NBR rubber - definition, types, properties, applications
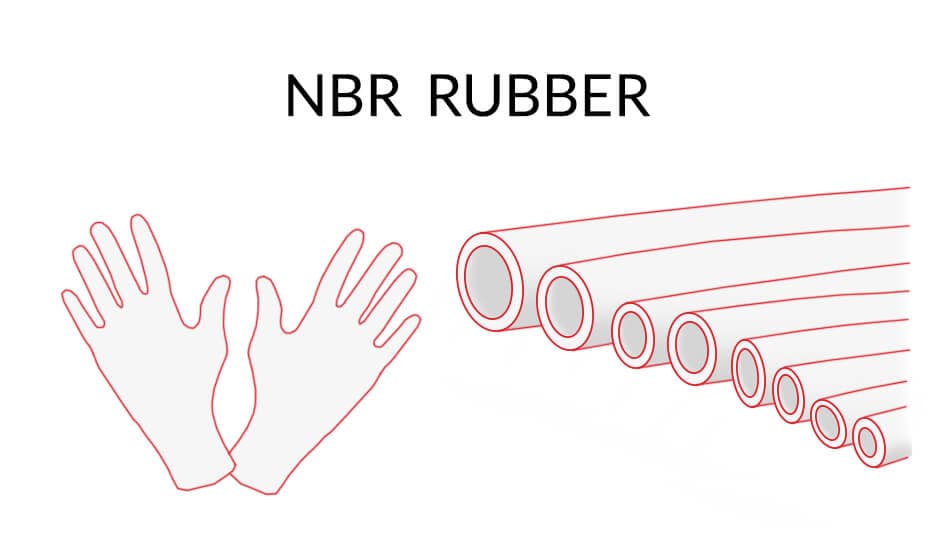
NBR rubber is a synthetic rubber compound made from acrylonitrile and butadiene, known for its natural resistance to oils, fuels, water and many chemicals. Generally speaking, it is a great, versatile product in the world of hydraulics and pneumatics.
In this article, we will explore its properties, applications, as well as its advantages and disadvantages.
What is NBR rubber?
NBR rubber is a synthetic rubber, a copolymer of acrylonitrile (ACN) and butadiene. Although the physical and chemical properties of the material vary depending on the composition, this particular type of synthetic rubber is remarkable for its resistance to oil, fuel and other chemicals.
The general rule of thumb is that the more ACN in the polymer, the higher the oil resistance, but the lower the flexibility of the material.
Is NBR a natural rubber?
No, NBR is not natural rubber. It is a synthetic rubber made from a copolymer of acrylonitrile and butadiene
What does NBR stand for?
NBR stands for "Nitril Butadiene Rubber", or nitrile butadiene rubber. You will also find other terms for this polymer on the market, such as:
- acrylonitrile butadiene rubber,
- oil-resistant rubber,
Chemically speaking, what we are dealing with here is a copolymer of butadiene and acrylonitrile.
How is NBR rubber produced?
NBR rubber is produced using an emulsion polymerisation system. For this, the following ingredients are required:
- water,
- emulsifier/soap,
- monomers (butadiene and acrylonitrile),
- radical generating activator,
- other additives.
All are inserted into the polymerisation vessels.
During the emulsion process, a polymer latex is formed. It later coagulates with various materials (e.g. calcium chloride, aluminium sulphate) to turn it into a rubber crumb. This in turn is dried and pressed into bales.
It is worth noting that some speciality products are packaged in crumb form.
Most NBR manufacturers produce at least 20 conventional varieties of the elastomer. However, there are also some who now offer more than 100 grades of this rubber.
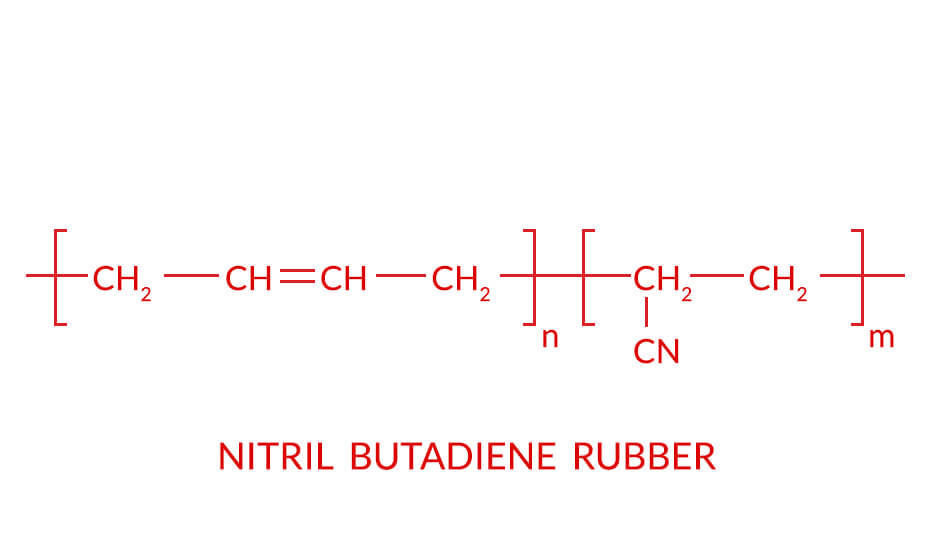
What are the ingredients of NBR?
The ingredients of NBR are butadiene and acrylonitrile. The acrylonitrile content in commercial products varies from 18% to 50%. The rubber may also have other additives that modify its properties.
NBR manufacturers use different polymerisation temperatures to produce "hot" and "cold" polymers. The ratio of acrylonitrile (ACN) and butadiene (BD) is adjusted for oil and fuel resistance and contact with low temperatures.
You will also find specialised NBR polymers on the market that contain a third monomer (such as divinylbenzene or methacrylic acid).
Finally, it is worth adding that some NBR elastomers are hydrogenated to reduce the chemical reactivity of the polymer backbone. This significantly improves the material's resistance to heat.
Each modification contributes to a change in unique properties.
What types of NBR rubber are there?
The most common types of NBR rubber are:
- cold-polymerised NBR,
- hot-polymerised NBR,
- cross-linked hot-polymerised NBR,
- carboxylated nitrile,
- hydrogenated nitrile – HNBR rubber,
- NBR bonded with an antioxidant.
You can read more about them below.
Cold-polymerised NBR
The current generation of cold NBR includes a wide range of compositions. Acrylonitrile content ranges from 15% to 51%. Mooney values range from very hard (110) to flowing liquids - with 20-25 as the lowest practical limit for solid material.
They are produced using a wide range of emulsifier systems, coagulants, stabilisers, molecular weight modifiers and chemical compositions. Third monomers are added to the polymer backbone to provide advanced performance.
Each variety provides a specific function.
Cold NBR rubber is polymerised over a temperature range of 5°C to 15°C (depending on the desired balance of linear and branched configuration). Lower polymerisation temperatures yield more linear polymer chains.
Reactions are carried out in processes commonly known as continuous, semi-continuous and batch polymerisation.
Hot-polymerised NBR
Hot-polymerised NBR rubber is polymerised in a temperature range of 30°C to 40°C. This process forms highly branched polymers. This structure provides good adhesion and strong bonding in adhesive applications. Physically entangled branched polymers also feature significantly improved tensile strength at higher temperatures.
The natural resistance to melting makes hot polymers excellent candidates for compression moulding and sponge production. Other applications include thin-walled or complex extrusions where shape retention is important.
Cross-linked hot-polymerised NBR
Cross-linked hot NBR rubber is characterised by branched polymers that are further cross-linked by the addition of a bifunctional monomer. These products are typically used in moulded parts to provide sufficient moulding force or back pressure to eliminate trapped air.
Another application is to provide greater dimensional stability or shape retention in extruded and calendered products.
This leads to more efficient extrusion and vulcanisation of parts with complex shapes, as well as better release from calender rolls.
These NBR plastics also provide dimensional stability, impact resistance and flexibility for PVC modifications.
Carboxylated nitrile - XNBR rubber
XNBR rubber is created by adding carboxylic acid groups to the NBR polymer backbone, significantly altering its processing and curing properties. The result is a polymer matrix with significantly increased strength (measured by improved tensile, tear, modelling and abrasion resistance).
Negative effects include lower compressive strength, water resistance, as well as lower resilience and loss of some properties at low temperatures.
Hydrogenated nitrile – HNBR rubber
Hydrogenated butadiene nitrile rubber is produced by hydrogenating NBR. This results in the removal of olefin groups, which are susceptible to degradation by various chemicals as well as ozone. The hydrogenation degree also determines the type of vulcanisation that can be applied to the polymer.
HNBR rubber is renowned for its physical strength and retention of properties after prolonged exposure to heat, oil and chemicals.
It is commonly used to manufacture o-rings for automotive air conditioning systems. Other applications include timing belts, shock absorbers, diaphragms and seals, among others.
NBR bonded with an antioxidant
Nitrile rubbers are also available with an antioxidant polymerised in the polymer chain. The aim is to provide additional protection for the NBR during prolonged fluid handling or cyclic exposure to fluids and air.
When mixing with highly reinforcing carbon black, the chemical reactivity between the polymer and pigment can limit the potential for hot air ageing. Furthermore, the abrasion resistance is better compared to conventional NBR (especially at elevated temperatures).
This type of NBR was also found to have excellent dynamic properties.
What does NBR 70 stand for?
NBR 70 stands for nitrile butadiene rubber, which is a synthetic copolymer of butadiene and acrylonitrile. The number 70, on the other hand, refers to the Shore hardness of the rubber, which is a measure of its resistance to indentation. A Shore hardness of 70 is considered to be medium hard.
What are the properties of NBR rubber?
The properties of NBR rubber are as follows:
- Low resistance to weathering and ozone (PVC compound is an exception);
- High resistance to cracking;
- Resistance to oils and petrol;
- Resistance to aliphatic hydrocarbons;
- Resistance to light fuel oils and diesel fuels;
- High resistance to non-flammable hydraulic fluids (HSA, HSB: oil/water emulsions, HSC: polyglycol/water mixtures);
- No reaction in contact with acids and bases diluted at not too high temperatures;
- Unstable in contact with aromatic and chlorinated hydrocarbons;
- No resistance to HSD (polyester and chlorinated hydrocarbons);
- No resistance to brake fluids containing glycols.
Depending on the number of compounds used and the variation of their percentage in the compound, the manufacturer can manipulate the rubber's resistance to oils and low temperatures at will.
NBR is also highly commended for its durability in the presence of alcohols and aqueous salt solutions. When it comes to water temperature, it will perform well in conditions up to 60°C.
However, rubber is not very resistant to silicone-containing oils and greases, glycol-based brake fluids and HFD hydraulic fluids. The rubber will also not be resistant to concentrated acids and alkalis. Esters can also damage the structure of NBR.
Is NBR rubber a safe material?
NBR rubber is generally considered to be a safe material. It does not contain any components that could cause health hazards such as skin or mucous membrane irritation. The rubber is stable and non-volatile under normal conditions. Therefore, there is no significant health risk in standard industrial use.
Is NBR a hard rubber?
In general, NBR is a hard rubber, but it also depends on the specific grade of material.
Is NBR rubber durable?
Yes, NBR is a durable material for a variety of applications. It is known for its good resistance to abrasion, petroleum oils, crude oil, water, petrol and some hydraulic fluids. The rubber is also stable over a wide temperature range.
Is NBR rubber UV-resistant?
No, NBR rubber is not resistant to UV radiation. It is therefore not recommended for use in outdoor applications where it will be exposed to sunlight.
Is NBR rubber antistatic?
Yes, NBR is a solid-state rubber material that has antistatic properties. These increase as the ACN content in the compound increases.
Is NBR rubber polar?
Yes, NBR rubber is polar. Its polarity is derived from the acrylonitrile unit, and ACN is a highly polar compound because nitrile-CN is a particularly electro-negative group.
Is NBR rubber flammable?
NBR rubber is the least flammable of all dien rubbers. However, this does not change the fact that its fire resistance is poor.
What is the temperature range of NBR rubber?
The temperature range of NBR rubber extends from -50°C to 105°C. However, many experts point out that, in practice, it is better to limit yourself to a range of -40°C to 90°C.
What temperature can NBR rubber withstand?
However, consider that the specific temperature range the rubber can withstand depends on the composition of the polymer, ACN content and other factors.
What are the applications of NBR rubber?
Applications for NBR rubber mainly include hydraulics and pneumatics. The rubber is used for all seals, O-rings and gaskets as well as rubber hoses. Almost any job involving high pressure and compression, as well as contact with oils, is a suitable environment for the use of NBR.
In addition, nitrile is used to produce:
- single-use non-latex gloves,
- automotive transmission belts,
- tyres, inner tubes, bumpers,
- fuel hoses and oil hoses,
- food hoses,
- V-belts,
- synthetic leather,
- rollers for printers,
- cable covers.
NBR latex is also used in the preparation of adhesives and as a pigment binder.
On the other hand, a hydrogenated version of nitrile rubber, HNBR, also known as HSN (highly saturated nitrile), is commonly used to manufacture O-rings for automotive air conditioning systems.
The production process itself is not very complicated. It is true that polymerisation, monomer recovery and coagulation require some additives and equipment, but these are typical of the production of most rubbers. The necessary apparatus is simple and easy to obtain.
For the above reasons, NBR production is popular in poorer countries where labour is relatively cheap. The largest producers of nitrile include mainland China and Taiwan.
Is NBR rubber suitable for water?
Yes, NBR rubber is suitable for water both waste water and drinking water. However, it has average resistance to chlorinated water.
Is NBR suitable for oil?
Yes, NBR is suitable for oil. Thanks to its strong polar nitrile groups, NBR has exceptional resistance to non-polar or low-polar oils such as mineral oil. In addition, it offers reasonable resistance to petroleum, water, petrol and some hydraulic fluids.
What are the trade names of NBR rubber?
The trade names of NBR rubber are as follows:
- Nitrile®,
- Perbunan®,
- BUNA-N®,
- Nipol,
- Krynac,
- Europrene N,
- Breon.
You may also come across the terms oil-resistant rubber, nitrile, nitrile-butadiene rubber.
Who invented NBR rubber?
NBR rubber was invented by two German chemists: Erich Konrad and Eduard Tschunkur. They patented a group of acrylonitrile-butadiene copolymers, known as Buna-N, in 1934 while working for IG Farben . It signified the beginning of commercial production of NBR rubber in Germany.
Buna-N was also produced in the United States during the Second World War as GR-N (Government Rubber-Nitrile). Later, the acrylonitrile-butadiene elastomer group became known as nitrile rubber.
What is the difference between NBR and EPDM rubber?
The main difference between NBR and EPDM rubber is that NBR is a non-aromatic polymer compound, while EPDM is an aromatic polymer. Furthermore, NBR is made using acrylonitrile and butadiene monomers, while EPDM is made using ethylene, propylene and diene comonomer.
NBR is more suitable for oil or petroleum applications, while EPDM is better able to withstand harsh environments and is ideal for outdoor use.
Is NBR a better material than Viton?
NBR is a better material than Viton if you are looking for more flexibility and a lower price. However, Viton performs better in terms of resistance to various chemicals and resistance to high temperatures. Therefore, the particular material you choose depends primarily on your needs.
What are the disadvantages of NBR rubber?
The main disadvantages of NBR rubber are: poor resistance to ozone, weather and sunlight, limited resistance to high temperatures, poor electrical properties, high gas permeability, poor flame resistance. In addition, it is not suitable for working with polar solvents.
However, it is worth noting that some grades of nitrile rubber can be combined with PVC to improve resistance to ageing, flames, petrol and ozone, which combats some of the disadvantages mentioned above. In addition, XNBR has better physical properties and higher temperature resistance.
Is NBR rubber environmentally friendly?
NBR rubber is not considered environmentally friendly. This is primarily due to the fact that it is petroleum-based, the possibilities of recycling rubber are limited and, in addition, the production of the material emits greenhouse gases.
However, it is worth pointing out that efforts are being made to mitigate the environmental impact of synthetic rubbers such as NBR. Some strategies include reducing greenhouse gas emissions during production, introducing renewable sources of raw materials and reducing the amount of rubber in landfills.
Is NBR rubber recyclable?
NBR rubber has limited recycling capabilities compared to other materials due to its complex composition and the presence of additives. However, recent research has focused on developing methods to recycle NBR and improve its mechanical properties.
For example, one study showed that chemo-mechanical devulcanisation can be used to recycle NBR waste and improve the mechanical properties of the resulting rubber.
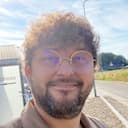
Articles author
Bartosz Kułakowski
CEO of Hosetech Sp. z o.o.
Bartosz Kulakowski is an industrial hoses and couplings specialist with over 10 years of experience. Bartosz has been present in the technical industry since 2013. He gained experience as a technical and commercial advisor in the sector of plastic conveyor belts, steel structures, industrial hoses, and connectors. Since 2016, he has specialized exclusively in hoses and connectors. In 2019 he opened his own business under the HOSETECH Bartosz Kulakowski brand and since July 2022 he has been the CEO of the capital company HOSETECH Sp z o. o. (LLC).
Table of Contents
What is NBR rubber?
Is NBR a natural rubber?
What does NBR stand for?
How is NBR rubber produced?
What are the ingredients of NBR?
What types of NBR rubber are there?
Cold-polymerised NBR
Hot-polymerised NBR
Cross-linked hot-polymerised NBR
Carboxylated nitrile - XNBR rubber
Hydrogenated nitrile – HNBR rubber
NBR bonded with an antioxidant
What does NBR 70 stand for?
What are the properties of NBR rubber?
Is NBR rubber a safe material?
Is NBR a hard rubber?
Is NBR rubber durable?
Is NBR rubber UV-resistant?
Is NBR rubber antistatic?
Is NBR rubber polar?
Is NBR rubber flammable?
What is the temperature range of NBR rubber?
What temperature can NBR rubber withstand?
What are the applications of NBR rubber?
Is NBR rubber suitable for water?
Is NBR suitable for oil?
What are the trade names of NBR rubber?
Who invented NBR rubber?
What is the difference between NBR and EPDM rubber?
Is NBR a better material than Viton?
What are the disadvantages of NBR rubber?
Is NBR rubber environmentally friendly?
Is NBR rubber recyclable?
See also other categories