9 benefits of using chillers in an industrial cooling system
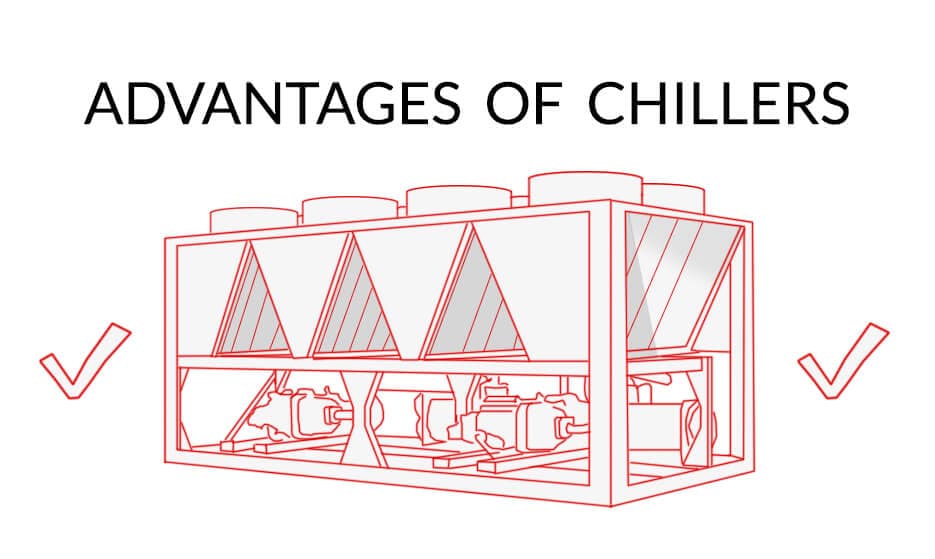
What are the benefits of chillers?
The benefits of chillers include:
- precise temperature control,
- uninterrupted production process,
- ability to cool oil,
- energy efficiency,
- longevity,
- acceleration of production processes,
- quiet operation,
- scalability,
- ecology.
Read on and you will learn more about each of these.
Precise temperature control
Chillers effectively remove excess heat generated by industrial machinery. As a result, they keep operating temperatures within the optimum range.
In this way, they prevent thermal stress and extend the service life of critical components.
Furthermore, precise temperature control allows processes to be optimised in various industrial applications. Whether in production, chemical processing or energy generation, maintaining specific thermal requirements ensures consistent product quality and maximises productivity.
Uninterrupted production process
Chillers keep equipment temperatures low during production processes. With the assistance of several cooling system components (from refrigeration circuits with standard lead-lag control to automatic pumps), they ensure the continuous operation of the plant.
As the chiller must meet the changing requirements of the application, many manufacturers offer additional capacity control options.
Ability to cool oil
The industrial environment is harsh on machinery, making it necessary to keep oil temperatures low. Overheating can lead to premature failure and long downtimes.
This is why oil chillers have been specifically designed for industrial machinery. They increase the efficiency, reliability, and service life of equipment.
Energy efficiency
Process cooling with chilled water units is very efficient for a number of reasons.
Firstly, water-cooled chillers operate independently of the ambient temperature, thus avoiding the system inefficiencies that occur when thermal conditions fluctuate.
Furthermore, due to their operating principle (heat removal using water), chillers are very effective in reducing temperatures quickly in larger industrial applications.
Longevity
Chiller manufacturers usually design chillers to last a very long time. Compared to other refrigeration systems, water-cooled chillers are more durable and have a much longer service life.
The explanation is relatively simple. Most components in water-cooled chiller systems are usually installed indoors. Only a few parts come into contact with natural atmospheric agents (such as rain, wind, sunlight, ice), so there is little risk of possible material degradation.
It is true that air-cooled chillers also have a long service life, but they are mostly located outdoors. For this reason, they are more prone to faults caused by atmospheric changes.
Acceleration of production processes
Chillers increase production speeds by optimising temperatures.
Industrial plants achieve maximum productivity under properly regulated thermal conditions and chillers provide a stable process environment.
In addition, chiller systems prevent damage to heat-sensitive machine components. They thus reduce unwanted downtime for repairs, which could slow down or even stop production altogether.
Quiet operation
Process cooling using water-cooled chillers is quiet. They have few dynamic components and as such do not generate unwanted noise in an industrial environment.
As a result, you will use them in virtually any environment while complying with industrial noise level regulations.
Scalability
Chillers are highly flexible industrial equipment that can be modified to operate in a variety of indoor and outdoor conditions. Depending on requirements, chillers are created in a wide range of sizes and configurations with different coolant hoses to ensure maximum compatibility for individual businesses.
Ecology
Water-cooled chillers are also eco-friendly. For a number of reasons.
Firstly, they enable closed-cycle cooling, which minimises waste. The water is recirculated and reused. This reduces its overall consumption in industrial operations.
Secondly, by optimising cooling processes, chillers reduce reliance on harmful refrigerants and promote the use of environmentally friendly alternatives. As a result, they reduce the environmental impact of industrial cooling systems.
Thirdly, chillers ensure compliance with environmental regulations and standards regarding temperature control and energy efficiency. Compliance not only helps protect the environment, but also prevents potential penalties for industrial facilities.
You can also opt for an air-cooled chiller. This will drastically reduce the need for water in the cooling processes. This is an ecological and cost-effective solution if water prices in your region are high.
FAQ
Are chillers noisy?
Chillers are noisy, especially in the case of air-cooled systems. However, water-cooled chillers can also generate noise due to compressor operation. They also cause some vibrations.
Fortunately, modern cooling systems offer many options for noise reduction, so that chillers operate relatively quietly.
Can a chiller freeze?
Yes, a chiller can freeze. Chilled water, which is the medium in a chiller, can be used not only for cooling, but also for freezing. One essential part of this is the mixture of water and glycol.
Do chillers use ammonia?
Yes, chillers use ammonia. This is because it has very good cooling properties and is effective in reducing temperatures in large industrial facilities
Summary
Chillers play a very important role in many commercial buildings and industrial plants. Some production processes would simply be impossible without an adequate cooling system.
However, and even where chillers are not necessary, they bring many benefits to companies by their presence. Increased productivity, protection of machinery from overheating or environmentally friendly solutions are just a few examples from the long list of advantages we have written about in the article.
This is why chillers are becoming increasingly popular.
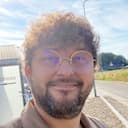
Articles author
Bartosz Kułakowski
CEO of Hosetech Sp. z o.o.
Bartosz Kulakowski is an industrial hoses and couplings specialist with over 10 years of experience. Bartosz has been present in the technical industry since 2013. He gained experience as a technical and commercial advisor in the sector of plastic conveyor belts, steel structures, industrial hoses, and connectors. Since 2016, he has specialized exclusively in hoses and connectors. In 2019 he opened his own business under the HOSETECH Bartosz Kulakowski brand and since July 2022 he has been the CEO of the capital company HOSETECH Sp z o. o. (LLC).
Table of Contents
What are the benefits of chillers?
Precise temperature control
Uninterrupted production process
Ability to cool oil
Energy efficiency
Longevity
Acceleration of production processes
Quiet operation
Scalability
Ecology
FAQ
Are chillers noisy?
Can a chiller freeze?
Do chillers use ammonia?
Summary
See also other categories