Types of chillers - Which is right for your business?
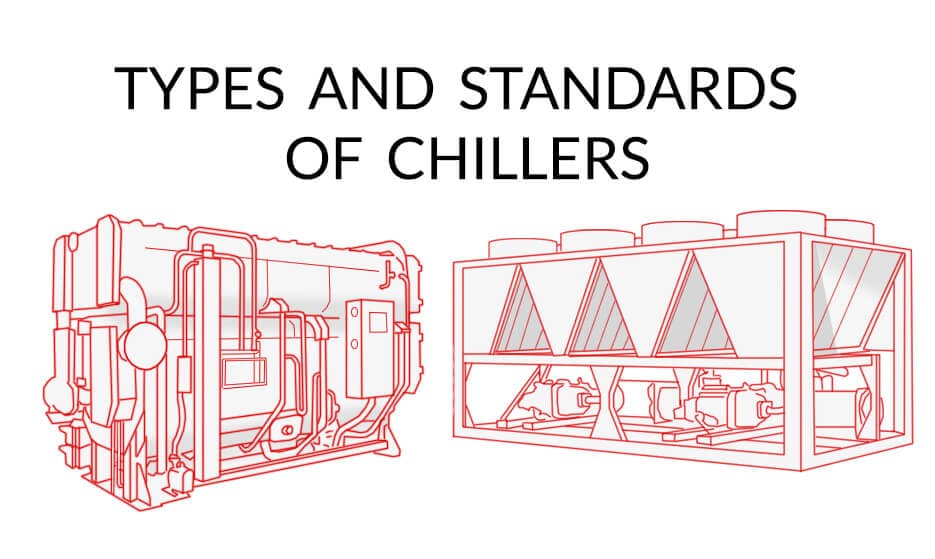
What are the types of chillers?
There are two main types of chillers:
- with a compressor (air- or water-cooled),
- absorption chillers.
Beyond this, there are many additional subcategories, e.g. by compressor technology or industrial application. Below we look at all types of chillers in more detail.
What are chillers with compressor?
Compressor chillers are chillers that use a compressor to pump refrigerant through the system. They are the most common type of machine.
The capacity of the compressor, and therefore the cooling capacity of the chiller, is measured in kilowatts (kW), horsepower (HP) or volume flow (m3/h, ft3/h). There are also different types of compressor. They can be hermetic (welded) or semi-hermetic (bolted).
Sometimes compressor chillers are combined with refrigeration dehumidifiers, which remove potentially harmful moisture from the cooled air from the machinery.
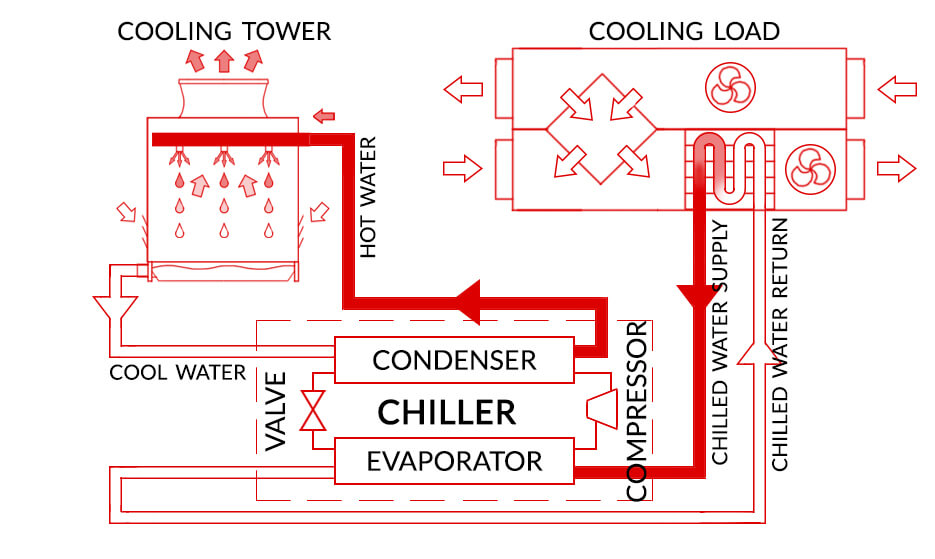
As we have already mentioned, compressor chillers are divided into two subcategories based on the method of cooling. You have a choice of devices:
- water-cooled,
- air-cooled.
We describe each of these below.
What are water-cooled chillers?
Water-cooled chillers are chillers that draw water into the evaporator, where heat is transferred from the water to the refrigerant. The water thus cooled goes through the main inlet to the tank, from where a pump distributes it to critical spaces using coolant hoses.
As it flows through each point in the system, the water absorbs heat from its surroundings.
This is stated by the second law of thermodynamics. Heat naturally passes from higher temperature areas to cooler areas.
Later, the water returns to the chiller where it cools down again. In this way, the process starts all over again.
However, in order to absorb more heat from the water in each cycle, the refrigerant must transfer the heat it absorbed previously somewhere. Therefore, the evaporator transports the heated low-pressure refrigerant to an engine-driven compressor.
The compressor increases the temperature and pressure of the coolant before sending it to the condenser.
In the condenser, the water that surrounds the refrigerant tubes absorbs its heat. It later enters the cooling tower, where it releases the excess heat.
As the refrigerant continues its cycle, an expansion valve (similar to a water bottle nozzle) reduces its temperature and pressure as the coolant flows back into the evaporator.
What are air-cooled chillers?
Air-cooled chillers are chillers that cool the condenser coil using a fan and cold air.
The refrigerant increases its temperature and pressure as it passes through the compressor. Later, it reaches the condenser where outside air is circulated by means of a fan. The condenser absorbs the heat of the refrigerant and discharges it outside.
Finally, the refrigerant returns to the evaporator via the expansion valve to restart the process.
Water-cooled chillers vs. air-cooled chillers
The main difference between water-cooled and air-cooled chillers is that water-cooled chillers are more efficient, especially for large cooling loads. They use water evaporation to dissipate heat, which is less energy-intensive than blowing air over a hot surface. In addition, water has a higher heat capacity than air, so it removes high temperatures more easily.
Therefore, water-cooled chillers will endure a higher load relative to the space they occupy. They are also more durable. As they are located inside a building, they deteriorate much more slowly.
However, chillers of this type need a cooling tower and a constant supply of clean water. In addition, they are large machines, so they take up a lot of space and (depending on the compressor technology) generate noise and vibration.
What's more, they cost more to install and maintain. In addition, they take up space in the building, which excludes some space from business use.
When it comes to air-cooled chillers, on the other hand, they are cheaper to install because they consist of fewer components. They also take up less space and can be located outside (e.g. on the roof), so they do not “steal” business space.
What's more, because of their simpler design, they also cost less to maintain.
However, air-cooled chillers do not have such a long service life because, due to their outdoor installation, they are exposed to the sun, rain, frost, snow, etc. This makes them deteriorate more quickly. In addition, their design is prone to damage, blockages or recirculation problems.
What are absorption chillers?
Absorption chillers are chillers that use the heat source instead of a compressor to move the refrigerant through the refrigeration system. The system design looks very similar. The only difference is that there is no compressor - in its place comes an absorber, a pump and a generator.
The thermodynamic cycle is powered by heat, which comes from steam, hot water or combustion. During it, refrigerant vapour is absorbed, resulting in the dilution of the absorber material.
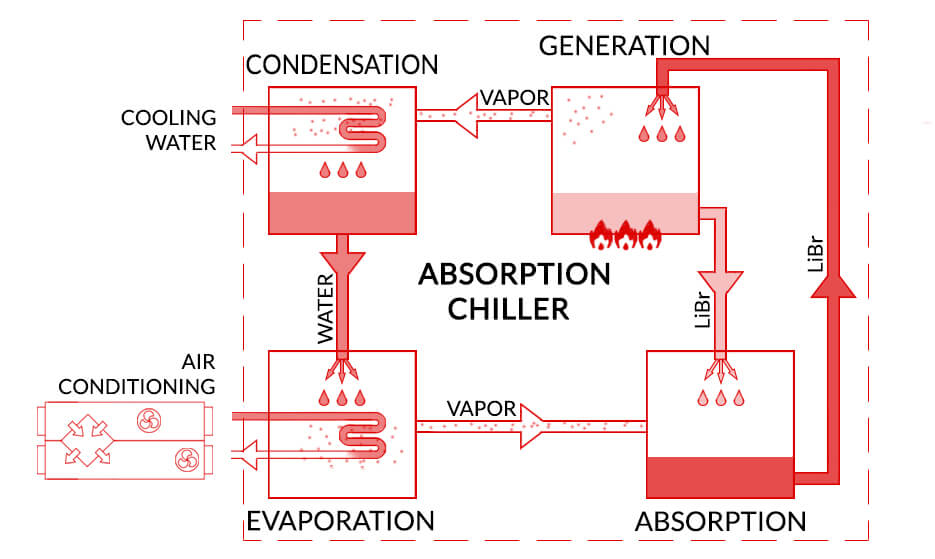
One of the most common absorbents in absorption chillers is lithium bromide combined with water as the refrigerant. However, some cooling systems use a combination of water and ammonia.
As for the heat source, it is sometimes a thermal waste from another unit, which increases energy efficiency.
It is worth noting that absorption chillers require much larger cooling towers than compressor versions. However, they are more energy efficient, especially if you have access to a cheap heat source or waste heat.
Even solar energy is used to operate absorption chillers in sunny climates.
What are glycol chillers?
Glycol chillers are chillers that use glycol as the cooling medium. Glycol chillers are the heart of the refrigeration system, which is commonly used in breweries and wineries. They are perfect for maintaining the right temperature for food products as they offer a reliable control mechanism.
The glycol chillers consist of a compressor, evaporator, condenser, throttling element and electrical control system.
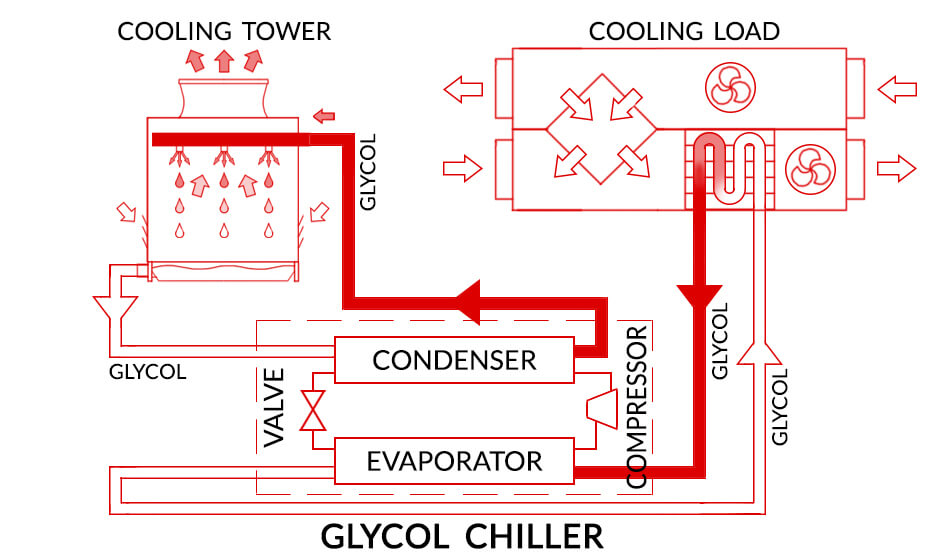
The chiller refrigerant absorbs the heat energy from the process and usually turns into a gas. In this form, it enters the condenser, which removes the heat through condensation. In doing so, it condenses the refrigerant back into a cooler gas-liquid mixture, which again goes to the heating source and starts the whole cycle again.
As individual wineries and breweries do not have exactly the same needs, there is no one-size-fits-all glycol system that is suitable for all locations and applications.
When choosing the design of a glycol chiller, many factors come into play, so the individual solution for the company is of paramount importance.
Division of chillers by mobility
In addition to the basic division, chillers also come in two mobility versions. The chillers available to you are:
- mobile,
- central.
Below we look at each of these.
What are mobile chillers?
Mobile chillers are chillers with have a lower capacity (up to 40 refrigeration tonnes), simpler design and lower installation cost. As they have wheels, they are easy to transport.
You will connect them with flexible hoses and start them up without too much trouble.
What's more, mobile chillers usually provide a consistent heat exchange capacity, measured in tonnes. They are best suited where a particular processing piece of equipment requires a flow of cooling water at a temperature that is significantly different from other equipment.
Mobile chillers contain a single circuit or heat transfer zone. They are therefore well suited for use in processes where cooling requirements remain relatively constant.
As a rule, mobile chillers operate most energy efficiently when the cooling load closely matches their rated capacity.
What are central chillers?
Central chillers are chillers that feature higher efficiency, more complex design, higher energy efficiency, and more costly installation.
The key advantage of a central chiller system is that it will successfully handle many large and variable process loads that require chilled water at approximately the same temperature.
In addition, these types of chillers have functions for modulating their capacity. You will match it to your changing production cooling needs.
One central chiller will provide better overall performance than multiple portable chillers with the same total efficiency.
Wondering what will be better: one central system or multiple mobile units? And the answer depends on the overall combination of cooling needs in the facility.
As a general rule, if 80% or more of the materials are processed in one temperature range, a central cooling system will meet the needs with lower operating tonnage, less floor space and probably less frequent daily maintenance.
If, on the other hand, materials processing requires widely varying temperatures, appropriately sized portable chillers will be more efficient.
Sometimes companies opt for a mix of both solutions. They have a central chiller but also support with mobile units.
Division of chillers by compressor technology
Chillers are also divided into several types depending on what type of compressor they use. Below we look at the most popular of these.
What are centrifugal chillers?
Centrifugal chillers are chillers that operate by rotating impellers that compress the refrigerant and pump it into the circulation.
Most centrifugal chillers are water-cooled (it is extremely rare to find a centrifugal compressor in an air chiller).
These types of compressors are most often used for medium to large cooling loads (typically 150 to 6,000 tonnes of cooling). They offer high efficiency in a compact design, but typically require a full load to operate effectively.
What are chillers with piston compressor?
Chillers with piston compressor are chillers that use a piston and chamber to compress the refrigerant.
Piston compressors appear in both water- and air-cooled chillers. They work best for small to medium loads - from 50 to 500 tonnes of refrigeration.
However, this is an old technology that manufacturers are using less and less.
What are scroll compressor chillers?
Scroll compressor chillers are chillers which operation is based on the use of two scroll plates (one stationary and one rotating) to compress the refrigerant. Scroll compressors are used in both air- and water-cooled chillers.
Scroll chillers are best suited for small to medium loads - from 40 to 400 tonnes of refrigeration.
What are rotary screw driven compressor chillers?
Screw driven compressor chillers are chillers which rotary screw compressors use two interlocking scroll rotors to compress the refrigerant.
Rotary screw driven compressors are also used in both types of chillers (water-cooled and air-cooled). They are best suited for small to medium cooling loads. They are usually available in capacities from 70 to 600 refrigeration tonnes.
What are turbocor compressor chillers?
Turbocor compressor chillers are chillers which method of operation is based on two rotating impellers that compress the refrigerant. What's more, the turbocor compressor needs no oil.
Turbocor compressors are the most versatile technology. They are suitable for both water- and air-cooled chillers. In addition, they will work well in small and large buildings.
The load range for this type of compressor ranges from 60 to 1,500 refrigeration tonnes.
Dividing chillers by area of application
We also divide chillers according to their intended use. In this respect, we distinguish between several main industries.
What are chillers for food and beverages?
Chillers for food and beverages maintain the optimum temperature of food and beverage products. It is crucial, as it directly affects their safety and quality.
Chillers work well in many circumstances - whether it is to cool liquids such as milk or juice or to keep food products fresh.
The industry has various types of equipment available, including air-cooled and water-cooled units. And when it comes to the size of the chiller, it depends on the volume of food products and the temperature requirements.
What are medical chillers?
Medical chillers are chillers play an important role in maintaining optimum temperature levels of sensitive medical equipment e.g. MRI machines and CT scanners.
With their precise temperature control, chillers ensure consistent performance and prevent overheating, which can adversely affect equipment and patient safety. Chillers also help to maintain sterility as they precisely control humidity levels.
What are HVAC chillers?
HVAC chillers are key components in various industrial and commercial applications (e.g. hospitals, data centres and manufacturing plants). They cool water or other fluids to provide air conditioning or process cooling.
Chillers range in size from small units that fit under a desk to large systems that require an entire room. Choosing the right size and type of chiller will provide companies with better efficiency and lower energy costs. It will also extend the life of their HVAC mechanical systems.
What are chillers for metalworking industry?
Chillers for metalworking are chillers that ensure high-quality plating and chemical processes. Precise temperature control is necessary to avoid corrosion, pitting and other defects that result from abnormal environmental conditions.
When selecting a metalworking chiller, it is important to consider the size of the application, the temperature range required and the type of chemicals used.
What are industrial chillers?
Industrial chillers are chillers that are used in a wide range of commercial operations, where they are used to cool large machinery and equipment. Thus, they provide them with optimum efficiency.
On the market you will find various industrial chillers (including air-cooled and water-cooled). With the right plan and proper maintenance, they will provide you with reliable cooling for many years.
What are chillers for plastics processing?
Chillers for plastics processing maintain precise temperature control is crucial in the plastics industry. The right cooling system will improve the efficiency and quality of production, while reducing energy costs.
You can choose between air- and water-cooled chillers. They meet different requirements depending on individual needs.
FAQ
Is a chiller a condenser?
No, a chiller unit is not a condenser. The condenser is one of the system components in the chiller. It is responsible for removing heat from the refrigerant via the evaporator.
What is the most commonly used type of chiller?
The most common type of chiller is the compressor version. Depending on your needs and system load, you have chillers with different types of compressor, such as centrifugal, scroll or rotary screw. Each of these has its pros and cons.
Which type of chiller is the most efficient?
The most efficient type of chiller is the water-cooled version with a centrifugal compressor. It guarantees the highest operating efficiency at full load. Performance indeed drops off when partially loaded, but with the help of additional improvements you will reduce this compressor weakness.
Summary
As you can see, we distinguish between many different chillers. Chillers are divided not only by the type of design and cooling method but also by mobility, the technology used or the industry purpose.
This is why choosing the right chiller can be difficult.
Each chiller has its pros and cons, which you should consider before deciding on a purchase. Especially since the installation of a chiller system involves a significant initial cost.
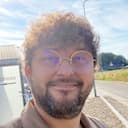
Articles author
Bartosz Kułakowski
CEO of Hosetech Sp. z o.o.
Bartosz Kulakowski is an industrial hoses and couplings specialist with over 10 years of experience. Bartosz has been present in the technical industry since 2013. He gained experience as a technical and commercial advisor in the sector of plastic conveyor belts, steel structures, industrial hoses, and connectors. Since 2016, he has specialized exclusively in hoses and connectors. In 2019 he opened his own business under the HOSETECH Bartosz Kulakowski brand and since July 2022 he has been the CEO of the capital company HOSETECH Sp z o. o. (LLC).
Table of Contents
What are the types of chillers?
What are chillers with compressor?
What are absorption chillers?
What are glycol chillers?
Division of chillers by mobility
Division of chillers by compressor technology
Dividing chillers by area of application
FAQ
Is a chiller a condenser?
What is the most commonly used type of chiller?
Which type of chiller is the most efficient?
Summary
See also other categories