How is a chiller constructed? Components of a water chiller
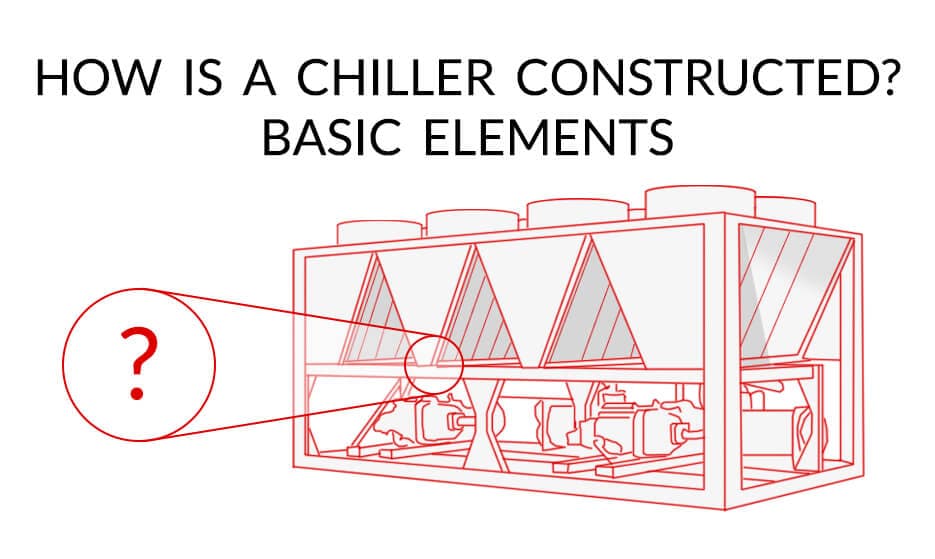
How is a chiller constructed?
A chiller is constructed from a number of components, among which are:
- condenser,
- compressor,
- evaporators,
- thermal expansion valves,
- power supply,
- control panel,
- water boxes.
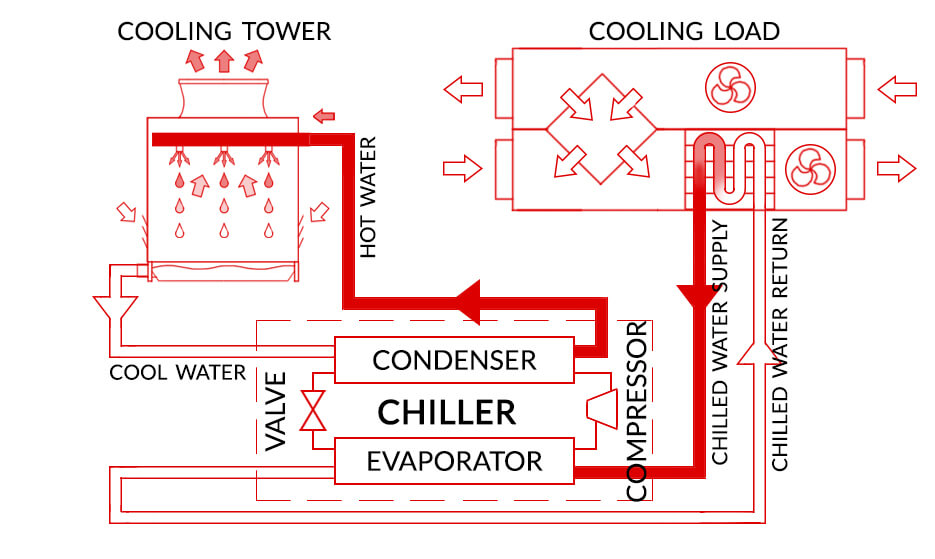
Read on and you will learn more about each of these.
What is a condenser?
The condenser is a chiller part that removes heat from the refrigerant that has reached the evaporator. The condenser is located after the compressor, but before the expansion valve.
There are two main types of condenser:
- air-cooled,
- water-cooled.
Water-cooled condensers continually repeat the circulation of “condenser water” between the cooling tower and the condenser.
The hot refrigerant that enters the condenser from the compressor transfers its heat to the water. In turn, this water is directed into the cooling tower and leaves the building. Refrigerant and water do not mix, as they are separated by the pipe walls. The water flows inside the pipe and the refrigerant flows outside.
The condensers in air-cooled chillers work slightly differently, as they do not use a cooling tower. Instead, they blow air through exposed pipes, through which the refrigerant flows this time.
What is a chiller compressor?
The compressor is the main drive that creates the pressure difference to move the refrigerant through the system.
There are various refrigerant compressor designs, the most popular of which are:
- centrifugal,
- rotary screw,
- scroll,
- piston.
Each type has its own pros and cons.
The compressor is always located between the evaporator and the condenser. In addition, it is usually subject to partial insulation and has a driving force in the form of an electric motor, which is either internally or externally mounted.
Compressors can sometimes be very noisy. It is usually a steady, deep, rumbling sound with an overlapping high note. Therefore, noise protection earmuffs should be worn in the vicinity of the refrigeration unit.
What is an evaporator?
The evaporator is a chiller part that collects unwanted heat from the building and transfer it to the refrigerant so that it can be sent to the cooling tower and rejected. The evaporator is is located between the expansion valve and the compressor
The water cools as the refrigerant takes up the heat. This “chilled water” is then pumped into the building to provide air conditioning. It later returns to the evaporator, carrying with it unwanted high temperatures from the rooms/processes.
What is the thermal expansion valve?
The expansion valve is a chiller part that expands the refrigerant, which reduces its pressure and increases its volume. This makes it easier to dissipate unwanted heat in the evaporator. The expansion valve is located between the condenser and evaporator
There are many different types of expansion valves, the most popular of which are:
- thermal expansion valve,
- pilot operated thermal expansion valve,
- electronic expansion valve,
- fixed orifice expansion valve.
How is the chiller powered?
Chiller is powered by the power unit is either mounted directly to the chiller or separately on the wall of the plant room (with power cables running to the unit).
The purpose of the power unit is to control the flow of electricity to the chiller. It typically includes a starter, circuit breakers, speed controller and power monitoring equipment.
What is the purpose of the chiller control panel?
The purpose of the chiller control panel is to monitor various aspects of the unit's performance and control them by making adjustments.
In addition, the control panel generates alarms for the engineering teams and safely shuts down the system to prevent damage to the unit. The control panel is usually mounted on the chiller.
BMS connections are also usually present to allow remote control and monitoring.
What are water boxes?
Water boxes are an element of the chiller that directs the flow and also to separates the input and output.
Depending on the number of channels in the evaporator and condenser, water boxes have single or double flanged inlet or outlet ports, or are completely covered and simply redirect the flow back to the next channel. Water boxes are mounted on evaporators as well as condensers of water-cooled chillers.
How are chillers made?
Chillers are created during the manufacturing process, which consists of 4 phases:
- design phase,
- production phase,
- assembly phase,
- testing phase.
We look at each of these in more detail below.
What is a chiller design phase?
During the design phase, a group of experienced engineers develops a scheme that will provide the best performance in a given location. To do this, the specialists consider several important issues such as:
- industry,
- working environment,
- budget,
- individual customer preferences.
On this basis, an original design is created, the configuration of which takes into account the unique application conditions of a particular plant. Therefore, different chillers may vary in size, mechanics and functions.
What is chiller production phase?
During the chiller production phase, the manufacturer processes the material, i.e. cuts and bends it to shape. Usually a professional production line with lasers, hydraulic presses and other similar machines is used for this.
What is chiller assembly phase?
When all the chiller components are ready, the manufacturer proceeds to assemble them. The parts are securely joined together using rivets, bolts and anchors.
The key components of the machine, which we described above, are then fitted to the finished framework.
Once everything is in place, production moves on to the piping stage, i.e. the installation of the relevant pipes, refrigerant coolant hoses and smaller components. At the same time, another specialist takes care of the wiring and installation of the control panel.
What is chiller testing phase?
Before the chiller leaves the factory, it undergoes a series of quality tests.
First, the refrigeration circuit is filled with helium to check for leaks. Helium is a smaller molecule compared to refrigerants. If it is not leaking, the larger particle will also remain in the circuit.
Later, the fluid circuit is once again checked for leaks by increasing the water pressure in the tank, pumps and piping.
The test bench is then modified to simulate the expected heat load that the chiller will experience during operation.
If there are no objections, the manufacturer fills the unit with refrigerant and adds the appropriate fluid to the circuit. Then it is time to start the chiller. The whole thing is supervised by a technician who checks the operation of each component. If necessary, he makes the necessary adjustments.
When the chiller is operating in accordance with specifications, it is given a data label which contains all the relevant information for the installer.
Take into account, however, that the testing phase may vary depending on the manufacturer.
What are the safety considerations in the construction of chillers?
Safety considerations in the construction of chillers primarily concern:
- risk of electric shock,
- refrigerant leakage,
- extreme temperatures,
- too much/too little pressure.
You can read more about each consideration below.
Risk of electric shock
As the device uses relatively large amounts of electricity, there is always a risk of electrocution. It is therefore important that the electrical installation is properly insulated.
In addition, every employee should take the necessary minimum precautions when operating the chiller.
Refrigerant leakage
Some coolants present in chillers pose a serious environmental risk to workers if a leak occurs. This is why most units have internal sensors that monitor the amount of coolant in the circuit. If a leak occurs, the system automatically blocks the flow.
Workers should also be well versed in how to stop the chiller in the event of a leak.
Extreme temperatures
Another risk to chiller operation and employee health is extreme temperatures. The unit often generates a great deal of heat, which poses a serious risk. On the one hand, it leads to burns if workers are careless, and on the other hand, it can even cause a fire. Therefore, contact with hot surfaces should be kept to a minimum.
Moreover, there is also a danger associated with too low a temperature. In some cases, too much cold poses the risk of the fluid freezing, which can lead to circuit damage.
This is why chiller systems have appropriate sensors to detect excessive temperature changes.
Too much/too little pressure
A sudden increase or decrease in compressor pressure can lead to serious damage to the whole chiller structure, resulting also in a dangerous leak of toxic coolant.
That's why the chiller system also has pressure sensors. They interrupt the system if they detect any abnormalities.
FAQ
What is the best compressor for a chiller?
The best compressor for a chiller is a centrifugal compressor if you are dealing with large installations of more than 750 cooling tonnes. However, bear in mind that this type of compressor is only suitable for water-cooled chillers.
For small systems (up to 150 refrigerated tonnes), a piston compressor will work better. On the other hand, between 150 and 750 refrigerated tonnes, it is worth thinking about multi-piston or rotary screw compressors.
Is a chiller a boiler?
No, a chiller is not a boiler. Boilers use heated or evaporated liquid to heat residential buildings or for other industrial and commercial applications. Chillers, on the other hand, use an evaporative or absorption cooling cycle to remove heat from the liquid to cool equipment or large facilities.
Do chillers have heat pumps?
Yes, in a sense, chillers have heat pumps because the two units are very similar in design. The only difference is that a chiller is used to remove heat from a space or process stream, making it cooler by expelling heat into the environment. In contrast, a heat pump extracts heat from the environment and uses it for heating.
Summary
You already know that the main components of a chiller are the condenser, compressor, evaporators and expansion valves. Adequate power supply, control panel and water boxes are also of paramount importance.
The correct operation of each component is essential for the unit to have the highest performance and provide a high level of safety.
Therefore, a professional production process and the following regular inspection of the device's condition also play a key role. With the latter, you will make sure that the chiller is in good condition and does not cause any problems, which in the long run will save you from unnecessary expenses.
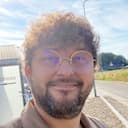
Articles author
Bartosz Kułakowski
CEO of Hosetech Sp. z o.o.
Bartosz Kulakowski is an industrial hoses and couplings specialist with over 10 years of experience. Bartosz has been present in the technical industry since 2013. He gained experience as a technical and commercial advisor in the sector of plastic conveyor belts, steel structures, industrial hoses, and connectors. Since 2016, he has specialized exclusively in hoses and connectors. In 2019 he opened his own business under the HOSETECH Bartosz Kulakowski brand and since July 2022 he has been the CEO of the capital company HOSETECH Sp z o. o. (LLC).
Table of Contents
How is a chiller constructed?
What is a condenser?
What is a chiller compressor?
What is an evaporator?
What is the thermal expansion valve?
How is the chiller powered?
What are water boxes?
How are chillers made?
What is a chiller design phase?
<a></a>What is chiller production phase?
What is chiller assembly phase?
What is chiller testing phase?
What are the safety considerations in the construction of chillers?
Risk of electric shock
Refrigerant leakage
Extreme temperatures
Too much/too little pressure
FAQ
What is the best compressor for a chiller?
Is a chiller a boiler?
Do chillers have heat pumps?
Summary
See also other categories