What is a chiller? – A complete guide
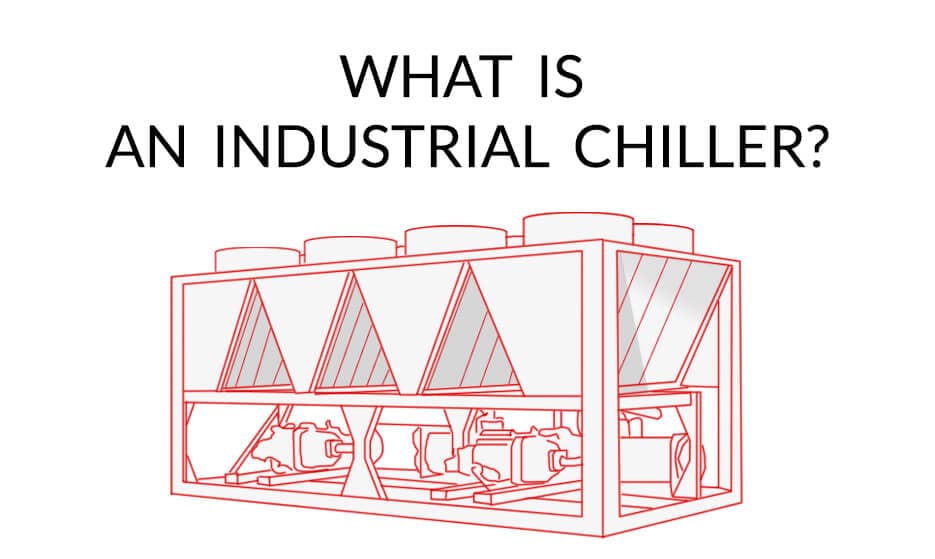
What is a chiller?
A chiller is a refrigeration system that reduces the temperature of machinery, industrial spaces and process fluids. This is does by removing heat from the process and transferring it elsewhere.
In some industries, industrial chillers are essential for temperature control. These include injection moulding, metal plating or food processing.
Why use chillers?
Chillers are worth using because they provide benefits where strictly defined operating temperatures are required.
When integrated into heat-sensitive processes, chillers prevent thermal damage to the equipment. In addition, they guarantee that there are no changes in the end products that could be damaged by exposure to inappropriate temperatures.
How does a chiller work?
Chiller works as follows: a pump circulates cold water or water/glycol solution from the chiller to the process. The cold fluid removes heat from the process and then heated returns to the chiller. The fluid is transported using coolant hoses.
Chillers contain a chemical compound called a refrigerant. There are many types of refrigerant, but all work on the basic principle of compression and phase transformation from liquid to gas and back to liquid.
This process is called the refrigeration cycle.
The refrigeration cycle starts with a low-pressure mixture of liquid and gas flowing into an evaporator. There, heat from the process water or a solution of water and glycol boils the refrigerant, so that it changes from a low-pressure liquid to a low-pressure gas.
The low-pressure gas enters the compressor, where it is compressed into a high-pressure gas. This then goes into the condenser, which removes heat using ambient air or water. This cools the high-pressure gas into a high-pressure liquid.
Later, the high-pressure liquid moves to the expansion valve, which controls the amount of liquid refrigerant entering the evaporator. From that point on, the refrigeration cycle starts all over again. Below you can see a diagram of how a chiller works.
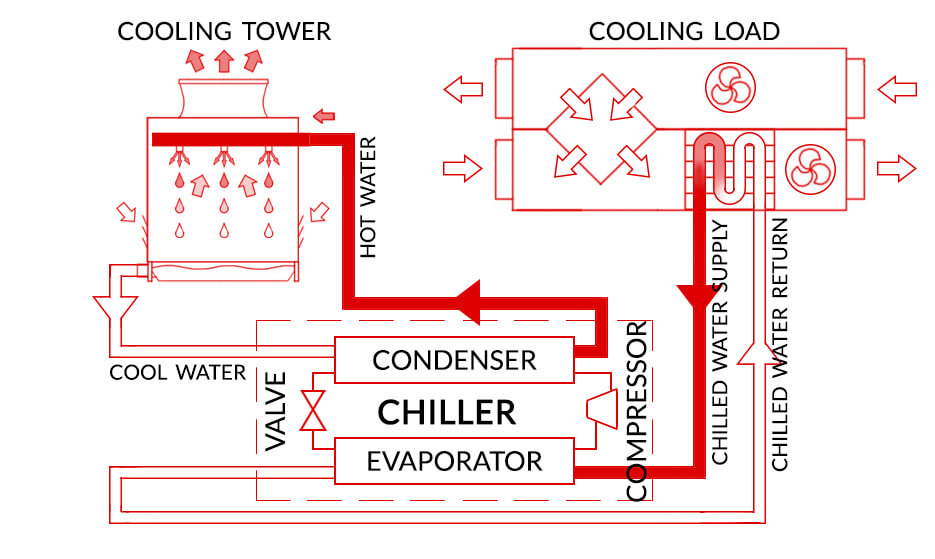
What are the types of chillers?
There are three main types of chillers - water-cooled chillers, air-cooled chillers, and absorption chillers.
There are also special variations of the unit, such as the glycol chiller. However, here we will focus only on the most important types.
Water-cooled chillers
Water-cooled chillers use water from an external cooling tower to remove heat from the gaseous refrigerant in the condenser before it undergoes a phase change to liquid.
Air-cooled chillers
Air-cooled chillers use fans and ambient air to remove heat from the refrigerant in the condenser.
Absorption chillers
Absorption chillers use a heat source (e.g. solar energy or waste heat) to direct coolant through the system. Absorption chillers do not have a compressor.
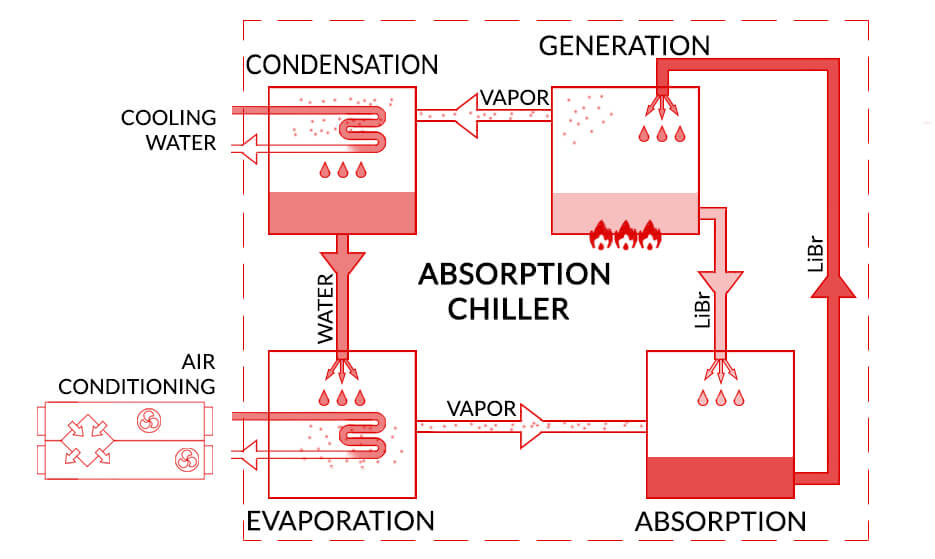
What are the applications of chillers?
Key applications of chillers include food processing, metal processing, injection moulding, and room cooling and many more.
Read more about the most important applications of chillers below.
Food processing
Chillers are widely used in food production and processing, which requires a high level of precision when it comes to temperature control.
For example wine chillers are used to control the temperature during fermentation and storage of wine. While bakery chillers help to cool mixers, drinking water and yeast tanks, key components of the bakery.
Metal processing
Chillers remove excess heat during metal processing. Temperature control is also essential for metal finishing, such as electroplating or electroless plating.
Their operation is necessary because the above-mentioned processes usually require very high temperatures up to several hundred degrees to bind metals.
Some industries use chillers to cool the anodising liquid in the heat exchanger or use glycol/water as a cooling medium to reduce the temperature inside the tank.
Injection moulding
The chiller can deliver a flow of mould cooling fluid at an ideal rate, thus guaranteeing optimum product quality.
Injection moulding is a technique for the mass production of plastic parts using an injection moulding machine, thermoplastic pellets and a mould. It requires maintaining precise temperatures to prevent problems such as cracking, warping and internal stresses in the final product.
Room cooling
In production facilities that generate a lot of heat from heavy machinery, a chiller unit prevents extreme temperatures in offices and other working spaces.
It also helps save on the cost of purchasing separate cooling systems.
What are the benefits of chillers?
The main benefits of chillers include:
- service life (up to 20-30 years with proper maintenance),
- energy efficiency,
- acceleration of production processes,
- protection of machinery,
- water saving,
- quiet operation (for water-cooled chillers),
- low installation and maintenance costs (for air-cooled chillers),
- multiple applications.
How to maintain the chiller?
To effectively take care of the chiller, remember to perform regular maintenance. The most important parts of chiller maintenance are:
- keeping a log of operational data,
- keeping the ductwork clean,
- reducing the condenser water temperature,
- inspecting condenser water loops,
- checking the system for leaks,
- measuring glycol concentration,
- maintaining optimal chilled water flow rate,
- compressor oil analysis (if applicable),
- inspection of motors and starting mechanism.
In general, it is necessary to periodically inspect all components of the system. This includes pipes, cables, chiller components, filters and many other things.
How to select a chiller?
To select a chiller that suits your needs, pay attention to the following:
- type of application,
- cooling performance,
- size,
- energy efficiency,
- control,
- cost.
Type of application
The use case is one of the first variables to consider when purchasing a chiller.
Different applications require different chillers. Therefore, understanding what type of installation you need is a great start to the buying process.
Cooling performance
When choosing a chiller, also consider its cooling performance. This is the amount of heat that a chiller can remove from a room. Cooling capacity is measured in tons.
To determine the required cooling capacity, you need to know the heat load. You can calculate it using a special calculator.
Chiller Size
In many chillers, size and efficiency go hand in hand. A chiller that is too large will use more energy than necessary, reducing profit. Conversely, a chiller that is too small may not be able to keep up with the needs of the facility.
The right chiller allows for efficient cooling while saving energy and money.
To determine the correct chiller size for your facility, determine the desired temperature, flow rate and required coolant type in addition to the heat load.
Energy efficiency
Another important factor in choosing a chiller is energy efficiency. The more efficient a chiller is, the less energy it uses, saving you money on your bills.
There are many factors that affect the energy efficiency of a chiller, including:
- quality of maintenance,
- type of compressor,
- insulation,
- control components.
Control
Chiller unit controls are important for many reasons. First and foremost:
- enable you to set the desired temperature,
- help optimize chiller operation,
- they provide diagnostic information.
There are many different types of controls available for chillers. The most basic is the thermostat, which simply turns the system on and off when the temperature reaches a certain point.
More advanced controls, such as variable speed drives, help optimize chiller operation and save energy.
Cost
Before purchasing a chiller, consider its initial and operating cost, as well as the potential price of maintenance and expected service life.
Water-cooled systems typically have a higher initial cost and require more installation work than air-cooled versions.
Then again, air-cooled systems consume a significant amount of energy to power the fans. However, they reduce operating costs because they do not have the cooling tower that the water-cooled version requires.
What are the typical problems with chillers?
Typical problems with chillers are primarily corrosion, insufficient maintenance, and electrical problems.
Chiller corrosion
Chillers use metal pipes (usually copper or carbon steel) to transfer water between the chiller and the process. The presence of oxygen in the water can cause corrosion.
However, if the water and pipes are properly treated, the risk of this occurring decreases significantly.
On the other hand, inadequate treatment causes sediment, minerals and bacteria to enter the system. Their accumulation differentiates the oxygenation level, which also leads to corrosion.
In addition, any point where two different metals are used is more prone to corrosion. This is due to the different electrochemical properties of the materials.
Regardless of how corrosion occurs, it often causes leaks. In turn, these damage the chiller, reduce its efficiency and can devastate the surrounding area.
Insufficient maintenance of chillers
Chillers require a lot of maintenance to keep them in good condition. If you don't take proper steps in this regard, the chiller may corrode, clog, lose efficiency or experience many other problems.
Electrical problems in chillers
The electrical systems in chillers are carefully designed and as complex as the rest of the machine. Therefore, they can be easily knocked out of balance by a high voltage spike or wear and tear.
If there is a grounding problem or a power failure, the chiller can detect this and shut down.
However, overloading the chiller can cause it to overheat, which will likely lead to failure. In addition, wires and cables sometimes become loose or damaged after maintenance or negligence, sometimes resulting in chiller malfunction.
How much does a chiller cost?
A chiller costs from a few to tens of thousands of pounds. In large industrial facilities, the price of the installation may even exceed several hundred thousand pounds. It all depends on the size, type and performance of the chiller.
It is best to consult the supplier or manufacturer for detailed pricing information.
FAQ
Can the chiller be used in industrial processes?
Yes, the chiller unit can be used in industrial processes to remove heat from machinery, equipment and fluids. This helps maintain a constant temperature and prevents equipment damage. Chillers are also used where precise temperature control is required, such as in food processing and semiconductor manufacturing.
What refrigerants are commonly used in chillers?
Refrigerants commonly used in chillers include R-134a, R-410A and R-407C. However, know that many of these are being replaced by newer, more environmentally friendly alternatives.
Can a chiller be used in residential buildings?
Yes, chillers can be used in residential buildings to provide cooling during hot weather. However, it is usually a more expensive solution than air conditioners, so it is not as popular in this sector.
Can a chiller be used for heating?
Yes, a chiller can be used for heating thanks to a process called "reverse cooling". During it, the chiller removes heat from a source, such as a hot water boiler. It then transfers this to a heat exchanger, which heats the building or process.
Summary
Chillers are indispensable equipment for many industrial plants, as well as commercial buildings. They enable them to work efficiently and provide many benefits.
By understanding the basics of chillers, as well as their types, you will find it much easier to choose the right solution for your needs. Furthermore, you will take better care of the installation, so that it will serve you efficiently for many years.
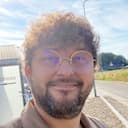
Articles author
Bartosz Kułakowski
CEO of Hosetech Sp. z o.o.
Bartosz Kulakowski is an industrial hoses and couplings specialist with over 10 years of experience. Bartosz has been present in the technical industry since 2013. He gained experience as a technical and commercial advisor in the sector of plastic conveyor belts, steel structures, industrial hoses, and connectors. Since 2016, he has specialized exclusively in hoses and connectors. In 2019 he opened his own business under the HOSETECH Bartosz Kulakowski brand and since July 2022 he has been the CEO of the capital company HOSETECH Sp z o. o. (LLC).
Table of Contents
What is a chiller?
Why use chillers?
How does a chiller work?
What are the types of chillers?
Water-cooled chillers
Air-cooled chillers
Absorption chillers
What are the applications of chillers?
Food processing
Metal processing
Injection moulding
Room cooling
What are the benefits of chillers?
How to maintain the chiller?
How to select a chiller?
Type of application
Cooling performance
Chiller Size
Energy efficiency
Control
Cost
What are the typical problems with chillers?
Chiller corrosion
Insufficient maintenance of chillers
Electrical problems in chillers
How much does a chiller cost?
FAQ
Can the chiller be used in industrial processes?
What refrigerants are commonly used in chillers?
Can a chiller be used in residential buildings?
Can a chiller be used for heating?
Summary
See also other categories