Sand for sandblasting - How to choose an abrasive for a sandblaster?
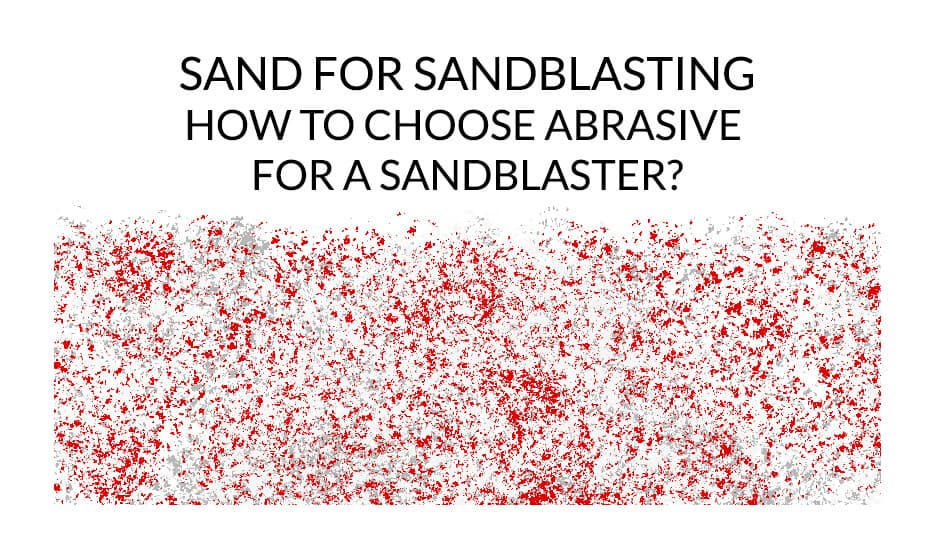
What is sandblasting sand?
Sandblasting sand is an abrasive used in the sandblasting process, which is a method of cleaning, smoothing or making various surfaces rough by pressing an abrasive (in this case sand) firmly onto a given surface. The process is carried out using compressed air, water or steam.
Why is it important to choose the right abrasive for your sandblaster?
The choice of abrasive for your sandblaster is important as it impacts the finish quality, efficiency of operation and safety.
Below we explain each point in more detail.
Efficiency of operation
Different abrasives have different abrasive properties, which translate into their effectiveness for specific applications. Heavier abrasives (e.g. grit) are better for removing hard coatings of material, while lighter abrasives (e.g. nut shells) are ideal for cleaning softer surfaces without the risk of damaging them.
Durability and costs
Some abrasives (e.g. garnet) can be used more than once. In contrast, others are disposable. For this reason, the choice of an abrasive with a suitable service life can make a significant difference to the overall expenditure associated with a sandblasting operation.
Safety
Some abrasives, especially those containing silica, can pose serious health risks in the form of respiratory diseases. Using some safer alternatives, such as glass or garnet abrasives, can minimise this risk.
Environmental protection
Some abrasives are harmful to the environment (e.g. those containing heavy metals can contaminate soil and water). It is therefore worth considering organic or recycled materials that will reduce the negative impact of sandblasting on nature.
Finish quality
Different abrasives produce different finishing effects. Finer and softer abrasives can smooth the surface, while coarser and harder abrasives are better for a rough texture.
Regulatory compliance
Due to health and environmental issues, some countries and industries have strict regulations on the types of abrasives that can be used. Therefore, make sure that the abrasive you choose meets the relevant requirements.
What are the types of abrasive for sandblaster?
The most popular types of abrasive for the sandblasters are:
- quartz sand,
- corundum and electrocorundum,
- copper slag,
- garnet,
- grit,
- baking soda,
- glass shards,
- aluminium oxide (diglinium trioxide),
- plastic abrasive,
- silicon carbide,
- pumice,
- ground maize cobs,
- nut shells.
Below you can find the characteristics of each of these.
What is quartz sand?
Quartz sand is the most commonly used abrasive. This is largely due to the fact that it is characterized by the lowest cost while providing a very good end result.
Additionally, it is available in various granulations, making it suitable for both the renovation of monuments and the sandblasting of rims, chassis, or car bodies. It can also handle strong corrosion on steel components. For quartz sand, we recommend selecting sandblasting hoses that are highly abrasion-resistant.
What is corundum and electrocorundum?
Corundum and its synthetic version electrocorundum are popular abrasives.They are used in the manufacture of abrasive papers and grinding wheels.
They are also considered a slightly more effective abrasive compared to the sand described above.
They are most often used in cleaning rust from steel structures, removing dirt from bricks, sandblasting wood and working with glass.
What is copper slag?
Copper slag is a type of abrasive that is primarily used in abrasive blasting. Because it is less durable and less expensive than aluminium oxides, it is excellent for outdoor work, such as cleaning large metal surfaces (e.g., bridges, ships, containers) using the abrasive blasting method.
In addition to its low cost, its advantages include lower consumption compared to sand and no risk of the abrasive settling on the processed surface.
What is garnet sand?
Garnet sand is a popular abrasive for sandblasting due to its effectiveness and environmental friendliness.
It is characterised by sharp edges that ensure effective cleaning and surface profiling. It is also durable, allowing for multiple uses, thereby reducing operating costs.
In addition, garnet is safer for health than sands containing silica. It also remains environmentally friendly as it contains no toxic metals.
What is grit as an abrasive?
Steel or cast iron grit is a specific abrasive. Due to its hardness and sharpness, it is very effective in removing external coatings from various materials.
It is most commonly used for cleaning, as well as strengthening and refining steel structures. However, there is a growing popularity of grit blasting services for brick or concrete as well. Shotblasting hoses are also abrasion resistant to withstand the entire process.
The abrasive creates a characteristic effect of a very rough surface structure.
It is worth noting, however, that grit is also available in fine pellet form. They are noticeably less invasive than crushed grit.
What is baking soda as an abrasive?
Baking soda (sodium bicarbonate) is an abrasive , that stands out for its high effectiveness with very little interference with the structure of the material being treated.
Baking soda is the least invasive cleaning method and is therefore most often used when working with delicate surfaces so as not to damage them.
It is great for removing old varnish from sheet metal. In addition, soda is also a natural rust inhibitor, so it will be suitable for fighting corrosion. It also has anti-fungal properties, which will be useful for cleaning facades.
However, for sodding to have the best effect, it should be carried out with a water sandblaster.
What are glass shards as an abrasive?
Glass particles are another popular abrasive. As an aggressive raw material with relatively sharp edges, it shows a high degree of effectiveness in cleaning surfaces - even very rough and irregularly shaped ones.
The use of glass particles as an abrasive will result in a smooth texture of the material to be treated. For this reason, this method is most often used for renovation work and when a deep cleaning of the surface is required.
As with grit, glass is available in crushed and spherical form. The latter version is less invasive and has greater recycling potential.
What is aluminium oxide (diglinium trioxide)?
Aluminium oxide is a hard and durable abrasive. It is often used for the surface treatment of metals (e.g. stainless steel) due to its ability to remove thick coatings and rust without affecting the underlying material.
Aluminium oxide is also effective in precision grinding and can be used to machine glass and ceramics.
What is plastic abrasive?
Plastic abrasives are used in more delicate applications where it is necessary to avoid damaging the surface. They are ideal for cleaning aluminium, plastic or fibreglass.
As plastic abrasives are less aggressive than their metal or mineral alternatives, they allow greater control of the cleaning process while providing effective removal of dirt and paint.
What is silicon carbide?
Silicon carbide is an extremely hard abrasive, often used for sandblasting metal, stone and glass. Its sharp edges provide exceptional effectiveness in quickly removing the outer coating of a given surface.
Silicon carbide is also used in micro-sanding for fine machining of delicate components and for cleaning very hard materials.
What is pumice as an abrasive?
Pumice is a natural mineral that has a volcanic form with a porous structure. Due to its brittleness, it mainly serves as an abrasive for delicate materials.
In addition, pumice is moderately hard, which makes it not very aggressive and therefore ideal for working with glass, stone, etc. It is suitable for most operations where protection of the material surface is very important.
What are ground maize cobs as an abrasive?
Ground maize cobs are an environmentally friendly abrasive, often used for gentle cleaning or polishing. It is an excellent choice when you need to remove paint from delicate surfaces or clean a sensitive electronic component.
The soft nature of the cobs makes them less aggressive than traditional abrasives, minimising the risk of damage to the surface being worked on.
What are nut shells as an abrasive?
Nut shells are another environmentally friendly abrasive, ideal for delicate applications. They are often used when cleaning surfaces that can be easily damaged, such as wood or plastic.
This abrasive is biodegradable and contains no harmful substances, making it a suitable choice for areas that require eco-friendly solutions.
Which sand to choose for sandblasting?
What sand to choose for sandblasting depends on the specifics of the treatment in question and the hardness of the material you will be working with.
Above all, follow one simple rule: the abrasive should never be harder than the material to be sandblasted. Otherwise, damage and abrasions may appear on the surface to be cleaned.
Also pay attention to the basic parameters of the abrasive. These are:
- granulation - describes the grain size distribution of the ground material and has a significant impact on the abrasive process;
- fraction - refers to the characteristic grain size which is constant for a given abrasive;
- moisture content - mainly applies to silica sand and determines the water content of the raw material (should be no more than 0.2% by weight of the product).
In addition to the above, you can also consider the profile of the abrasive's surface when choosing an abrasive. Angular or sharp grits show much greater effectiveness in cleaning the material, but are also more intrusive. On the other hand, spherical and smoother abrasives have less friction but are more delicate.
The surface profile, together with the hardness of the abrasive, directly influences the effectiveness and speed of peeling off the outer layers from the material being treated.
Finally, it is worth noting that some abrasives are recyclable. In this respect, grit, garnet and silicon carbide perform best, followed closely by quartz sand and glass beads.
Where to buy sand for sandblasting?
You can buy sand for sandblasting from aggregate distributors as well as from builders' or even garden shops. Most of them also sell their products online, so you can easily order the right raw material online.
Many people believe that the best quality abrasives are available from distributors. Although this may indeed be the case in some cases, it is not the rule.
Therefore, when choosing a raw material, read its description and pay particular attention to the parameters we wrote about above.
How much does sand for sandblasting cost?
Sand for sandblasting costs around £100 per 100 kg (you will also find cheaper offers), making it the least expensive type of abrasive on the market. You can also buy corundum at a very similar price.
As for glass, on the other hand, it is about 3 times more expensive, and you will pay up to 10 times more for grit and aluminium oxide.
As you can see, the price of an abrasive depends mainly on its type. However, the good news is that the cheapest sand in this respect is completely sufficient for most applications (even professional ones).
How much sand is needed for sandblasting?
For sandblasting, approximately 5-7 kg of sand per square meter of surface is required. This represents the average consumption of abrasive. However, keep in mind that these are general guidelines, so the actual demand may vary.
This is because the necessary amount of sand for sandblasting depends on several key factors, such as:
- Size and type of the processed surface - Larger or more complex surfaces will require more sand. For example, sandblasting an entire car will involve a greater need for abrasive compared to sandblasting a small component.
- Type of abrasive – Some abrasives are more efficient than others. For example, garnet can be reused, reducing the overall amount of abrasive needed.
- Desired finishing effect – Coarser abrasives may remove surface layers more quickly, but they may also require more material to achieve a uniform finish.
- Sandblasting equipment – The type of sandblaster used and its settings (e.g., pressure) also influence the rate of abrasive consumption.
- Sandblasting technique – The experience and technique of the operator also affect the efficiency of sand consumption. Less experienced workers may use more material.
For a more accurate assessment of abrasive requirements, it's advisable to consult with a raw material supplier or a sandblasting specialist who can provide more precise estimates based on the specific project.
What should be done with the sand after sandblasting?
Sand after sandblasting should either be disposed of properly or treated for re-use. In both cases, you should always consider safety issues and applicable regulations.
Here are some things to consider:
- Sand recovery and cleaning - In some cases (especially if you are using more expensive abrasives) it is possible to recover and clean them for reuse. However, this requires specialised screening and removal equipment.
- Abrasive disposal - Sand and other used abrasives can contain contaminants such as paint, oils, heavy metals and even toxic materials (depends on the surface being treated). For this reason, they cannot simply be discarded or reused in other applications. It is best to contact your local authorities or industrial waste disposal companies to find out about suitable disposal methods and locations.
- Regulatory compliance - The disposal of used sand and other abrasives may be subject to local regulations for the disposal of industrial waste. You should comply with these to avoid penalties and handle waste responsibly.
- Environmental protection - Make sure that the abrasive does not enter water systems, soil or other areas where it could adversely affect the environment.
- Safety - Use appropriate protective equipment when cleaning and disposing of the abrasive to avoid exposure to potentially harmful substances.
FAQ
Which sand for sanding alloy wheels?
For the sandblasting of alloy wheels, quartz sand is more than sufficient. More expensive abrasives (e.g. glass dust or grit) may produce a slightly better result, but are not necessary for effective work.
Which sand for sandblasting steel wheels?
Medium or fine quartz sand is suitable for sandblasting steel wheels. For an even better result, you can go for slightly more expensive abrasives such as glass dust, alumina or grit.
Which sand for a siphon sandblaster?
For a siphon sandblaster, choose either universal quartz sand or any other aggregate you wish to use. The type of sandblaster rarely determines which abrasive you should use.
For sandblasting wood, either quartz sand, baking soda or glass beads are best. Baking soda and glass perform slightly better here as they do less damage to the structure of the wood.
What sand is suitable for wet sandblasting?
For wet sandblasting, abrasives that do not dissolve in water are best, such as garnet, glass beads, or specially prepared sand for wet sandblasting.
How much sand per m2 of sandblasting?
On average, 5-7 kg of sand is needed per square meter for sandblasting, but the requirement may vary depending on the type of abrasive and sandblasting technique.
What's better for sandblasting: sand or corundum?
Corundum is usually a better choice for sandblasting than traditional sand, due to its efficiency, safety, and finish quality. However, the choice of the appropriate abrasive should always be tailored to the specific project, its requirements, and available resources.
What sandblasting sand thickness?
The choice of sandblasting sand thickness depends on the task. Coarser grains are better for heavy-duty tasks, such as rust removal, while finer grains are used for more delicate applications.
How much does corundum for sandblasting cost?
The cost of corundum for sandblasting depends on the chosen supplier and the quantity ordered (bulk quantities are usually cheaper). However, this type of abrasive is generally more expensive than traditional sand. You can check current prices with local sellers.
Can baking soda be used for the sandblaster?
Yes, baking soda can be used for sandblaster. Soda is a gentle abrasive and can be used in sandblaster - especially for delicate surfaces or where easy removal is required.
Is regular sand suitable for sandblasting?
Regular sand is suitable for sandblasting, but has been banned in most countries due to the high health risk (lung silicosis) that arises from the high free silica content.
How much sand is needed for sandblasting?
The amount of sand needed for sandblasting depends on the project, but averages 5-7 kg/m2.
Which grit size for sandblasting?
Which grit for sandblasting is needed depends on the project. Finer grit sizes are better for delicate tasks, while coarser grains are better for more demanding work.
What sand for stone sandblasting?
For stone sandblasting, the best choices are garnet sand, corundum, or glass. For harder types of stone, silicon carbide is also worth considering. For more delicate work, synthetic material or soda ash can be suitable.
What is the best sand for metal sandblasting?
The best sand for metal sandblasting is garnet sand, silicon carbide, or corundum. Each one is effective in removing rust and paint.
Is it possible to sandblast with wet sand?
Yes, you can sandblast with wet sand. This is what the wet sandblasting process is all about, reducing dust emissions.
Can I use sugar for sandblasting?
No, you cannot use sugar for sandblasting. Sugar is not a suitable abrasive due to its softness and stickiness.
Can salt be used for sandblasting?
Salt cannot be used for sandblasting as it can cause corrosion and is not effective as an abrasive.
What is the best sandblasting agent for severe rust?
In the case of severe rust, the best sandblasting agent will be corundum or silicon carbide, which are very effective at removing tough contaminants.
What is the most aggressive sandblasting agent?
The most aggressive sandblasting agent is silicon carbide and some types of corundum. These are very hard and effective at removing heavy contaminants.
What is the best sand for sandblasting?
Which sand is best for sandblasting depends primarily on the type of surface to be treated and the required finishing effect. A grittier and harder abrasive will be better suited to treating hard materials and removing thick coatings (such as paint or rust). By contrast, less aggressive and softer abrasives will work well for softer surfaces when a gentle cleaning effect is required.
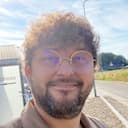
Articles author
Bartosz Kułakowski
CEO of Hosetech Sp. z o.o.
Bartosz Kulakowski is an industrial hoses and couplings specialist with over 10 years of experience. Bartosz has been present in the technical industry since 2013. He gained experience as a technical and commercial advisor in the sector of plastic conveyor belts, steel structures, industrial hoses, and connectors. Since 2016, he has specialized exclusively in hoses and connectors. In 2019 he opened his own business under the HOSETECH Bartosz Kulakowski brand and since July 2022 he has been the CEO of the capital company HOSETECH Sp z o. o. (LLC).
Table of Contents
What is sandblasting sand?
Why is it important to choose the right abrasive for your sandblaster?
Efficiency of operation
Durability and costs
Safety
Environmental protection
Finish quality
Regulatory compliance
What are the types of abrasive for sandblaster?
What is quartz sand?
What is corundum and electrocorundum?
What is copper slag?
What is garnet sand?
What is grit as an abrasive?
What is baking soda as an abrasive?
What are glass shards as an abrasive?
What is aluminium oxide (diglinium trioxide)?
What is plastic abrasive?
What is silicon carbide?
What is pumice as an abrasive?
What are ground maize cobs as an abrasive?
What are nut shells as an abrasive?
Which sand to choose for sandblasting?
Where to buy sand for sandblasting?
How much does sand for sandblasting cost?
How much sand is needed for sandblasting?
What should be done with the sand after sandblasting?
FAQ
Which sand for sanding alloy wheels?
Which sand for sandblasting steel wheels?
Which sand for a siphon sandblaster?
What sand is suitable for wet sandblasting?
How much sand per m2 of sandblasting?
What's better for sandblasting: sand or corundum?
What sandblasting sand thickness?
How much does corundum for sandblasting cost?
Can baking soda be used for the sandblaster?
Is regular sand suitable for sandblasting?
How much sand is needed for sandblasting?
Which grit size for sandblasting?
What sand for stone sandblasting?
What is the best sand for metal sandblasting?
Is it possible to sandblast with wet sand?
Can I use sugar for sandblasting?
Can salt be used for sandblasting?
What is the best sandblasting agent for severe rust?
What is the most aggressive sandblasting agent?
What is the best sand for sandblasting?
See also other categories