Chiller maintenance - A guide for summer and winter
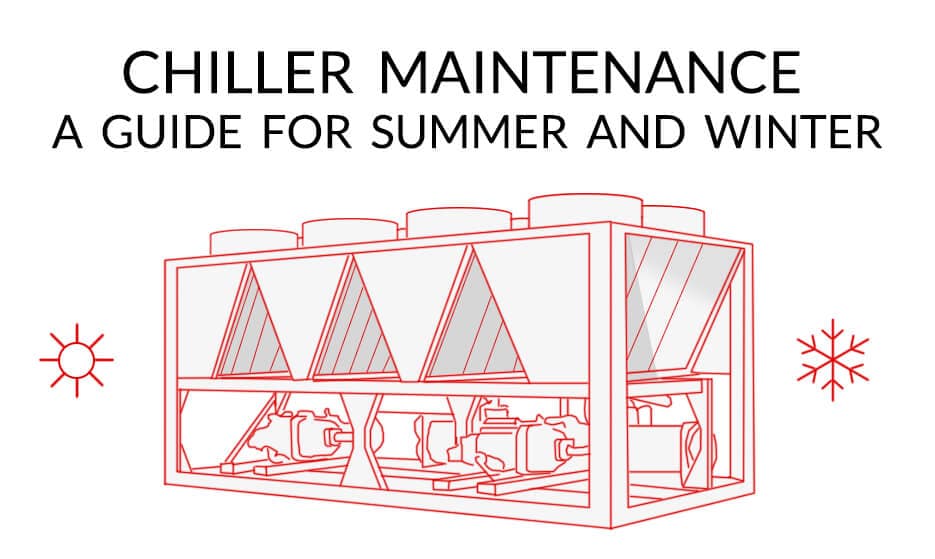
Why is it worth maintaining chillers regularly?
It is worth maintaining chillers regularly, as well-maintained cooling systems do not use as much energy.
Conversely, those with contaminated condenser or evaporator pipes, leaking refrigerant from coolant hoses, poor water treatment or other problems can increase operating costs. In addition, sometimes they require unplanned downtime during which necessary repairs and maintenance will take place.
Therefore, make sure that your service plan meets the necessary minimum recommended by the manufacturer of the respective chiller.
Chiller maintenance checklist
Below are the daily, weekly, monthly and annual maintenance activities you should consider to keep your industrial chillers in good condition.
Daily chiller maintenance checklist
Daily maintenance includes an analysis of the regular operation of the chiller:
- Check chilled water temperatures entering and leaving the chiller system.
- Check and verify condenser water temperatures entering and leaving the system.
- Check the power and current drawn by the compressor.
- Check the oil level and temperature. Top it up if necessary.
- Check condenser and evaporator pressure.
- Check and record oil pressure readings.
- Check for unusual noises and vibrations in the chiller system.
Weekly chiller maintenance checklist
The main steps for weekly chiller maintenance are as follows:
- Check the fluid level with a sight glass.
- Check hoses and coils for visible leaks.
- Check the external condition of the condenser.
- Check and record all operating temperatures and pressures. Ensure that all values correspond to normal operating conditions.
Monthly chiller maintenance checklist
At the end of each month, focus on the following tasks:
- Check system components for wear and tear.
- Check the lubricant level in pumps and motors. Top up the grease if necessary.
- Check the condenser and clean the coils.
- Clean the condenser water filters.
- Run the chiller at full load and check the liquid level in the evaporator.
- Check the compressor motor for operating temperature. Make sure it is not overheating.
Annual chiller maintenance checklist
In addition to daily, weekly and monthly maintenance checks, schedule annual shutdowns. During these:
- Chemically wash the condenser coils.
- Change all oil filters.
- Change all the oil. Make sure you use only approved oil.
- Straighten the fins and fans of air-cooled condensers.
- Check the liquid line filter. Change it if necessary.
- Check the condition of the water filters. Change them if necessary.
- Check the quality of the circulating water in the water-cooled condensers. Replace the water if necessary.
- Check the condition of the shut-off valves. Lubricate the moving parts of the shut-off valve.
- Check and verify the operation of the valve limit switch.
- Check and verify the operation of the vane throttle.
- Check the physical condition of the starter panel.
- Check contacts and terminals of electrical components.
- Check the condition of the terminal blocks. Change them if necessary.
- Check loose connections in electrical circuits and components.
How to maintain chillers in summer?
Maintain chillers in the summer as follows:
- remove dirt and debris,
- clean the coils,
- check condenser inlet filter,
- clean and check panels and steel structure,
- check for leaks,
- analyse the system and chilled water,
- plan maintenance and service.
After months of wind, rain, leaves and snow, your chiller probably could needs some maintenance. A good inspection and cleaning before the summer will give you the confidence that continued production will run smoothly.
Below, we explain each step of the above task list in more detail.
Remove dirt and debris
If the chiller unit is outside, dirt, leaves and other debris will not only surround it, but will even get inside the housing. Remove the debris to ensure good airflow and access to the unit.
For more thorough cleaning to eliminate rodents or nests, we recommend using a professional to carry out a risk assessment and be aware of all potential hazards.
Clean the coils
Condenser coils and chiller fins should also be properly cleaned to ensure effective heat transfer. Accumulated dirt impedes temperature transfer in the cooling process, forcing the chiller to work harder.
As a result, its efficiency decreases and energy consumption and operating costs increase.
Check and clean the chiller hoses with appropriate approved chemicals and mains water. Use a soft hand brush for this.
Pressure washers, inappropriate cleaners and unsuitable brushes can damage the unit.
Check condenser inlet filter
Remove, check and clean the condenser inlet filter. If dirt accumulates on it, it will just as negatively affect the performance of the chiller as dirt on the condenser coil.
This is very important for point-of-use chillers, which are usually located indoors in oily or dusty environments.
Clean and check panels and steel structure
Wipe down each panel and the frame of the unit including the supporting structure. In addition, inspect the entire unit for corrosion or breach of panel seals.
If deficiencies are found, repair them to prevent additional damage. Dirt or mould left behind can quickly become permanent and corrosive.
Also check for water accumulation on the panels, hinges or around the base of the unit.
Check for leaks
Piping, pumps and related components need to be inspected. If you identify a leak, repair the component immediately.
Unlike water, refrigerant and oil leaks are much more difficult to detect. They will require investigations and leak tests.
If fitted, any fixed leak detection systems and alarms should also be tested.
Analyse the system and chilled water
The chiller is considered the heart of the system. However, the system that connects to it is equally important to ensure optimum performance.
Check filters for proper flow and pressure. Inspect and test valves and actuators together with flow switches and trace heating to avoid simple alarms.
To protect against freezing, carry out a water viscosity test with a refractometer. It is also possible to analyse the chilled water as part of a water treatment programme including glycol and inhibitors.
Plan maintenance and service
Lastly, and most importantly, plan the servicing of the chiller unit. A regular maintenance schedule is the best thing you can do to keep your system in good condition.
Inspecting the switchgear, testing the compressors and electronic components - including the checklist listed above will ensure the chiller is working well and ready for summer.
However, some preventive procedures need to be carried out by a professional.
Regular inspections and maintenance will ensure that the system always performs optimally.
How to maintain chillers in winter?
To effectively maintain your chillers in winter, follow the advice below:
- prevent freezing,
- clean the coils and other parts of the system,
- check for leaks,
- check insulation,
- set maximum efficiency,
- check crankcase heaters and evaporator heaters.
This will help you minimise the impact of winter weather on the performance of your chiller. Read on and you will learn more about each of the points mentioned.
Prevent freezing
To prevent the chiller from freezing, make sure that the amount of glycol in the system is adequate. Check the glycol content regularly during the winter period and keep it constant.
The correct amount for your system should be specified in the documentation provided with the unit.
Also check that the heating tape and any connections are not damaged or corroded. This will avoid the risk of failure and frozen pipes.
Remember that any electrical checks should be carried out by a qualified engineer using the correct equipment.
Clean the coils and other parts of the system
Coils are often stressed during the winter months due to the build-up of dirt, mould and other debris. Sediment builds up gradually, but over time it forces the chiller to work harder as it reduces airflow, cooling capacity and pressure.
This results in a decrease in efficiency, thereby increasing energy consumption and operating costs.
To avoid problems, clean and maintain the coils regularly. When doing so, remove any waste, rubbish and general debris from around the chiller unit.
Also, as with summer maintenance, check and clean other components of the cooling system. In particular, focus on the condenser inlet filter, the protective coating of the condenser fins/coils and the panels and steel structure.
Check for leaks
Leaks waste the energy of the machine and the company's money, that is why every contractor tries to avoid them. And you too should regularly check your cooling system for leaks.
Water leaks are generally obvious When you spot them, have them repaired immediately.
When it comes to coolant leaks, on the other hand, they are more difficult to detect. They usually require a leak test to be carried out by a qualified engineer.
Check insulation
Also make sure the thermal insulation is in good condition. It should be properly attached to the tank/pipes - you can't afford to lose heat during the winter months.
Also check for condensate leaks.
Repair and replace insulation where necessary.
Set the maximum capacity
You can change the settings on the control panels of chillers.
When you adjust the setpoints to the outside temperature, the chiller's efficiency will improve. This is a simple fix that will increase energy and money savings.
Check crankcase heaters and evaporator heaters
You will find crankcase and evaporator heaters in most chillers. They are very important when external thermal conditions change, as they bring all fluids to operating temperature before starting the system.
If the heaters were damaged or not working properly, the chiller would work much harder during start-up, leading to excessive wear and tear on the parts.
Therefore, crankcase and evaporator heaters should be checked, tested and replaced if necessary.
What are the benefits of regular chiller maintenance?
The benefits of regular chiller maintenance include:
- cost savings,
- energy efficiency,
- extended service life,
- improved efficiency and reliability,
- safety.
Read on and you will learn more about each item on the list.
Cost savings
Regular maintenance greatly reduces the risk of costly breakdowns. Although you won't avoid all chiller malfunctions, servicing will save you a lot of money on unforeseen heating and cooling emergencies.
Energy efficiency
A well-maintained cooling system can result in significant energy savings - as much as 10%to 40%! So why not ensure your chiller can run at peak efficiency and benefit from lower monthly utility bills?
With regular maintenance, it is possible.
Extended service life
Equipment that is clogged with dirt, dust and other debris has to work much harder and longer to produce the same amount of cooling. This results in premature wear or failure of expensive components.
Why waste money on new equipment when it is much more cost-effective to perform preventive maintenance? Extending the service life of your chiller instead of buying a new equipment is good for your wallet.
Improved efficiency and reliability
To do its job well, a chiller must dissipate heat efficiently. This applies to all parts of the unit, especially its refrigeration circuits.
If the heat transfer is insufficient, the chiller will not be able to reduce the temperature to the preferred level. What's worse, it may not even provide any cooling effect at all!
Dirt in the condenser is one of the main causes of poor heat transfer. Minerals from hard water, scale, algae and dirt can block the condenser tubes. In addition, scale deposits on chiller components can increase the chiller's thermal resistance.
When any of these factors arise, equipment performance is bound to be affected.
Therefore, proper maintenance is essential. This will help you avoid the above problems.
Safety
Regular maintenance also improves the safety of chiller operation, as you will detect possible leaks in advance. Due to leaks in some parts of the system, refrigerant can escape, posing a risk not only to the environment but also to employees.
Leaks are also risky for the chiller itself. A shortage of refrigerant forces the compressor to work harder, resulting in higher energy costs, poorer cooling and (worse) a greater risk of failure.
How often does a chiller unit need to be serviced?
A chiller should be serviced at least once a year. However, it depends on many factors, including the type of chiller, its operating environment and the intensity of use.
Some maintenance should be carried out on a daily, weekly or monthly basis. In this way, you will detect in advance drops in system performance and the possible faults behind them.
As a result, you will prevent major and costly failures.
Why is it worth hiring professionals for chiller maintenance?
There are plenty of reasons why it's worth hiring professionals for chiller maintenance. Here are the most important ones:
- Expertise - Professional technicians have the qualifications and experience to carry out genset maintenance correctly. They know what to look for and how to repair faults before they lead to serious damage.
- Advanced preventive maintenance - A professional service will extend the service life of your chiller and prevent costly repairs. Technicians will clean and lubricate chiller components, check refrigerant levels, look for any leaks, and inspect electrical components and safety systems.
- Peace of mind - Knowing that your chiller is well looked after by professionals will give you peace of mind. You won't worry about the risk of unexpected breakdowns or costly repairs.
FAQ
Is the chiller part of the HVAC system?
Yes, the chiller is part of the HVAC (heating, ventilation and air conditioning) system. Chillers are used in HVAC systems to provide air conditioning in buildings by generating chilled water that cools the air.
What is the ideal chiller temperature?
The ideal chiller temperature depends on the specific application and the type of chiller used.
How does the chiller control the temperature?
The chiller controls the temperature with controllers that allow the user to set the desired temperature and maintain it within a specified range. The controllers use pressure-sensitive parts, digital controls and other sensors to monitor the system.
Summary
Chillers provide essential cooling to production processes and commercial buildings, but require regular maintenance. Indeed, without it, the performance and reliability of chillers declines.
In this article, we have prepared a chiller maintenance guide that covers all aspects of system maintenance - from daily checks to annual tune-ups. Follow the guidelines we have collected and you will ensure that your chiller runs smoothly and efficiently for many years to come. These include both the winter and summer periods.
Remember that a regular review of the unit's basic functions and readings will save you from many serious faults in the future.
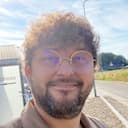
Articles author
Bartosz Kułakowski
CEO of Hosetech Sp. z o.o.
Bartosz Kulakowski is an industrial hoses and couplings specialist with over 10 years of experience. Bartosz has been present in the technical industry since 2013. He gained experience as a technical and commercial advisor in the sector of plastic conveyor belts, steel structures, industrial hoses, and connectors. Since 2016, he has specialized exclusively in hoses and connectors. In 2019 he opened his own business under the HOSETECH Bartosz Kulakowski brand and since July 2022 he has been the CEO of the capital company HOSETECH Sp z o. o. (LLC).
Table of Contents
Why is it worth maintaining chillers regularly?
Chiller maintenance checklist
Daily chiller maintenance checklist
Weekly chiller maintenance checklist
Monthly chiller maintenance checklist
Annual chiller maintenance checklist
How to maintain chillers in summer?
Remove dirt and debris
Clean the coils
Check condenser inlet filter
Clean and check panels and steel structure
Check for leaks
Analyse the system and chilled water
Plan maintenance and service
How to maintain chillers in winter?
Prevent freezing
Clean the coils and other parts of the system
Check for leaks
Check insulation
Set the maximum capacity
Check crankcase heaters and evaporator heaters
What are the benefits of regular chiller maintenance?
Cost savings
Energy efficiency
Extended service life
Improved efficiency and reliability
Safety
How often does a chiller unit need to be serviced?
Why is it worth hiring professionals for chiller maintenance?
FAQ
Is the chiller part of the HVAC system?
What is the ideal chiller temperature?
How does the chiller control the temperature?
Summary
See also other categories