Sandblaster – definition, types, how to choose a sandblaster?
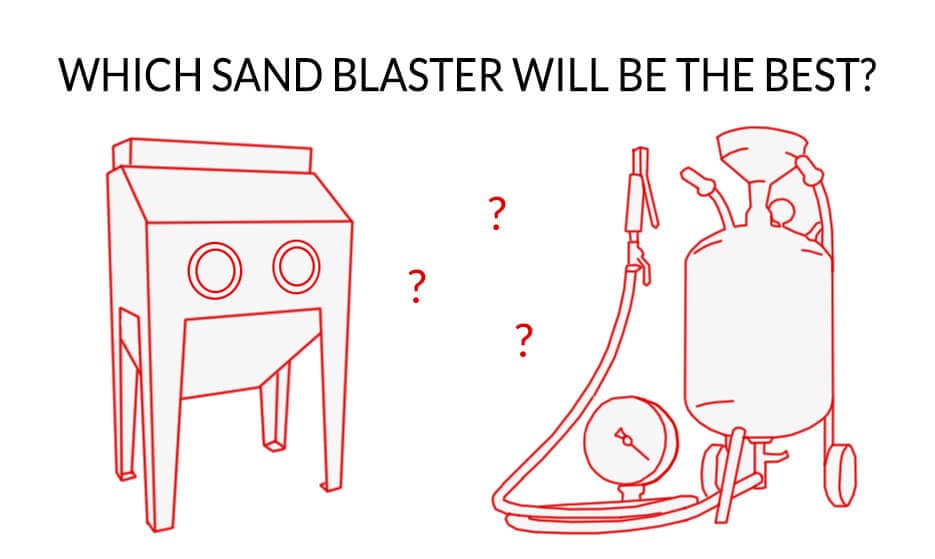
What is a sandblaster?
A sandblaster is a specialised piece of equipment used in various industries to clean, smooth or shape surfaces by shooting an abrasive material (such as sand) under high pressure. The technique, also known as sandblasting, is widely used to remove rust, paint, dirt or old coatings from a variety of surfaces such as metal, wood, concrete or plastic.
Sandblasters are used in a wide range of industries, including building restoration and maintenance, heavy industry, vehicle manufacturing, shipyards, as well as wood, metal and stone processing.
How does a sandblaster work?
The sandblaster works as follows: the abrasive (in the form of fine sand or otherwise) collected in a special tank is sucked in under pressure and directed via a sandblasting hose to a gun with a suitable nozzle. This allows the machine operator to discharge the abrasive jet in the direction of the material to be cleaned.
A hydroblasting machine operates on a slightly different principle, using a jet of water instead of air to transport the abrasive.
What are the types of sandblasters?
The main types of sandblasters are:
- siphon sandblaster,
- water sandblaster,
- cabin sandblaster,
- gravity sandblaster,
- manual sandblaster,
- semi-automatic sandblaster,
- automatic sandblaster,
- injector sandblaster,
- pressure sandblaster.
Read on and you will learn more about each of these.
What is a siphon sandblaster?
The siphon sandblaster is one of the cheapest sandblasters on the market. Its design is characterized by simplicity, as it boils down to an abrasive tank and two connections - one for the compressor and the other for the hose and pressure gun.
In addition to the low price, the big advantage of the siphon sandblaster is its mobility. Thanks to its compact size and mounting on wheels, you can easily transport it from point A to point B.
The tank of the device usually features a capacity of 80-170 liters, and in the set you will often find a set of the most popular nozzles.
When choosing a siphon sandblaster, be primarily guided by the size of the tank and the maximum working pressure, as these two parameters directly affect the cleaning performance.
In addition, it would be good for the device to have a disc valve. On the one hand, it will increase the life of the sandblaster, and on the other hand, it will ensure that it does not need expensive pistons and diaphragms.
What is a water sandblaster?
A water sandblaster is a type of sandblaster that allows dry-wet operation. The additional water jet during cleaning keeps dusting to a minimum, which translates into less dirt generated by the machine and greater worker safety.
Water sandblasters are professional and modern machines that are suitable for working with many materials. They are usually larger than siphon sandblasters, but can still be transported fairly freely when needed.
The tanks in this type of equipment have a capacity of up to 230 liters, and their efficiency reaches up to 80 m2/h (sometimes more). In addition, in most cases they feature a higher working pressure, which allows much better cleaning of various surfaces.
The only significant disadvantage of water sandblasters is their high price.
However, if you want to buy one, it is best to choose a variant with a self-priming water pump and a water treatment and pressure regulation system.
What is a cabin sandblaster?
A cabin sandblaster is a device that allows the cleaning of individual components in an enclosed cabin, rather than in the open. This guarantees high occupational hygiene, as both dust and abrasive remain in an airtight chamber.
The big advantage of this type of sandblasters is a wide cross-section of prices. Depending on the version, you will buy a device relatively cheap or very expensive.
As for the downsides, the main and most important is the lack of mobility. Cabin sandblasters (especially the larger ones) are stationary devices.
Many of them have integrated rubber gloves for working inside the chamber, as well as safety switches that automatically stop operation of the device if the cabin is opened.
What is a gravity sandblaster?
A gravity sandblaster is a type of sandblaster that is characterized by a very simple design, because it is reduced to a small abrasive tank, which is located above the gun. The gravity sandblaster is the cheapest type of sandblaster.
When you start the compressor, pressurized air gradually pushes the contents of the hopper through the nozzle of the gun.
The gravity sandblaster (or mini sandblaster) is a simple and inexpensive tool that is ideal for small jobs of cleaning material from rust, paint residue, and decorating glass by tarnishing. It will also work well when you want to sand out hard-to-reach areas.
What is a hand-held sandblaster?
A hand-held sandblaster is a variation of a cabin sandblaster, in which the entire processing process depends on the operator. This includes loading, as well as moving and sandblasting all the parts.
As you may have guessed, this is the cheapest version of the cabin sandblaster. However, the savings here come with more time-consuming and demanding work.
What is a semi-automatic sandblaster?
A semi-automatic sandblaster is a variation of a cabin sandblaster, in which you still perform the sandblasting process manually, but the material being worked on moves automatically. As the operator, you conveniently control the speed and direction of the piece you are working on.
This allows you to focus on sandblasting, and the process is much faster.
What is an automatic sandblaster?
Automatic sandblaster is a type of sandblaster that performs the entire sandblasting process by itself without the attendance of an operator. After loading the material on the conveyor belt, you program the range of actions on the touch panel, and the rest is taken care of by the automatic machine. This allows for very accurate and repeatable processing of each component.
The automatic sandblaster is the most expensive variant of the cabin sandblaster.
What is an injector sandblaster?
An injector sandblaster is a device in which the abrasive sucked from the tank is combined with pressurized air only in the head, or gun. As a result, a jet of pre-planned parameters comes out of the nozzle.
In machines of this type, the kinetic energy with which the abrasive hits the surface to be cleaned is significantly lower than in pressure sandblasters.
However, the advantage of injector machines is their functionality. Their need for compressed air remains relatively low, so the cost of operation is also low.
Also worth noting is the fact that sandblasters of this type are more mobile.
What is a pressure sandblaster?
A pressure sandblaster is a machine in which the abrasive is contained in a pressure vessel and already there is combined with compressed air. It is then passed to the sandblasting nozzle in the chamber.
From there, it goes into the tank again and the whole process repeats.
This type of solution is up to four times more effective than the injector solution. Unfortunately, it is also about twice as expensive, as the cost of the pressure tank and all the equipment that takes care of the proper operation of the sandblaster comes into play.
This type of equipment is usually used for deep sandblasting, as it significantly reduces the time. They are usually used as sandblasters for metal or various types of stone in stone workshops.
What is a sandblasting gun?
A sandblasting gun is a portable device that is a key component of many sandblasting systems. It is what pressurizes the abrasive agent, such as sand for sandblasting, glass and sometimes even small pieces of metal.
Sandblasting guns are used to precisely clean, dull or remove coatings from small surfaces or hard-to-reach areas where larger sandblasters may be impractical or ineffective.
The unit consists of several key components, including an abrasive chamber, an outlet nozzle, an abrasive feed system and a trigger to control the flow. This allows the user to precisely control the amount and pressure of abrasive fired, allowing for gentle surface cleaning or aggressive removal of tough contaminants (as needed).
Because of their portability and ease of use, sandblasting guns are very popular among professionals and hobbyists who need an effective tool to clean, prepare surfaces or give them a new look.
Which sandblaster should you choose?
Which sandblaster to choose depends on a number of factors, such as the type and size of the project, the type of surface to be treated, and the expected results. Below we have compiled some tips to help you choose the best sandblaster for your needs:
- Scope of work - Consider whether you will be sandblasting large surfaces, such as building walls, or focusing on smaller, more detailed projects.
- Type of surface - Different materials require different treatment. Delicate surfaces, such as wood and some metals, may require lower-powered sandblasters and softer abrasives, while concrete or rust on metal need more powerful equipment and a coarser abrasive.
- Mobility - If you plan to work in different locations, choose a portable unit. Sandblasting guns and smaller, mobile sandblasters are easy to transport, but may have limited capacity and power compared to larger, stationary units.
- Safety and environmental protection - Sandblasting generates a large amount of dust and other particles, which can be harmful to both the operator and the environment. Therefore, consider sandblasters equipped with abrasive recovery systems or operating in enclosed cabins to minimize dust emissions.
- Budget - Prices of sandblasters can vary widely depending on their type, size and functions. Therefore, determine your budget and look for the unit that offers the best value for your money within your financial means.
Remember that the best sandblaster is the one that suits your specific needs. Also consider consulting a professional or equipment supplier for additional advice on choosing the ideal device.
What to consider when choosing a sandblaster?
When choosing a sandblaster, there are some key points to consider:
- Type of sandblaster - Decide whether you need a pressure sandblaster, a siphon sandblaster or perhaps a hand-held sandblasting gun or even a different machine. Each one has its own specific applications and advantages, so your choice should be tailored to the nature of the work you are planning.
- Power and efficiency - Check the power of the machine and its ability to deliver abrasive at the correct pressure. Higher power and pressure means faster and more efficient sandblasting, but also higher energy and abrasive consumption.
- Abrasive compatibility - Make sure the sandblaster is compatible with the type of abrasive you plan to use. Some machines are designed to work with specific materials such as sand, soda, glass or metal particles.
- Tank capacity - A larger abrasive tank capacity means longer working hours without refilling, which is extremely important for large projects. However, larger tanks make the unit heavier and less portable.
- Ergonomics and ease of use - Check whether the sandblaster is easy to use and whether its design will cause undue fatigue during prolonged work. Ergonomic design, adjustable handles and intuitive placement of controls can greatly improve comfort.
- Safety features - Make sure the chosen sandblaster has adequate safety features, including accidental start-up protection and air filtration systems to prevent dust inhalation. Durable and leak-proof connections are also important.
- Durability and reliability - Choose sandblasters made from high quality materials that are resistant to wear and corrosion. Check other users' reviews and warranty information to ensure the unit will serve you for a long time.
- Service and spare parts availability - Make sure the sandblaster model you choose has service and spare parts available. It's important that if something breaks down or needs to be replaced, you won't have any problems getting the unit repaired.
What are the features of a good sandblaster?
The features of a good sandblaster are not only effective cleaning and surface preparation, but also user comfort, versatility and efficiency. Below we take a closer look at the attributes of a good sandblaster:
- Durable tyres - For mobile sandblasters, large, sturdy tyres are essential to easily manoeuvre over a variety of terrains, both indoors and outdoors. They allow the unit to move smoothly around the yard or work area, even on uneven ground.
- Large tank - The large capacity of the abrasive tank is key to working for long periods without the need to constantly recharge. This allows for more efficient and continuous sandblasting, which is particularly important for larger projects.
- Comfortable gun grips - Ergonomically designed gun grips provide comfort and reduce the risk of blisters during prolonged use. This allows for longer working sessions with minimal fatigue.
- Pressure control - The pressure control function is essential if you want to adjust the sandblasting force to suit a specific task. This allows you to gently clean small or sensitive items, as well as effectively tackle larger, more demanding projects.
- Reusable sand - The ability to reuse sand through the use of a tarpaulin or other collection system is beneficial from both an economic and environmental point of view. This minimises the waste of abrasives and increases the efficiency of the work.
- Built-in lighting - Sandblasters equipped with lighting systems are ideal for precision work in shaded areas or on details that require greater brightness. This is because they eliminate the need for additional, bulky light sources.
- Versatility in abrasives - A good sandblaster should be able to work with a variety of abrasives, from traditional sand to walnut shells and aluminium oxide to glass beads. Versatility allows the sandblasting process to be tailored to the specific task, material and desired final result.
A well-designed sandblaster that combines the above features is an indispensable tool for professionals and hobbyists. This is because it enables a wide range of sandblasting operations to be carried out with optimum efficiency and comfort.
How much does a good sandblaster cost?
A good sandblaster costs from a few tens to even several thousand pounds, depending on what type of sandblaster it is. How much a good sandblaster costs depends on a number of factors, such as the type of machine, its performance, features, brand and where it is purchased. Please see below for approximate price ranges to help you get an idea of the sandblaster market:
- Sandblasting guns - The most basic and portable units, which cost between a few tens and hundreds of pounds. They are ideal for hobbyists or for smaller projects.
- Siphon sandblasters - Machines for a variety of applications that can cost from a few hundred to several thousand pounds. The price depends on size, performance and additional features such as abrasive recovery systems.
- Pressure sandblasters - Professional machines that offer the best performance and are designed for intensive use. Their prices start from a few thousand pounds and can reach up to several thousand pounds for models with the highest performance and additional features such as automatic abrasive recovery systems or advanced filtration.
- Specialised sandblasters - Equipment designed for specific applications, such as dry ice or soda blasting, can be even more expensive. Their prices often exceed several thousand pounds (depending on specifications and capabilities).
Remember that, in addition to the cost of purchasing the sandblaster itself, you need to factor in running costs such as abrasives, energy consumption, maintenance and possible repairs. A good sandblaster is an investment that should bring value for years, so you will do well to choose a unit from a reputable manufacturer, even if it involves a slightly higher initial cost.
What kind of compressor for a sandblaster?
A compressor for a cabin sandblaster should have a capacity of at least 600-700 l/min with small nozzles (the larger the nozzle diameter, the more compressed air the device needs).
However, for professional work, a compressor with a capacity of at least 200 liters and a capacity of 4000-5000 l/min will be best.
Sandblasting with a weaker compressor, admittedly, is possible, but you have to reckon with the fact that the process will take much longer and will not produce an ideal result. In addition, some tasks, such as removing powder-coated paint, will be beyond the reach of a less powerful compressor.
What factors to consider when choosing a compressor for a sandblaster
When choosing a compressor for a sandblaster, it is important to pay attention to:
- Capacity - Choose a compressor with sufficient capacity to ensure effective sandblasting. Too low a capacity can lead to uneven sandblasting and the need for frequent interruptions.
- Pressure - The compressor must be able to deliver the pressure required by the sandblaster, which is often 6 to 8 bar (which may be even higher for some applications).
- Tank capacity - A larger tank capacity allows the compressor to run for longer without the need to restart, which is important for long term sandblasting projects.
- Mobility - Depending on your needs, consider a portable compressor that can be easily moved between different work sites.
Is a compressor required for the sandblasting process?
A compressor is essential in the sandblasting process because it provides the compressed air necessary to transport the abrasive from the sandblaster to the surface to be treated. It is the driving force for efficient operation, as it gives the abrasive the right speed and pressure to effectively remove impurities (such as rust or paint).
What kind of hose for a sandblaster?
For a sandblaster, you need a hose that is resistant to abrasion, as it will transport the abrasive from the tank to the gun.
To ensure that the friction created by this work does not cause internal damage, you need the right material. Therefore, sandblasting hoses are most often made of special rubber, and in some cases, polyurethane.
Also take into account that the diameter of the sandblasting hose should be matched to the nozzle (usually 3-4 times larger than it is), and its length to the needs of the installation. This will ensure that the processing parameters of compressed air and abrasive will be optimal.
What kind of connectors for sandblasting?
For sandblasting, claw couplings, also known as Chicago connectors, are used. They are characterized by versatility, as well as ease of connection and disconnection, due to their distinctive design. They have specific "claws" that snap into each other, with which they guarantee a strong and tight connection.
There is also an additional protection against disconnection in the form of a pin.
Slightly different are the connectors-handles for nozzles, as they do not have claws. Instead, they are characterized by an internal thread into which the nozzle can be screwed.
The most popular materials for sandblasting connectors are galvanized iron and nylon (polyamide).
How to select nozzles for a sandblaster?
To choose the right nozzle for a sandblaster, you need to consider its shape, size and manufacturing material. Each of these features affects the speed and distribution of the abrasive, and thus the final sandblasting effect.
Below you will find a few tips useful when making your decision:
- Manufacturing material - Nozzles can be made of various materials, such as boron carbide, silicon carbide, ceramic, or stainless steel. Boron carbide is very durable and resistant to abrasion, making it ideal for intensive use, while ceramic nozzles are cheaper, but wear out faster.
- Nozzle size - The size of the nozzle opening should be adjusted to the type and size of abrasive, as well as to the power of the compressor. An opening that is too small can cause blockage and inefficient sandblasting, while an opening that is too large will reduce precision and increase abrasive consumption.
- Nozzle shape - The shape of the nozzle affects the focus and distribution of the abrasive stream. Rectangular-shaped nozzles are better for working on large, flat surfaces, while conical-shaped nozzles are better suited for corners and hard-to-reach areas.
- Nozzle length - Longer nozzles allow for better focus of the abrasive stream and are more effective over longer distances, but are less easy to maneuver in tight spaces.
- Sandblaster compatibility - Make sure the nozzle you choose is compatible with your sandblaster in terms of size and connection type.
- Application - Consider the specifics of your project (whether it requires precision sandblasting up close or working on large areas from a greater distance). This will help you choose a nozzle with the right shape and size.
- Wear and tear - Check the condition of the nozzle regularly, as progressive wear and tear can alter its properties and sandblasting efficiency. Replace the nozzle when you notice significant deterioration or damage.
What kind of accessories are needed for sandblasters?
The following accessories are needed with sandblasters:
- Personal protection - Appropriate personal protective equipment is essential for operator safety. These include dust masks or respirators, safety goggles, abrasion-resistant gloves, and special protective suits.
- Sandblasting booths - These are enclosed spaces where sandblasting takes place to prevent dust and debris from spreading outside the work area. These booths are often equipped with lighting and filtration systems.
- Abrasive recovery systems - Allow for reuse of abrasive, which is economical and environmentally friendly. These systems can be integrated into the sandblasting booth or be separate units.
- De-oiling microfilters - Reduce contamination of the air flowing through them, removing most of the oil particles that result from oil compressors. An ordinary air filter may not be able to handle this.
- Dehumidifiers - They are used to clean the working medium of moisture in a more efficient way than standard air filters and separators. The most common type of this device is a refrigeration dryer, but if more efficient moisture removal is required, an adsorption dehumidifier is preferable.
- Pressure regulators and pressure gauges - They allow precise control of the pressure of the air used in the sandblasting process, which is crucial for optimal results.
- Lighting systems - When working in poorly lit spaces or sandblasting booths, a good light source is essential for precise sandblasting.
- Covers and protection - Various types of protective covers and tapes are used to protect parts that should not be sandblasted.
An investment in high-quality accessories can significantly improve work efficiency, reduce operating costs and increase user safety. Therefore, it is worth considering your needs carefully and choosing accessories that best meet the requirements of your specific application and working environment.
FAQ
What should a sandblaster for metal be like?
A sandblaster for metal should be powerful and durable, with adjustable pressure to adjust the sandblasting force according to the type of metal and the desired end result. Pressure sandblasters with nozzles made of boron carbide or other highly abrasion-resistant material are recommended.
What pressure is needed for sandblasting?
The pressure needed for sandblasting depends on the type of surface to be treated and the abrasive, but typically ranges from 4 to 8 bar (60 to 120 PSI). Harder tasks, such as removing rust from metal, may require higher pressures.
How do I adjust the size of the sandblaster to suit my needs?
To adjust the size of the sandblaster to suit your needs, adapt it to the size of the project and frequency of use. For small, occasional jobs, a compact siphon sandblaster or sandblasting gun will be sufficient. On the other hand, for larger, professional applications, a more massive pressure sandblaster with a capacious abrasive tank will work better.
Can I use a small compressor for sandblasting?
You can use a small compressor for sandblasting, but there is a risk that it will not have the desired effect. This is because small compressors may not provide enough air for effective sandblasting, resulting in slower operation and poorer end results. Therefore, for best results, it is recommended to use a compressor with the right capacity according to the requirements of the sandblaster.
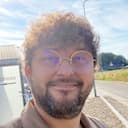
Articles author
Bartosz Kułakowski
CEO of Hosetech Sp. z o.o.
Bartosz Kulakowski is an industrial hoses and couplings specialist with over 10 years of experience. Bartosz has been present in the technical industry since 2013. He gained experience as a technical and commercial advisor in the sector of plastic conveyor belts, steel structures, industrial hoses, and connectors. Since 2016, he has specialized exclusively in hoses and connectors. In 2019 he opened his own business under the HOSETECH Bartosz Kulakowski brand and since July 2022 he has been the CEO of the capital company HOSETECH Sp z o. o. (LLC).
Table of Contents
What is a sandblaster?
How does a sandblaster work?
What are the types of sandblasters?
What is a siphon sandblaster?
What is a water sandblaster?
What is a cabin sandblaster?
What is a gravity sandblaster?
What is a hand-held sandblaster?
What is a semi-automatic sandblaster?
What is an automatic sandblaster?
What is an injector sandblaster?
What is a pressure sandblaster?
What is a sandblasting gun?
Which sandblaster should you choose?
What to consider when choosing a sandblaster?
What are the features of a good sandblaster?
How much does a good sandblaster cost?
What kind of compressor for a sandblaster?
What factors to consider when choosing a compressor for a sandblaster
Is a compressor required for the sandblasting process?
What kind of hose for a sandblaster?
What kind of connectors for sandblasting?
How to select nozzles for a sandblaster?
What kind of accessories are needed for sandblasters?
FAQ
What should a sandblaster for metal be like?
What pressure is needed for sandblasting?
How do I adjust the size of the sandblaster to suit my needs?
<b>Can I use a small compressor for sandblasting?</b>
See also other categories