, they protect the environment and the health of nearby communities.
Other reasons why industrial refrigeration is important
In addition to the above, industrial refrigeration improves productivity, reduces downtime and increases profits. Moreover, by providing a cool and comfortable working environment, it helps employees to be more productive.
What are the types of industrial refrigeration?
There are three main types of industrial refrigeration - dry cooling, evaporative cooling, compressor cooling (chiller).
What is dry cooling?
Dry cooling is the refrigeration type that uses dry coolers, or fans, to direct ambient air through coolant hoses. This reduces its temperature.
The system is used where the necessary process temperature is higher than the ambient air temperature. Only a few degrees of difference is needed.
A great advantage of dry cooling is that it does not need a constant supply of water or a treatment plant. In addition, the cost of maintenance is considerably low.
However, there are also some downsides.
First of all, the lowest achievable cooling temperature cannot be lower than the ambient temperature (unless you use additional improvement solutions). In addition, the fans consume a relatively high amount of electricity and the dry cooler itself needs a sufficiently large space to exchange heat via air.
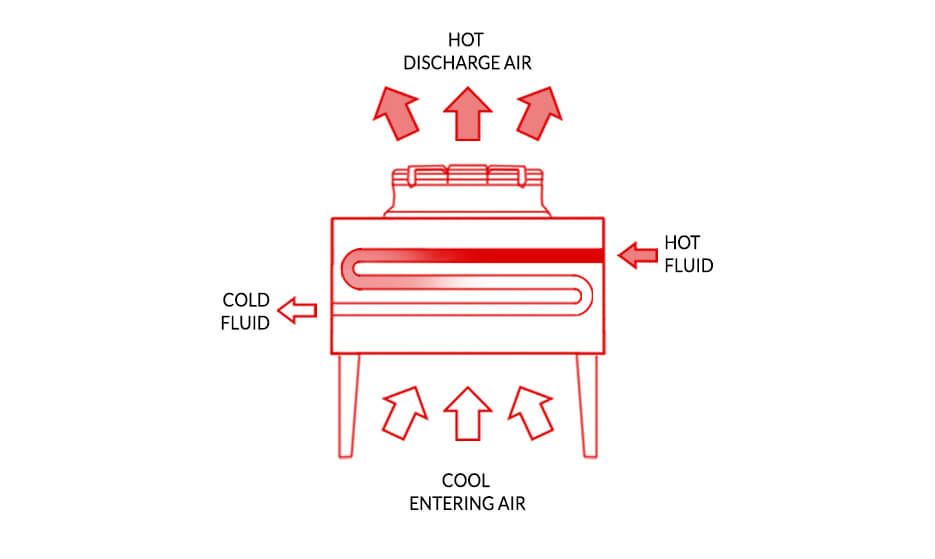
What is evaporative cooling?
Evaporative cooling is a type of refrigeration that uses the latent heat of evaporation of water to reduce the temperature of a liquid or gas.
At a relative humidity of less than 100%, the water evaporates, absorbing an amount of heat known as the latent heat of vaporisation. In doing so, it cools the remaining liquid or gas. The lower the relative humidity, the more efficient this process will be.
You can calculate the relative humidity from the difference between the wet and dry thermometer temperatures. Standard thermodynamic diagrams will suffice.
On dry summer days, when the dry thermometer temperature is above 25 degrees Celsius, the liquid can be cooled to around 21 degrees Celsius.
Evaporative cooling provides better heat transfer compared to a dry cooler. In addition, it consumes less electricity.
In terms of downsides, you have to add the cost of water to the installation. This consists of the treatment station and the replenishment of liquid losses.
Before we go any further, we will look at three more types of cooling towers that are possible with an evaporative cooling system. It is about:
- open cooling towers,
- closed cooling towers,
- hybrid cooling towers.
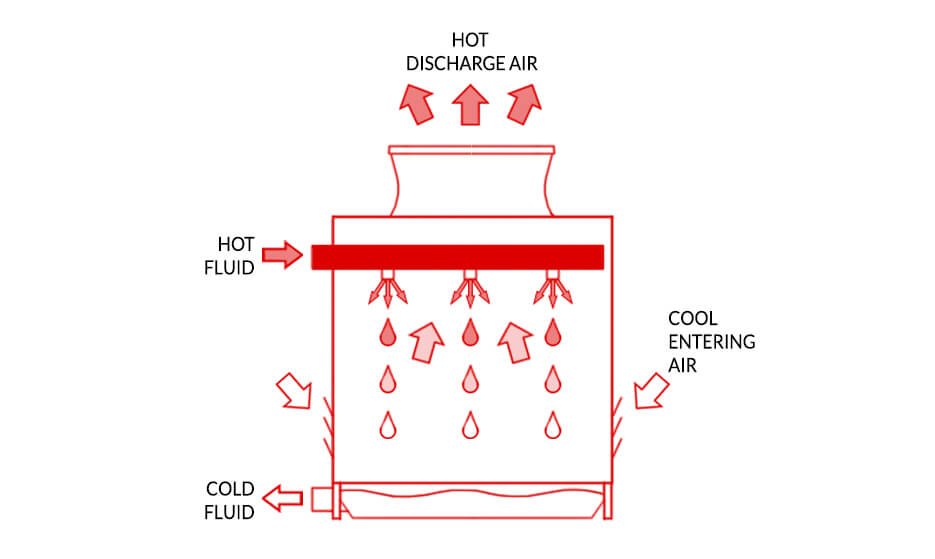
How does open cooling tower works?
The open cooling tower works in a simple way.
Water that needs to be cooled is sprayed at the top of the cooling tower. As it falls against gravity, it comes into contact with the air drawn upwards by the fan. As a result, the water partially evaporates, absorbing heat from the remaining droplets.
Already cooled, it accumulates in a water tank under the cooling tower. From there, it returns to the process.
How does clsoed cooling tower works?
A closed cooling tower works on a similar basis to an evaporative condenser. The only difference is that instead of refrigerant, the refrigeration coil contains plain water.
How does hybrid cooling tower works?
The hybrid cooling tower can operate in three different modes depending on the external conditions:
- dry (like a dry cooler)
- adiabatic (like a closed cooling tower)
- dry-wet (a combination that provides maximum cooling capacity).
Due to the high initial price of the installation (approximately five times higher than that of an open cooling tower), hybrid cooling towers only become interesting when the price of water is really high. They are most often used where vapour reduction is required.
What is more, with this technology, the emphasis is on saving water rather than energy.
What is compressor cooling?
Compressor cooling is a refrigeration type that is based on the principle of thermodynamics, which states that the boiling point of a liquid decreases as the ambient pressure decreases. Therefore, compression and expansion allows the liquid refrigerant to evaporate at a low temperature and condense at a higher temperature. At a low temperature, heat will be absorbed from the fluid to be cooled. On the other hand, at high temperature it will be emitted into the environment.
Compressor cooling is used in a wide range of applications, from domestic refrigerators to large industrial refrigeration systems. It uses a refrigerant with a boiling point lower than that of water.
There are three main types of industrial chillers:
- water-cooled,
- air-cooled,
- with an evaporative condenser.
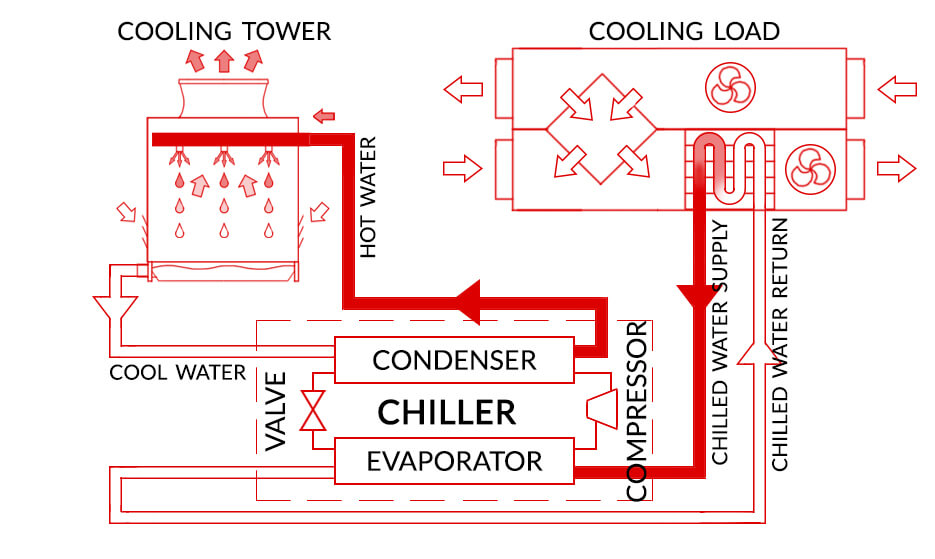
How does water-cooled chiller work?
A water-cooled chiller uses an external cooling tower to supply water, which takes the temperature away from the refrigerant in gaseous form in the condenser. Once the heat is removed, the refrigerant transforms back into a liquid and starts the cycle all over again.
In general, water-cooled chillers offer greater efficiency compared to air-cooled systems. They are flexible and scalable (suitable for both large size and small cooling requirements). Premises with limited space can also benefit from portable water-cooled chillers.
Another advantage is their relatively quiet operation compared to other systems.
On the other hand, water-cooled chillers are more expensive both to install and to maintain. In some areas, the constant need for water can also be a problem.
Constant maintenance is also required to prevent failures due to the build-up of mineral deposits from continuous water circulation.
How does air-cooled chiller work?
The air-cooled chiller uses ambient air to remove heat from the refrigerant in the condenser using fans. This is the main difference between them and the water-cooled version.
The heat dissipated can be significant at the chiller site.
The initial cost of installing the system is usually lower than its water-cooled counterpart. This is because it does not require components such as a cooling tower and water pump. For the same reason, an air-cooled chiller is also cheaper to maintain.
It works well where space is limited and is available in portable versions.
Furthermore, in some configurations, the heat ejected from the chiller is used to heat the interior of the building during the cold months. This increases savings.
However, air-cooled chiller systems tend to be more energy intensive due to the need to power the fan. They also tend to be noisier, which is a problem in certain types of interiors.
In addition, their overall lifespan can be slightly lower compared to water-cooled versions.
How does chiller with evaporative condenser works?
The evaporative condenser chiller offers an alternative method of achieving the same result. An evaporative condenser takes the place of the cooling tower from the water-cooled system. It is in a sense a hybrid system - something between water and air cooling.
The refrigerant in this configuration is transformed from a vapour to a cooled liquid by evaporating water, which is sprayed onto the external surface of the pipes. The elimination of the cooling tower reduces the number of steps in the cycle from two to one (water does not have to flow into the tower).
Evaporative condensers have the advantage over air-cooled chillers that they can operate at lower fan speeds, saving energy. They also have fewer components, so installation and maintenance costs are lower compared to the water-cooled version.
The evaporative condenser chiller is also relatively small, which is an advantage when space is limited.
The downside is that the system works most effectively in hot and dry climates. Therefore, it may not be a suitable solution in colder northern regions.
What is the principle behind industrial refrigeration?
The principle of industrial refrigeration is to transfer heat from a hot object to a cooler object. This can be done in a number of ways, but the most popular methods are:
- evaporative cooling,
- forced-air cooling,
- liquid cooling.
The type of industrial cooling system used depends on the specific application. For example, you will often encounter evaporative cooling in cooling towers, as it is a relatively inexpensive and efficient way of reducing the temperature of large volumes of water.
Forced-air cooling often appears in industrial fans and air conditioners, as it offers a relatively simple and efficient way to cool small and medium-sized facilities.
Liquid cooling, on the other hand, is most commonly used in industrial machinery. This is because it is very efficient at cooling high-temperature objects.
No matter what type of industrial cooling system you use, the principle is always the same: transferring heat from a hot object to a cooler object. In this way, you protect equipment, workers, products and the environment.
You also save energy and money because you increase productivity and reduce downtime.
What are the main components of an industrial refrigeration system?
The main components of an industrial refrigeration system are:
- heat exchangers,
- compressors,
- condensers,
- evaporators,
- pumps,
- fans,
- control systems.
Read on and you will find out more about them.
What are heat exchangers?
Heat exchangers transfer heat from one fluid to another. They are at the heart of most industrial cooling systems and come in a variety of types, including as:
- shell and tube heat exchanger,
- plate heat exchanger,
- evaporative condenser.
What is the compressor in industrial refrigeration?
The compressor is an element located between the condenser and evaporator. It takes heated, low-pressure refrigerant vapour from the evaporator, compresses it to increase pressure and pumps it to the condenser.
There are various compressors used in refrigeration systems, including the following:
- piston,
- scroll,
- rotary-screw.
What is a condenser?
The condenser is one of two types of heat exchanger used in the primary refrigeration loop. Hot refrigerant vapour at high pressure enters the unit where it releases heat by flowing through a coil. The condenser is also connected to a fan or water supply that takes away the high temperature.
As a result, the refrigerant condenses back to a liquid state.
What are expansion devices?
An expansion device is an element that creates a pressure drop when the refrigerant leaves the condenser. This causes some of the refrigerant to boil quickly, forming a two-phase mixture.
The rapid change in pressure allows the next piece of equipment in the circuit, the evaporator, to perform its intended function.
What are evaporators?
The evaporator is the second heat exchanger in the standard refrigeration circuit. As with the condenser, its name comes from the primary function of the unit.
The evaporator completes the refrigeration cycle as it absorbs heat.
It is located between the expansion valve and the compressor, and its function is to collect unwanted heat from the building and transfer it to the refrigerant so that it can be rejected.
The refrigerant then goes back to the compressor, where the process starts again.
What are pumps used for in the industrial refrigeration?
Pumps are responsible for the circulation of fluids. They are used in most industrial cooling systems to circulate the refrigerant in the circuit.
What are fans used for in the industrial refrigeration?
Fans force the circulation of air. In some cooling systems, they are responsible for heat exchange in the condenser or evaporator.
What are control systems used for in the industrial refrigeration?
Control systems control the operation of an industrial refrigeration system. They usually contain sensors that monitor the temperature of the object being cooled and the refrigerant. Based on the collected data, they try to maintain the desired process temperature.
Control systems can be simple or complex depending on the specific application.
Which factors to consider when designing an industrial refrigeration system?
Consider the following factors when designing an industrial refrigeration system:
- heat load,
- environmental factors,
- energy efficiency,
- scalability,
- maintenance and safety.
Below we explain why they are so important.
What is the heat load?
The heat load is the amount of energy that needs to be removed to cool the process to the desired temperature.
The first step in selecting an industrial cooling system is to calculate the heat load. One method involves measuring the temperature and flow rate of the fluid to be cooled.
Which environmental factors to consider when designing an industrial refrigeration system?
Consider the following environmental factors when designing an industrial refrigeration system - ambient temperature, humidity and wind speed affect the performance of the cooling system.
For example: an evaporative condenser chiller works best in a hot, dry climate. Its efficiency will decrease in cold, humid environmental conditions.
What is the energy efficiency of the cooling system?
The energy efficiency of the cooling system decides how much energy is efficiently used by the cooling system. The more efficient your cooling system is, the less energy it will use, meaning you will save money on your electricity bills.
There are many factors that affect the efficiency of a cooling system, including:
- refrigerant type,
- system design,
- operation and maintenance.
What is the scalability of the cooling system?
The scalability of the cooling system is a factor that allows you to expand the cooling system in the future. This means that you should be able to easily expand the installation to meet any increased requirements.
Some cooling systems are designed with scalability in mind, while others are not.
Maintenance and safety in cooling systems
Also pay attention to the maintenance requirements and safety features of the cooling system. Choose an installation that is relatively easy to maintain and has safety features that will protect workers and equipment from hazards.
As a general rule, water-cooled chillers are more difficult to maintain, but have the advantage of offering greater efficiency.
What are the advantages of an efficient industrial refrigeration system?
The biggest advantages of an efficient industrial refrigeration system are:
- increased productivity,
- extended equipment life,
- energy savings.
Increased productivity
An efficient cooling system reduces downtime. Thus, it prevents overheating and equipment failure, which increases the overall productivity and profitability of the production process.
Furthermore, a stable low temperature increases the quality of the final product as it protects it from heat damage. This also translates into greater customer satisfaction.
And finally, comfortable working conditions promote greater productivity for the people you employ. When they are not bothered by high temperatures, they can concentrate better on their duties.
Extended equipment life
As an efficient cooling system prevents machines from overheating, it protects equipment from damage. In this way, it extends its service life and makes you save money on repairs.
What's more, the machinery fleet won't require as much maintenance downtime, which in the long term will translate into increased profits.
Energy savings
When the cooling system works efficiently, it uses less energy. As a result, you will receive lower electricity bills at the end of the month.
In addition, efficient cooling produces fewer pollutants, so it is greener and contributes to better air quality. It will also make it easier for you to comply with environmental regulations.
Where is industrial refrigeration used?
The most significant industries where industrial refrigeration is used are:
- production plants,
- data centres,
- electricity plants,
- food processing industry.
Industrial refrigeration in production plants
Refrigeration systems are used in many production plants. One of the most popular examples is plastics processing. By properly cooling the injection moulds (and other components), the plastic does not melt. As a result, the quality of the final product is higher.
Another example is chemical plants. Thanks to cooling systems, chemicals do not overheat, which gives better control over the reactions taking place.
Metalworking is also worth mentioning. Adequate cooling ensures that the machines do not overheat, which increases the precision of the work (e.g. when cutting metal).
Industrial refrigeration in data centres
industrial refrigeration systems are used in data centres to cool down servers. Computer servers process a lot of information every day, which forces them to work hard. A side effect of their activity is heat, which has to be dissipated. Otherwise, the servers would overheat, which could lead to failure.
Industrial refrigeration in electricity plants
Electricity plants, such as power stations and oil and gas installations, use industrial refrigeration to cool equipment and processes.
For example: in power plants, cooling systems are used to remove heat from turbines and other equipment. In this way, they prevent the equipment from overheating and allow it to operate more efficiently.
Industrial refrigeration in food processing industry
Food processing is the main industry that uses refrigeration systems to cool products, for example during storage. This allows food to spoil more slowly and retain quality for longer. It can also be frozen and thus protected for a longer period of time.
In addition, industrial refrigeration is used to cool equipment in food processing plants. This ensures that machines do not overheat and work more efficiently.
What are the latest trends in industrial refrigeration?
The latest trends in industrial refrigeration include:
- intelligent cooling systems,
- ecological cooling options,
- integration with IoT and automation.
Below, we describe them in more detail.
Intelligent cooling systems
Smart cooling systems connect to Wi-Fi and allow users to automatically contact the control panel. This allows them to adjust the temperature to suit their current needs, even if they are outside the building.
The solution is slowly entering the mainstream with the increasing need to maintain energy efficiency. With advanced technology, facility managers will make real-time adjustments, contributing to overall energy savings and a sustainable future.
Ecological cooling options
Ecological cooling options use renewable energy sources and work in zoned systems.
Outdated HVAC systems are unable to deliver the expected performance. In addition, they contribute to excessive energy consumption, which has a negative impact on the environment.
Users also feel the pressure of high electricity costs.
Therefore, the industry is increasingly looking for innovative and energy-efficient solutions. Here are some of the eco-friendly innovations that are gaining popularity:
- Zoned systems that heat or cool specific rooms when needed. This solution significantly increases energy savings in buildings.
- Industrial refrigeration powered by gas and solar energy. Is a much cheaper option than electricity from fossil fuels or coal.
- Geothermal heating and cooling. Are safe, quiet and up to 65% more efficient than traditional HVAC systems. They use the earth's natural thermal energy for heating and air conditioning, and are therefore sustainable and efficient.
Installing these types of systems can be future-proof for companies.
Integration with IoT and refrigeration system automation
Technology plays an important role in the HVAC industry. Recently, the Internet of Things (IoT) has been gaining a lot of publicity and is finally becoming a reality in industrial refrigeration too!
IoT is much more intelligent and easily accessible to users. HVAC producers apply this technology by embedding sensors and other devices into heating and cooling systems. In this way, they monitor and collect data on the performance and status of the cooling system in buildings.
This means that buildings with different systems can communicate with each other. As a result, they are able to:
- improve efficiency,
- increase comfort,
- provide real-time monitoring of systems, perform predictive,
- maintenance on HVAC systems.
At the same time, they manage and control the temperature and humidity levels.
What's more, thanks to the installation of smart meters, thermostats and sensors, managers gain a higher level of control over the operation of the building. They collect data and compile it into reports that help identify usage trends, system status, and past performance.
The data can be further used to inform preventive maintenance and detect sources of failure for faster repair.
Modern HVAC systems self-diagnose faults. As a result, technicians remove them faster, which minimizes equipment downtime.
FAQ
What is the purpose of industrial refrigeration?
The purpose of industrial refrigeration is to remove heat from industrial equipment and processes. This is necessary for many reasons, such as: to prevent overheating and equipment failure, to maintain a safe working environment for workers, to protect the product from breakdown or degradation or to reduce the cost of energy.
How often should industrial refrigeration systems be maintained?
The maintenance frequency of industrial cooling systems varies depending on the specific installation and the environment in which it operates. However, most systems should be inspected and maintained at least once a year. This will ensure that the system is operating efficiently and is not at risk of failure.
Can industrial refrigeration systems be integrated with renewable energy sources?
Yes, industrial refrigeration systems can be integrated with renewable energy sources, such as solar and wind energy, for example. This will reduce the overall energy consumption of the system and lower the carbon footprint of the facility.
What is the average service life of an industrial cooling system?
The average service life of an industrial cooling system is typically 15 years. However, in reality it will vary depending on the quality of the system, the operating environment and the level of maintenance.
Summary
Industrial refrigeration is an integral part of many industrial processes. By removing heat from equipment and operations, it helps prevent equipment failure, protect workers and improve product quality.
If you are considering an industrial refrigeration system for your facility, consult a qualified engineer. This will help you determine the best solution for your needs.
With proper planning and installation, an industrial cooling system will give you many years of reliable operation. It will also contribute to keeping your plant running smoothly and efficiently.
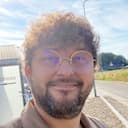
Articles author
Bartosz Kułakowski
CEO of Hosetech Sp. z o.o.
Bartosz Kulakowski is an industrial hoses and couplings specialist with over 10 years of experience. Bartosz has been present in the technical industry since 2013. He gained experience as a technical and commercial advisor in the sector of plastic conveyor belts, steel structures, industrial hoses, and connectors. Since 2016, he has specialized exclusively in hoses and connectors. In 2019 he opened his own business under the HOSETECH Bartosz Kulakowski brand and since July 2022 he has been the CEO of the capital company HOSETECH Sp z o. o. (LLC).
Table of Contents
What is industrial refrigeration?
Why is industrial refrigeration important?
Maintains equipment performance
Improves product quality
Creates a safe working environment
Reduces energy costs
Ensures regulatory compliance
Other reasons why industrial refrigeration is important
What are the types of industrial refrigeration?
What is dry cooling?
What is evaporative cooling?
What is compressor cooling?
What is the principle behind industrial refrigeration?
What are the main components of an industrial refrigeration system?
What are heat exchangers?
What is the compressor in industrial refrigeration?
What is a condenser?
What are expansion devices?
What are evaporators?
What are pumps used for in the industrial refrigeration?
What are fans used for in the industrial refrigeration?
What are control systems used for in the industrial refrigeration?
Which factors to consider when designing an industrial refrigeration system?
What is the heat load?
What is the energy efficiency of the cooling system?
What is the scalability of the cooling system?
Maintenance and safety in cooling systems
What are the advantages of an efficient industrial refrigeration system?
Increased productivity
Extended equipment life
Energy savings
Where is industrial refrigeration used?
Industrial refrigeration in production plants
Industrial refrigeration in data centres
Industrial refrigeration in electricity plants
Industrial refrigeration in food processing industry
What are the latest trends in industrial refrigeration?
Intelligent cooling systems
Ecological cooling options
Integration with IoT and refrigeration system automation
FAQ
What is the purpose of industrial refrigeration?
How often should industrial refrigeration systems be maintained?
Can industrial refrigeration systems be integrated with renewable energy sources?
What is the average service life of an industrial cooling system?
Summary
See also other categories