Dry cooler – definition, structure, configurations, applications – Complete guide
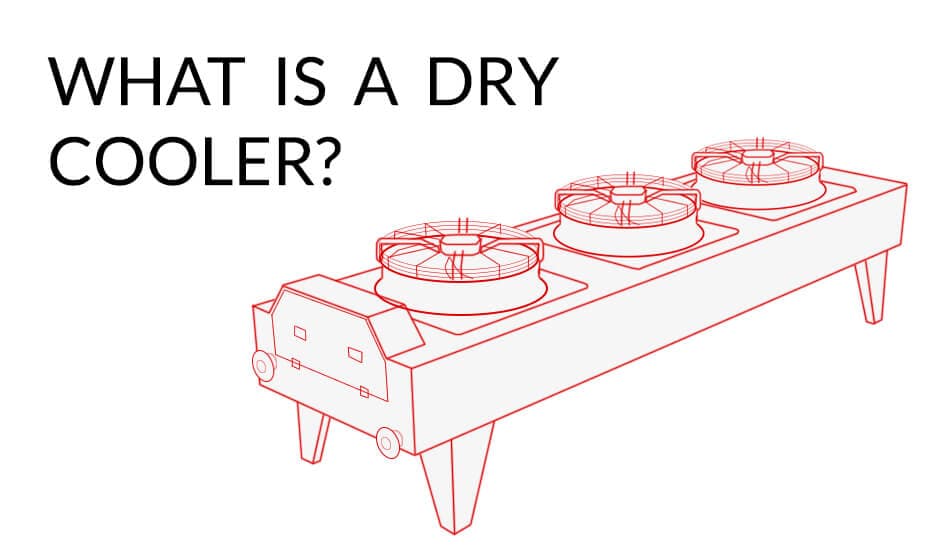
What is a dry cooler?
A dry cooler is a cooling device that uses air to regulate the process temperature. The cooling is based on the principles of sensible heat rejection.
A typical system requires refrigerant to enter the dry cooler from the associated process. This is where it exchanges the accumulated heat with the air circulating inside.
Dry coolers have fans that draw in air from outside to maintain the thermal exchange process. To ensure efficient cooling, an adequate temperature difference must be maintained between the cooling medium and the air.
Typically, a minimum difference of 5 degrees Celsius is sufficient.
Dry coolers are often used where water is scarce or its use is prohibited due to environmental regulations. They are also used in industrial processes that require cooling to maintain optimum working conditions.
How is the dry cooler constructed?
The dry cooler is made up of a number of essential components. These are:
- housing with built-in pipes for the flow of the cooling medium,
- fans,
- plate fin heat exchangers.
The principle of the whole thing is very simple. The refrigerant flows through the dry cooler, where it exchanges the accumulated heat with the air, which is forced in by the fans. As a result, it returns to the process cooled.
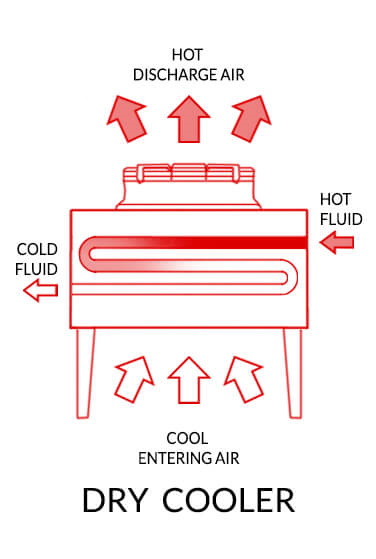
What are the dry cooler configurations?
There are three configurations of dry coolers in cooling systems:
- direct dry cooling,
- indirect dry cooling,
- natural draft condenser.
Below we explain how each of them works.
What is direct dry cooling?
Direct dry cooling is a configuration that directly condenses the exhaust stream from the steam turbine and returns the condensate without loss of water. This means that the vapour changes to a liquid state directly inside the air-cooled finned tubes.
An intermediate surface condenser is not necessary.
Such systems are used in industrial processes, public utilities, as well as small and large power plants.
What is indirect dry cooling?
Indirect dry cooling is the configuration that combines a dry cooling tower (IDCT) with a surface or evaporative condenser. They are ideal for high-capacity condensing units.
Their steel or concrete housing prevents hot air recirculation. This reduces the need for additional power and the number of mechanical components.
What is natural draft condenser?
A natural draft condenser (NDACC) is an air-cooled condenser (ACC) that uses a natural draft tower instead of fans. This design reduces electricity requirements.
Which applications are dry coolers used for?
The most common applications of dry coolers include:
- data centres,
- office buildings,
- hospitals/medical office buildings,
- industrial/process systems,
- heat exchange/recuperation,
- energy generation,
- induction cooling.
Dry coolers are used in many types of buildings and in almost the entire HVAC industry. Due to their properties, dry coolers play a significant role in increasing building efficiency.
What are the advantages of dry coolers?
The main advantages of dry coolers are:
- easy installation and set-up;
- generally low operating costs after installation;
- convenient separation of components allows operators to save floor space for other equipment;
- a constant supply of water is not needed, so there are no supply and disposal concerns;
- ability to operate all year round, even in cold environments;
- heat generated can be diverted directly to other processes, reducing energy losses and improving overall efficiency.
What are the disadvantages of using dry coolers?
The disadvantages of using dry coolers are:
- the requirement for regular inspection (or an automated chiller monitoring system) to ensure that the amount of coolant does not fall below
- the required level; the cost of additional components adds to the total expenditure on the set-up.
Dry cooler vs chiller
The main difference between dry coolers and chillers is in the form of thermal exchange. For dry coolers, a thermal exchange takes place by drawing in outside air and circulating it over pipes with a coolant (usually water or a mixture of water and glycol). The cooled fluid then passes through a heat exchanger, which combines with the associated process. The excess temperature is transferred to the coolant. This in turn, heated, returns to the dry cooler, where the cycle starts again.
Note that the dry cooler does not have a standard cooling unit to remove heat. Instead, it uses fans. They draw in ambient air and thus cool the heated medium.
Chillers, on the other hand, have refrigeration units (often in combination with heat exchangers) in their system configuration. They use the refrigerant and reduce its temperature using air or water in the condenser.
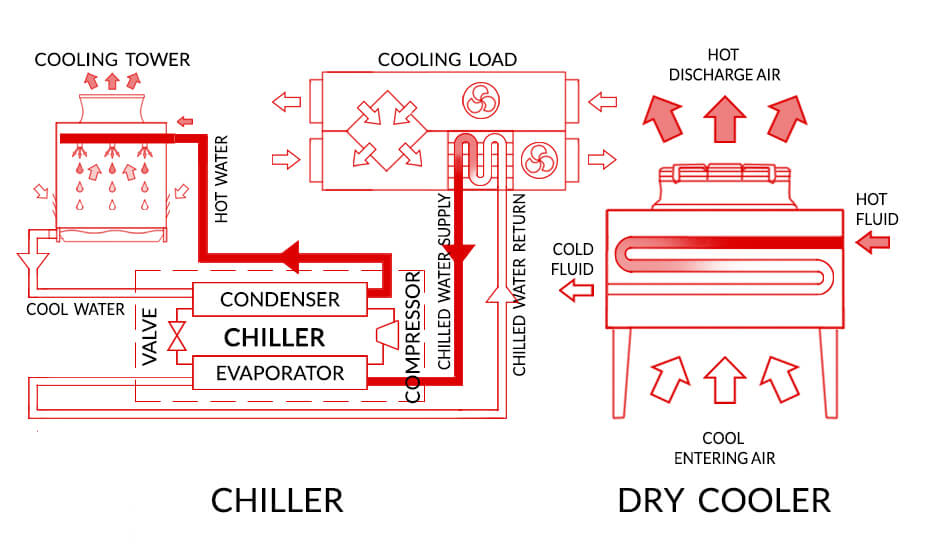
Chillers primarily have the advantage of better temperature control and greater heat reduction capabilities. In addition, they are long-lived and energy-efficient.
On the other hand, compared to dry coolers, chillers are clearly more costly to maintain. So is the initial installation of the system in a plant.
Nevertheless, both dry cooler and chiller offer benefits when used under the right conditions.
Dry cooler vs cooling tower
The main difference between a dry cooler and a cooling tower is the complexity of construction. Dry coolers are characterised by a simple and robust design that includes a heat exchanger (usually finned tubes or microchannel coolant hose) and fans that direct airflow through it to cool the water or glycol solution. Dry coolers are most often available with horizontal or vertical airflow.
The heat dissipation capacity is usually up to 1 MW, although high-capacity versions are also available on the market.
Modern designs may have additional components such as pre-cooling systems (both adiabatic spray and wetted pads). They allow the process fluid to be cooled below the dry thermometer temperature.
On the other hand, we have the cooling tower, whose structure is much more sophisticated. This includes:
- nozzles that spray hot water uniformly onto the heat exchanger,
- fans that direct ambient air through the cooling tower,
- droplet eliminators that prevent water from escaping with the air,
- chilled water tank.
Air flows from the bottom of the tower (counterflow type tower) or perpendicular to the direction of water flow (crossflow type tower).
The cooling tower relies on the latent heat of evaporation of the water to exchange terminator with the air stream that flows through it. It can reduce the temperature of the process water below ambient temperature.
A dry cooler, on the other hand, only reduces the water temperature to ambient temperature. However, better cooling is possible if you use additional solutions. This includes, for example, adiabatic pre-cooling of the inlet air.
Wet cooling towers operate efficiently in hot and dry climates, but when the ambient air becomes humid, their efficiency decreases. In contrast, the efficiency of dry coolers is not affected by humidity, but depends on the ambient temperature.
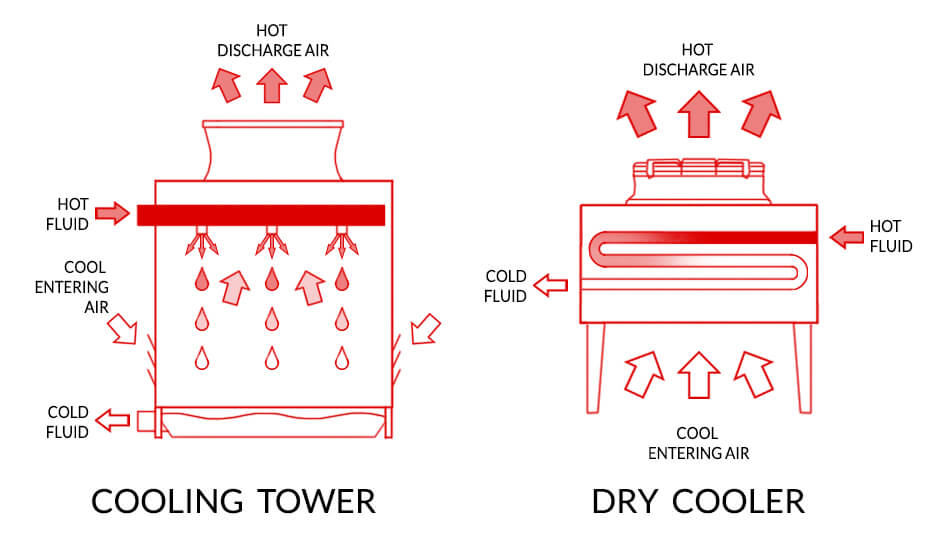
To summarise, cooling towers offer greater temperature reduction, better cooling capacity and are suitable for hot climates. However, their initial installation is much more costly, as is subsequent maintenance.
Summary
Dry coolers are a versatile and efficient way to cool process fluids in buildings and almost all HVAC applications. You can buy them in a variety of sizes and configurations to meet the specific needs of different applications.
Not only are they cost-effective, but they can also help reduce your company's environmental impact.
If you're looking for a way to cool process fluids efficiently and sustainably, a dry cooler is the answer. However, remember that when you are choosing a unit for your needs, you should consider the key points discussed in the article.
With careful planning, you will install a dry cooler that is up to the task and will give you years of reliable service.
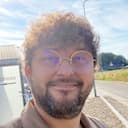
Articles author
Bartosz Kułakowski
CEO of Hosetech Sp. z o.o.
Bartosz Kulakowski is an industrial hoses and couplings specialist with over 10 years of experience. Bartosz has been present in the technical industry since 2013. He gained experience as a technical and commercial advisor in the sector of plastic conveyor belts, steel structures, industrial hoses, and connectors. Since 2016, he has specialized exclusively in hoses and connectors. In 2019 he opened his own business under the HOSETECH Bartosz Kulakowski brand and since July 2022 he has been the CEO of the capital company HOSETECH Sp z o. o. (LLC).
Table of Contents
What is a dry cooler?
How is the dry cooler constructed?
What are the dry cooler configurations?
What is direct dry cooling?
What is indirect dry cooling?
What is natural draft condenser?
Which applications are dry coolers used for?
What are the advantages of dry coolers?
What are the disadvantages of using dry coolers?
Dry cooler vs chiller
Dry cooler vs cooling tower
Summary
See also other categories